板料折彎模檢測的重要性與流程解析
板料折彎模作為鈑金加工中的核心工具,其精度和狀態直接影響工件成型質量與生產效率。在長期使用過程中,模具可能因磨損、變形或材料疲勞導致性能下降,因此定期開展系統性檢測是保障生產穩定性的關鍵環節。通過科學的檢測手段,可以精準評估模具可用性,預測維修周期,避免因模具失效引發的批量性質量問題,同時延長模具使用壽命,降低企業綜合成本。
核心檢測項目清單
1. 模具材質檢測
采用光譜分析儀驗證模具材料成分是否符合設計要求,重點檢測Cr、Mo、V等合金元素含量,確保材料具備足夠的耐磨性和抗沖擊性能。對于高頻次使用的精密模具,需特別注意表面滲碳/氮化層的厚度均勻性檢測。
2. 尺寸精度檢測
使用三坐標測量儀對關鍵尺寸進行全尺寸掃描,包括:上下模閉合高度、V型開口尺寸、導向槽配合間隙等,允許公差需嚴格控制在±0.02mm以內。對于復雜曲面模具,需配合3D掃描技術進行三維形貌比對。
3. 表面粗糙度檢測
通過表面輪廓儀測量模具工作面的Ra值,重點區域粗糙度應≤0.4μm。過高的粗糙度會導致板材表面劃傷,同時影響脫模性能;而異常過低的數值可能掩蓋細微裂紋缺陷。
4. 硬度檢測
采用洛氏硬度計(HRC)多點檢測模具工作面硬度,確保硬度值在58-62HRC范圍內。特別注意硬度梯度的合理性,避免出現表面硬度過高導致的脆性斷裂風險。
5. 角度與弧度檢驗
使用專用角度規和半徑樣板檢測成型部位的幾何特征,對于多段折彎模具需逐段驗證角度過渡區的連續性。針對彈性回彈補償設計,需通過試折驗證實際成型角度與理論值偏差。
6. 導向機構檢測
檢查導柱/導套的配合間隙(應≤0.015mm),檢測復位彈簧的壓縮力衰減情況。對于液壓式模具,需同步檢測液壓缸的同步精度和保壓性能。
7. 刃口狀態評估
使用20倍以上工業顯微鏡檢查刃口是否存在崩刃、卷邊等缺陷,測量刃口圓角半徑變化。當圓角半徑超過設計值30%時,需立即進行修復處理。
8. 裝配精度驗證
在專用檢測平臺上進行動態合模測試,使用激光位移傳感器監測上下模的平行度誤差(≤0.03mm/m),同時檢測模具整體的水平度與緊固螺栓的預緊力均勻性。
9. 殘余應力檢測
采用X射線衍射法檢測模具內部殘余應力分布,重點分析應力集中區域。對于應力值超過材料屈服強度35%的模具,必須進行去應力退火處理。
檢測周期與注意事項
建議每完成5000-8000次沖壓進行預防性檢測,在連續高強度使用時應縮短至2000次/次。檢測過程需嚴格遵循溫度補償原則(20±1℃),檢測后需建立完整的模具健康檔案,包含3D數字孿生模型和維修履歷記錄。通過實施標準化檢測流程,可使模具故障率降低60%以上,顯著提升產線綜合OEE指標。

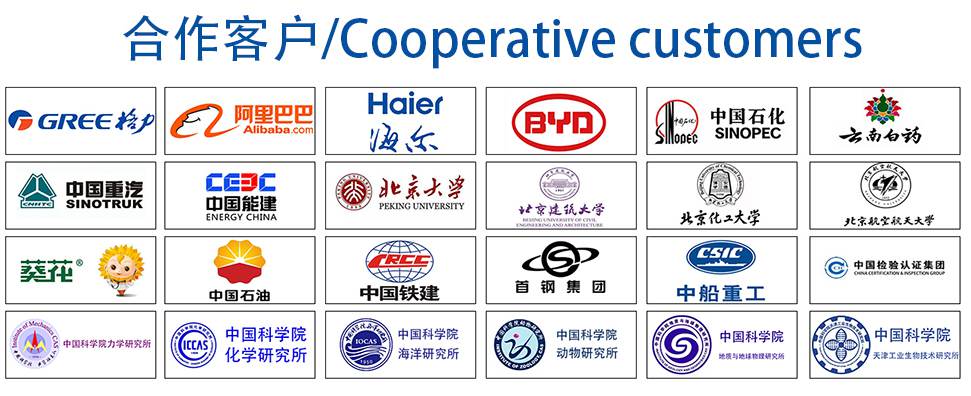