工業用鋰電池檢測
實驗室擁有眾多大型儀器及各類分析檢測設備,研究所長期與各大企業、高校和科研院所保持合作伙伴關系,始終以科學研究為首任,以客戶為中心,不斷提高自身綜合檢測能力和水平,致力于成為全國科學材料研發領域服務平臺。
立即咨詢工業用鋰電池檢測的重要性及核心關注點
隨著新能源技術的快速發展,工業用鋰電池在儲能系統、電動車輛、通信基站、航空航天等領域的應用日益廣泛。然而,鋰電池的高能量密度特性也帶來了熱失控、短路、爆炸等潛在風險。為確保其安全性、可靠性和長壽命,工業用鋰電池的檢測成為生產制造和使用環節中不可或缺的環節。通過科學的檢測流程,能夠驗證電池性能是否符合國家標準(如GB/T 36276、UN38.3等)和國際規范(如IEC 62133),同時為產品質量追溯和故障分析提供依據。
工業鋰電池檢測的核心項目
1. 安全性能檢測
安全測試是鋰電池檢測的重中之重,主要包括: ? 過充/過放測試:模擬異常充放電場景,驗證電池保護機制的有效性; ? 短路測試:檢測電池在極端短路情況下的熱穩定性和防爆能力; ? 針刺與擠壓測試:評估機械破壞下的內部結構抗損性; ? 高溫/低溫耐受測試:檢驗電池在-40℃至85℃極端環境下的工作安全性; ? 熱失控分析:通過加熱觸發電池失效,研究熱擴散路徑及防護設計。
2. 電化學性能檢測
此類測試關注電池的實用效能,涵蓋: ? 容量與能量密度:測量實際放電容量與標稱值的偏差; ? 循環壽命測試:模擬長期充放電(如1000次循環)后的容量衰減率; ? 內阻與自放電率:評估電池存儲過程中的能量損耗; ? 倍率充放電性能:驗證高倍率(如2C、5C)下的電池穩定性。
3. 環境適應性檢測
針對不同工業場景的特殊需求,需進行: ? 振動與沖擊測試:模擬運輸或設備運行中的機械應力影響; ? 鹽霧與濕度測試:驗證沿海或高濕環境下的耐腐蝕性能; ? 高海拔低氣壓測試:評估在高原/航空環境中的氣體膨脹風險。
4. 結構及材料分析
通過CT掃描、SEM顯微鏡等手段,檢測電極涂覆均勻性、隔膜完整性、電解液分布等微觀結構問題,同時分析正負極材料成分是否符合設計要求。
5. 生產一致性檢測
對同一批次電池進行電壓、內阻、尺寸等參數的統計抽樣檢測,確保量產產品的一致性,降低因制造偏差導致的系統性風險。
檢測技術與標準演進趨勢
隨著固態電池、鈉離子電池等新技術的涌現,檢測項目持續升級。例如,針對固態電解質的界面穩定性測試、快充場景下的析鋰監測等新型需求,國際機構正在制定更細化的測試標準。同時,AI驅動的智能檢測系統和在線監測技術,正在提升檢測效率和數據追溯能力。
工業用鋰電池的檢測不僅是合規要求,更是保障產業鏈安全的核心防線。通過多維度的科學評估,企業可有效降低應用風險,推動新能源技術的高質量發展。

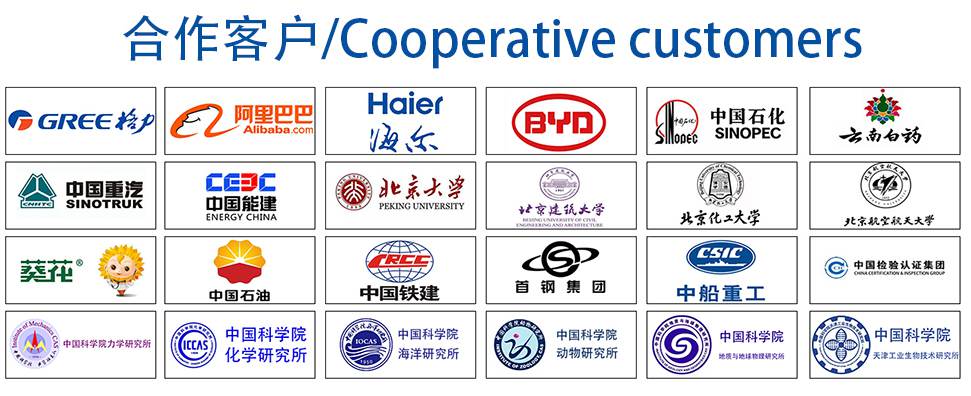