工程機械 高溫高壓液壓軟管總成檢測
實驗室擁有眾多大型儀器及各類分析檢測設備,研究所長期與各大企業、高校和科研院所保持合作伙伴關系,始終以科學研究為首任,以客戶為中心,不斷提高自身綜合檢測能力和水平,致力于成為全國科學材料研發領域服務平臺。
立即咨詢工程機械高溫高壓液壓軟管總成檢測的重要性
在工程機械領域,液壓系統是實現動力傳輸與精準控制的核心部件,而高溫高壓液壓軟管總成作為連接油泵、閥門和執行機構的關鍵元件,其性能直接影響設備的安全性與可靠性。尤其在礦山機械、盾構機、起重設備等重載工況下,軟管總成需長期承受超100℃的高溫、40MPa以上的高壓以及頻繁的脈沖沖擊。若軟管出現老化、破裂或密封失效,輕則導致液壓系統漏油、效率下降,重則引發設備停機甚至安全事故。因此,建立科學的高溫高壓液壓軟管總成檢測體系,是保障工程機械運行安全與延長使用壽命的必要措施。
核心檢測項目及技術要求
1. 外觀與尺寸檢查
通過目測與精密測量工具對軟管總成的外觀缺陷(如裂紋、鼓包、劃痕)及關鍵尺寸(內徑、壁厚、接頭安裝角度)進行全面檢測。依據ISO 1307、SAE J517等標準,確認軟管表面無局部膨脹或變形,橡膠層與鋼絲編織層貼合緊密,接頭處無銹蝕或裝配錯位現象。
2. 耐壓性能測試
采用液壓脈沖試驗機模擬實際工況,進行靜壓試驗(1.5倍工作壓力保持3分鐘)和脈沖試驗(頻率1Hz,壓力波動范圍±15%)。記錄軟管在500萬次循環后的滲漏、爆裂情況及膨脹率變化,確保符合DIN EN 853/856標準中對壓力衰減率≤5%的要求。
3. 高溫老化測試
將軟管總成置于120℃±5℃的高溫箱中連續暴露72小時,隨后進行低溫脆性試驗(-40℃冷凍2小時)。測試后檢查橡膠層硬度變化(邵氏A型硬度差值≤15)、屈撓性能及接頭密封性,驗證材料抗熱氧老化與耐低溫性能。
4. 動態彎曲疲勞測試
通過伺服驅動裝置模擬軟管在設備運動中的彎曲工況,以每分鐘10次的頻率進行±90°往復彎曲測試。記錄軟管在10萬次循環后是否出現外層龜裂、鋼絲層斷裂或接頭松動,彎曲半徑需符合GB/T 3683規定的動態彎曲壽命指標。
5. 介質兼容性驗證
將軟管浸泡在特定液壓油(如HLP46、HV46)中48小時,檢測橡膠層體積膨脹率(≤10%)及抗溶脹性能。同時結合紅外光譜分析,確認橡膠材料未發生化學降解,防止因油液腐蝕導致軟管強度下降。
6. 爆破壓力測試
在液壓試驗臺上以3MPa/s的速率逐步增壓至軟管爆破,實測爆破壓力需≥4倍額定工作壓力。通過高速攝像機記錄爆破形態,分析失效模式(軸向撕裂或徑向分層)以優化結構設計。
檢測設備與數據管理
檢測過程需配備高精度壓力傳感器(誤差≤±0.25%FS)、熱電偶溫度采集系統(分辨率0.1℃)及三維運動模擬平臺。采用MES系統整合檢測數據,建立軟管總成全生命周期數據庫,通過SPC統計過程控制實現質量趨勢預警,為工程機械制造商提供選型優化與預防性維護依據。

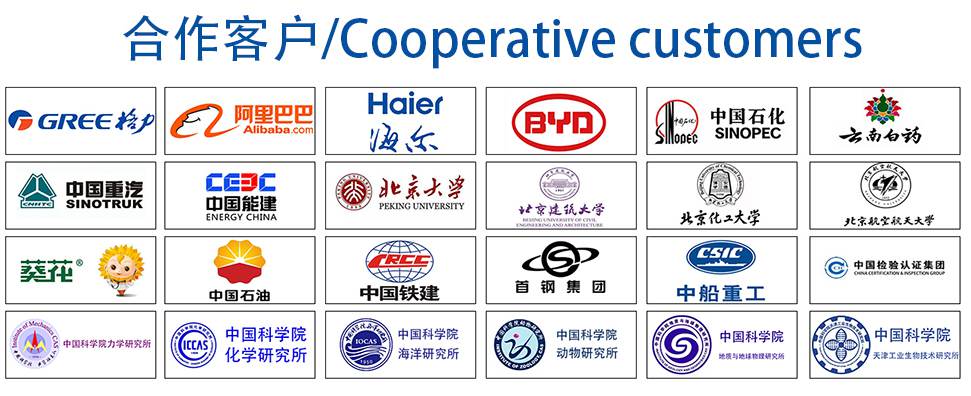