噴油泵試驗(yàn)臺(tái)檢測(cè)
實(shí)驗(yàn)室擁有眾多大型儀器及各類(lèi)分析檢測(cè)設(shè)備,研究所長(zhǎng)期與各大企業(yè)、高校和科研院所保持合作伙伴關(guān)系,始終以科學(xué)研究為首任,以客戶(hù)為中心,不斷提高自身綜合檢測(cè)能力和水平,致力于成為全國(guó)科學(xué)材料研發(fā)領(lǐng)域服務(wù)平臺(tái)。
立即咨詢(xún)聯(lián)系中化所
噴油泵試驗(yàn)臺(tái)檢測(cè)的重要性與核心內(nèi)容
噴油泵作為柴油發(fā)動(dòng)機(jī)燃油系統(tǒng)的核心部件,其性能直接影響發(fā)動(dòng)機(jī)的動(dòng)力輸出、燃油經(jīng)濟(jì)性和排放標(biāo)準(zhǔn)。噴油泵試驗(yàn)臺(tái)檢測(cè)是通過(guò)專(zhuān)業(yè)設(shè)備對(duì)噴油泵各項(xiàng)參數(shù)進(jìn)行系統(tǒng)性測(cè)試的過(guò)程,能夠有效評(píng)估其工作狀態(tài)、校準(zhǔn)精度和耐久性。在發(fā)動(dòng)機(jī)維修、生產(chǎn)質(zhì)檢及研發(fā)改進(jìn)環(huán)節(jié)中,這項(xiàng)檢測(cè)技術(shù)對(duì)保障噴油泵與發(fā)動(dòng)機(jī)系統(tǒng)的匹配性具有不可替代的作用。隨著電控高壓共軌技術(shù)的發(fā)展,現(xiàn)代噴油泵試驗(yàn)臺(tái)已集成計(jì)算機(jī)控制、高精度傳感和智能數(shù)據(jù)分析功能,使檢測(cè)項(xiàng)目更加全面且結(jié)果更具參考價(jià)值。
噴油泵試驗(yàn)臺(tái)核心檢測(cè)項(xiàng)目解析
1. 密封性檢測(cè)
通過(guò)加壓試驗(yàn)檢測(cè)柱塞偶件、出油閥等關(guān)鍵部位的密封性能,使用壓力表監(jiān)測(cè)保壓階段的壓力衰減值。該項(xiàng)檢測(cè)可發(fā)現(xiàn)早期磨損或裝配缺陷,防止燃油泄漏導(dǎo)致的供油壓力不足。
2. 供油量檢測(cè)
在不同轉(zhuǎn)速和負(fù)荷工況下,測(cè)量各缸噴油泵的供油均勻性。采用精密量筒收集標(biāo)準(zhǔn)循環(huán)次數(shù)下的噴油量,要求各缸偏差不超過(guò)±3%。該指標(biāo)直接影響發(fā)動(dòng)機(jī)運(yùn)轉(zhuǎn)平穩(wěn)性。
3. 噴油壓力測(cè)試
利用壓力傳感器記錄噴油器開(kāi)啟壓力、最高噴射壓力及壓力波動(dòng)曲線(xiàn)。電控噴油泵需額外驗(yàn)證ECU控制信號(hào)的響應(yīng)特性,確保壓力調(diào)節(jié)精度符合設(shè)計(jì)要求。
4. 噴油正時(shí)校準(zhǔn)
通過(guò)頻閃儀或電子角度儀檢測(cè)噴油提前角,比對(duì)設(shè)計(jì)值與實(shí)際值的偏差。對(duì)于可調(diào)式噴油泵,需進(jìn)行動(dòng)態(tài)調(diào)整并驗(yàn)證修正效果。
5. 調(diào)速特性測(cè)試
模擬發(fā)動(dòng)機(jī)轉(zhuǎn)速變化,檢測(cè)調(diào)速器對(duì)供油量的控制能力。重點(diǎn)分析怠速穩(wěn)定性、標(biāo)定轉(zhuǎn)速保持性以及超速斷油功能的可靠性。
6. 耐久性驗(yàn)證
在連續(xù)工況下進(jìn)行500-1000小時(shí)壽命試驗(yàn),監(jiān)測(cè)關(guān)鍵參數(shù)的變化趨勢(shì)。記錄密封件磨損量、金屬疲勞等數(shù)據(jù),評(píng)估噴油泵的長(zhǎng)期使用可靠性。
7. 智能化診斷分析
現(xiàn)代試驗(yàn)臺(tái)配備的檢測(cè)系統(tǒng)可實(shí)現(xiàn):①異常噴射波形識(shí)別 ②故障代碼解析 ③性能退化趨勢(shì)預(yù)測(cè) ④檢測(cè)報(bào)告自動(dòng)生成。通過(guò)數(shù)據(jù)模型對(duì)比歷史檢測(cè)記錄,大幅提升故障定位效率。
檢測(cè)技術(shù)發(fā)展趨勢(shì)
當(dāng)前噴油泵試驗(yàn)臺(tái)正朝著多參數(shù)同步采集、虛擬仿真測(cè)試、AI智能診斷方向發(fā)展。通過(guò)集成3D光學(xué)測(cè)量、納米級(jí)泄漏檢測(cè)等新技術(shù),檢測(cè)精度已提升至微米級(jí)。未來(lái)檢測(cè)系統(tǒng)將深度融入工業(yè)物聯(lián)網(wǎng),實(shí)現(xiàn)檢測(cè)數(shù)據(jù)與生產(chǎn)/服務(wù)環(huán)節(jié)的實(shí)時(shí)交互,為智能維保提供數(shù)據(jù)支撐。

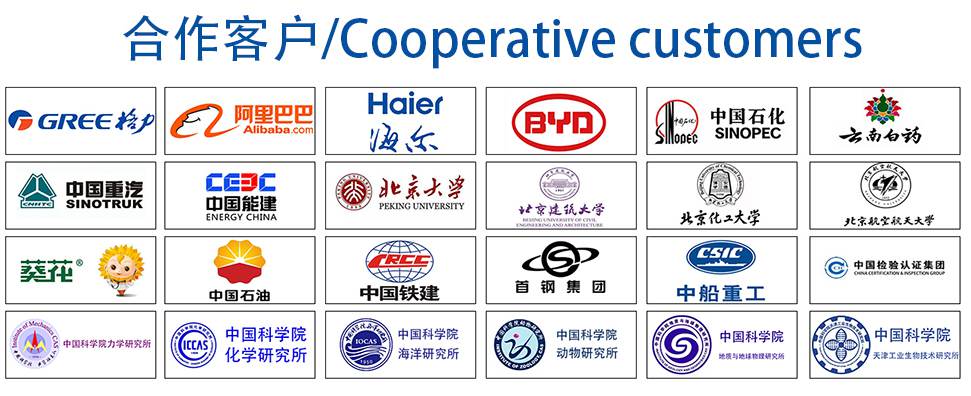