插齒機檢測
實驗室擁有眾多大型儀器及各類分析檢測設備,研究所長期與各大企業、高校和科研院所保持合作伙伴關系,始終以科學研究為首任,以客戶為中心,不斷提高自身綜合檢測能力和水平,致力于成為全國科學材料研發領域服務平臺。
立即咨詢插齒機檢測:保障齒輪加工精度的核心環節
插齒機作為齒輪加工領域的關鍵設備,其性能直接影響齒輪的齒形精度、表面質量和生產效率。隨著制造業對精密齒輪需求的不斷提升,插齒機的定期檢測與維護已成為企業質量控制體系中的重要環節。通過系統性檢測,可有效發現設備潛在故障、校準加工參數偏差,從而避免因設備性能衰減導致的批量質量事故。本文將從插齒機的核心檢測項目出發,詳細解析各項檢測指標的標準要求及實施方法,為設備管理人員提供技術參考。
一、幾何精度檢測
作為基礎檢測項目,需使用激光干涉儀和電子水平儀對機床導軌平行度、主軸徑向跳動、工作臺平面度進行測量。重點檢查:①主軸軸線與工作臺面的垂直度誤差(GB/T 9061標準要求≤0.01mm/300mm);②刀架滑枕運動軌跡的直線度(ISO 230-1標準規定允差為±3μm);③工作臺分度裝置的定位精度(通常要求≤5角秒)。
二、運動精度檢測
通過球桿儀檢測X/Y/Z軸聯動精度,驗證插齒機的復合運動性能:①主軸往復運動速度穩定性需控制在±2%以內;②徑向進給系統的重復定位精度應≤0.005mm;③圓周進給機構的分度精度需通過標準齒輪樣板件進行對比測試,齒距累積誤差須符合DIN 3962標準6級精度要求。
三、加工性能驗證
使用標準試件(通常為模數3-5的直齒輪)進行切削試驗:①采用三坐標測量機檢測加工齒輪的齒形誤差(漸開線偏差≤8μm)、齒向誤差(螺旋線偏差≤10μm);②使用表面粗糙度儀評估齒面Ra值(應≤1.6μm);③連續加工20件驗證設備穩定性,尺寸極差需控制在公差帶的30%以內。
四、液壓與潤滑系統檢測
通過壓力傳感器監測液壓系統:①主油路壓力波動需≤±0.5MPa;②刀架平衡缸壓力應與設定值偏差<5%;③潤滑油膜厚度需通過超聲波測厚儀驗證,確保導軌面油膜≥8μm。對冷卻液進行定期取樣檢測,顆粒污染物濃度需符合ISO 4406 17/15/12標準。
五、安全防護功能測試
重點驗證:①急停裝置響應時間≤0.2秒;②防護門聯鎖開關的斷開行程≤1mm;③過載保護系統的觸發閾值誤差<5%。需使用專業檢測設備模擬超程、過載等異常工況,確保所有安全裝置符合GB 5226.1機械電氣安全標準。
建議企業建立季度檢測制度,結合加工量每3000小時進行預防性維護。通過實施全面檢測體系,插齒機的平均故障間隔時間(MTBF)可提升40%以上,同時將齒輪加工合格率穩定在99.5%以上,有效支撐高精度齒輪的批量化生產需求。

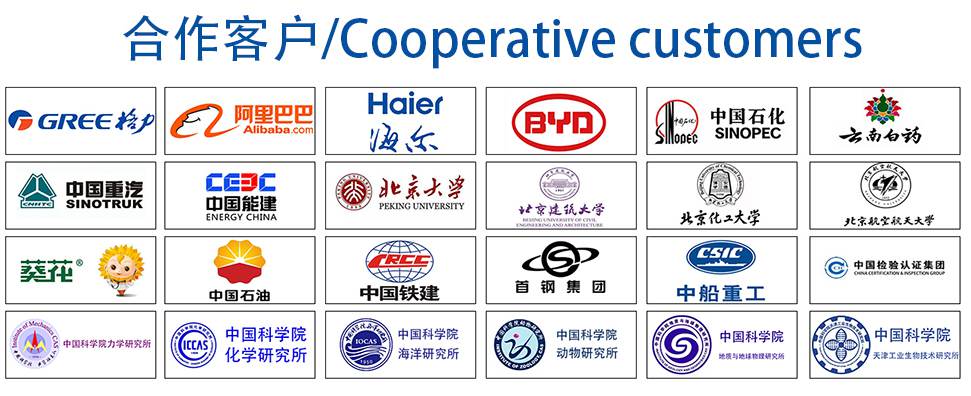