輪胎式裝載機(jī)用傳動(dòng)軸檢測(cè)
實(shí)驗(yàn)室擁有眾多大型儀器及各類分析檢測(cè)設(shè)備,研究所長(zhǎng)期與各大企業(yè)、高校和科研院所保持合作伙伴關(guān)系,始終以科學(xué)研究為首任,以客戶為中心,不斷提高自身綜合檢測(cè)能力和水平,致力于成為全國(guó)科學(xué)材料研發(fā)領(lǐng)域服務(wù)平臺(tái)。
立即咨詢聯(lián)系中化所
輪胎式裝載機(jī)用傳動(dòng)軸檢測(cè)的重要性與核心內(nèi)容
輪胎式裝載機(jī)作為工程機(jī)械領(lǐng)域的關(guān)鍵設(shè)備,其傳動(dòng)系統(tǒng)直接關(guān)系到整機(jī)的動(dòng)力傳輸效率與作業(yè)穩(wěn)定性。傳動(dòng)軸作為動(dòng)力從發(fā)動(dòng)機(jī)到驅(qū)動(dòng)橋的核心連接部件,長(zhǎng)期承受高扭矩、交變載荷及復(fù)雜工況的考驗(yàn)。若傳動(dòng)軸存在缺陷或性能下降,輕則導(dǎo)致設(shè)備動(dòng)力損失、能耗增加,重則引發(fā)機(jī)械故障甚至安全事故。因此,對(duì)傳動(dòng)軸進(jìn)行系統(tǒng)性檢測(cè)是保障裝載機(jī)安全運(yùn)行、延長(zhǎng)設(shè)備壽命的必要技術(shù)手段。通過科學(xué)的檢測(cè)流程,可精準(zhǔn)評(píng)估傳動(dòng)軸的機(jī)械性能、動(dòng)態(tài)平衡性和耐久度,為維修、更換或優(yōu)化設(shè)計(jì)提供可靠依據(jù)。
傳動(dòng)軸檢測(cè)的核心項(xiàng)目與技術(shù)要求
1. 外觀與尺寸精度檢測(cè)
采用目視檢查與量具測(cè)量相結(jié)合的方式,重點(diǎn)檢測(cè)軸體表面是否存在裂紋、凹陷、銹蝕或過度磨損現(xiàn)象。使用三坐標(biāo)測(cè)量?jī)x對(duì)傳動(dòng)軸的同軸度、法蘭盤端面跳動(dòng)等關(guān)鍵尺寸進(jìn)行精密測(cè)量,確保尺寸公差符合GB/T 1184-1996標(biāo)準(zhǔn)(同軸度誤差≤0.08mm,軸徑磨損量≤原尺寸的2%)。
2. 動(dòng)平衡性能測(cè)試
通過動(dòng)平衡試驗(yàn)機(jī)在額定轉(zhuǎn)速(通常1200-2000rpm)下進(jìn)行旋轉(zhuǎn)測(cè)試,使用激光傳感器捕捉不平衡量。按照J(rèn)B/T 7917-2018規(guī)范要求,傳動(dòng)軸殘余不平衡量應(yīng)控制在≤15g·cm范圍內(nèi),避免高速運(yùn)轉(zhuǎn)時(shí)引發(fā)異常振動(dòng)。
3. 扭矩承載能力驗(yàn)證
采用液壓扭矩加載裝置模擬實(shí)際工況,分階段施加0-150%標(biāo)定扭矩(典型值12000N·m)。記錄各階段的彈性變形量,繪制扭矩-扭角曲線,確保最大工作扭矩下扭轉(zhuǎn)角變化率≤0.25°/m,極限扭矩時(shí)無塑性變形。
4. 材料性能分析
通過超聲波探傷(UT)和磁粉探傷(MT)檢測(cè)焊縫及關(guān)鍵部位內(nèi)部缺陷,使用光譜分析儀驗(yàn)證材料成分(如40CrMo鋼需滿足C:0.37-0.44%,Cr:0.9-1.2%)。布氏硬度測(cè)試要求基體硬度達(dá)到HB280-320,花鍵表面經(jīng)高頻淬火后硬度≥HRC50。
5. 密封性與潤(rùn)滑評(píng)估
對(duì)十字軸萬向節(jié)進(jìn)行3bar氣壓密封測(cè)試,保壓5分鐘泄漏量≤0.5%。檢查注油通道暢通性,確認(rèn)潤(rùn)滑脂填充量達(dá)到腔體容積的85%,確保長(zhǎng)期運(yùn)行時(shí)的有效潤(rùn)滑。
6. 疲勞壽命試驗(yàn)
在專用試驗(yàn)臺(tái)上進(jìn)行循環(huán)載荷測(cè)試,模擬裝載機(jī)典型作業(yè)工況(載荷波動(dòng)頻率2-5Hz)。要求傳動(dòng)軸在交變扭矩(±80%額定值)下通過≥1×10?次循環(huán)無裂紋產(chǎn)生,驗(yàn)證其抗疲勞性能是否符合ISO 6336標(biāo)準(zhǔn)。
智能化檢測(cè)技術(shù)的新發(fā)展
隨著物聯(lián)網(wǎng)技術(shù)的應(yīng)用,部分企業(yè)已引入在線監(jiān)測(cè)系統(tǒng),通過在傳動(dòng)軸安裝振動(dòng)傳感器(采樣頻率≥10kHz)和溫度傳感器,實(shí)時(shí)采集運(yùn)行數(shù)據(jù)并構(gòu)建健康評(píng)估模型。結(jié)合大數(shù)據(jù)分析,可提前30-50工作小時(shí)預(yù)警潛在故障,檢測(cè)效率較傳統(tǒng)方法提升40%以上。

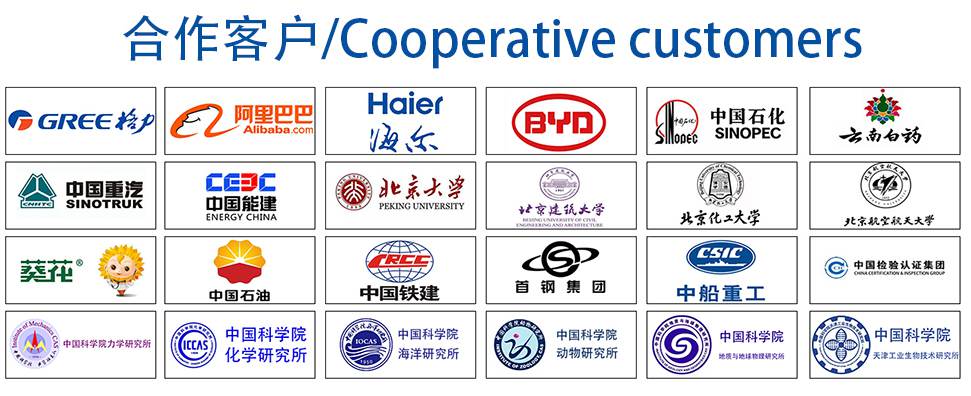