乘用車及其拖車用車輪檢測
實驗室擁有眾多大型儀器及各類分析檢測設備,研究所長期與各大企業、高校和科研院所保持合作伙伴關系,始終以科學研究為首任,以客戶為中心,不斷提高自身綜合檢測能力和水平,致力于成為全國科學材料研發領域服務平臺。
立即咨詢乘用車及其拖車用車輪檢測的重要性
車輪作為車輛與地面直接接觸的核心部件,其性能直接關系到行車安全、燃油效率及駕駛體驗。隨著汽車工業的快速發展,乘用車及其拖車用車輪的制造工藝和材料技術不斷革新,但同時也對質量控制提出了更高要求。車輪檢測不僅需要驗證其結構強度、耐久性和動平衡能力,還需評估極端工況下的可靠性。據統計,因車輪質量問題引發的交通事故中,約30%與輪轂斷裂、變形或動平衡失準相關。因此,國際標準化組織(ISO)、各國汽車工程協會及整車制造商均制定了嚴格的檢測標準,覆蓋從原材料到成品、從實驗室到實際路況的多維度測試體系。
核心檢測項目與技術規范
1. 結構強度測試
通過彎曲疲勞試驗、徑向載荷試驗和沖擊試驗,模擬車輪在高速行駛、過載或遭遇路面沖擊時的受力狀態。例如,ISO 3006標準要求車輪需承受10^6次循環載荷測試,檢測是否發生裂紋或永久變形。試驗中需使用液壓伺服系統精確控制加載力,并通過應變片實時監測應力分布。
2. 動平衡測試
采用高精度動平衡機檢測車輪質量分布均勻性,殘余不平衡量需符合GB/T 18505或SAE J267標準。測試時車輪以額定轉速旋轉,系統自動識別并標記不平衡點,指導配重塊的安裝。動態不平衡量過大可能導致車輛抖動、輪胎異常磨損,甚至影響懸掛系統壽命。
3. 尺寸精度檢測
使用三坐標測量儀(CMM)或激光掃描儀進行三維幾何檢測,包括輪輞直徑、偏距(ET值)、中心孔公差、螺栓孔分布圓(PCD)等關鍵參數。根據DIN 7817標準,輪輞徑向跳動量需控制在0.6mm以內,軸向跳動量不超過1.0mm,確保與輪胎的裝配密封性。
4. 材料性能測試
通過金相分析、硬度測試和拉伸試驗驗證鋁合金/鋼制輪轂的化學成分、晶粒結構和機械性能。例如,鍛造鋁合金輪轂的抗拉強度需達到320MPa以上,延伸率不低于8%。X射線探傷技術可檢測內部氣孔、夾雜物等缺陷,避免應力集中導致的早期失效。
5. 疲勞壽命與耐腐蝕性測試
在鹽霧試驗箱中模擬5-10年使用環境,評估涂層附著力及抗腐蝕能力。同時執行臺架耐久試驗,模擬車輛在復雜路況下的長期使用,要求車輪在完成等效20萬公里測試后無功能性損傷。部分高端車型還需通過-30℃低溫沖擊試驗,驗證極端溫度下的材料韌性。
智能化檢測技術發展
隨著工業4.0的推進,基于機器視覺的在線檢測系統已被應用于輪轂生產線,實現缺陷實時識別與數據追溯。人工智能算法可分析海量檢測數據,優化工藝參數并預測產品壽命。例如,采用深度學習技術識別X射線圖像中的微裂紋,檢測精度可達99.7%,相比傳統方法效率提升40%以上。
通過上述多維度的檢測體系,車企可有效控制車輪質量風險,同時推動輕量化、高強度的新型車輪材料研發。未來,隨著新能源車對續航里程的嚴苛要求以及自動駕駛對安全性的極致追求,車輪檢測技術將持續向高精度、智能化和全生命周期管理方向演進。

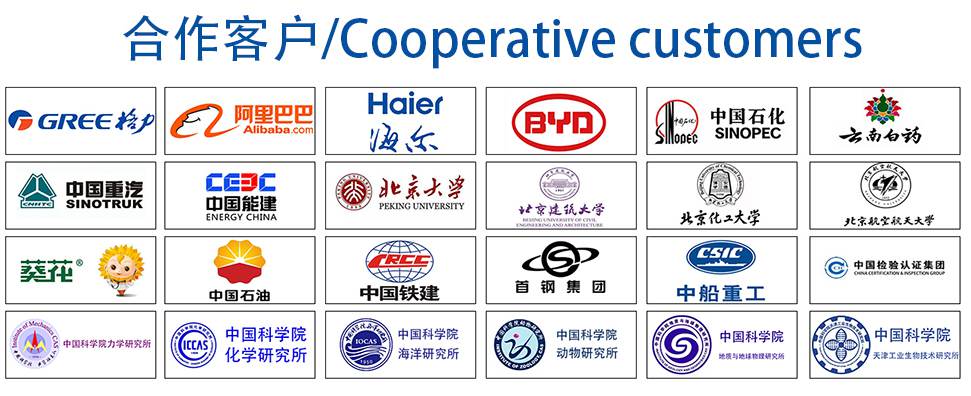