充氣輪胎內胎摩托車輪胎內胎檢測的重要性
摩托車輪胎內胎作為車輛與地面直接接觸的核心部件,其性能直接關系到騎行安全、操控穩定性和使用壽命。隨著摩托車使用場景的多樣化(如城市通勤、越野騎行、長途旅行等),對內胎的耐壓性、氣密性、抗老化能力等提出了更高要求。因此,針對充氣輪胎內胎的檢測項目已成為生產質量控制、產品認證及售后問題分析的關鍵環節。通過科學系統的檢測,可以確保內胎符合國家標準(如GB/T 519-2017《充氣輪胎內胎》)及國際規范,同時幫助制造商優化材料配方和生產工藝。
核心檢測項目及標準要求
1. 氣密性測試
通過浸水試驗或壓力保持試驗檢測內胎的氣密性。將充氣至標準壓力(通常為最大設計氣壓的150%)的內胎浸入水中,觀察是否出現連續氣泡,或記錄保壓狀態下氣壓下降速率,要求30分鐘內壓降不超過初始值的10%。
2. 物理機械性能檢測
- 拉伸強度測試:測定橡膠材料在拉伸狀態下的斷裂強度(≥14MPa)
- 扯斷伸長率(≥400%)
- 硬度測試(邵氏A型硬度60-80)
- 撕裂強度測試(≥30kN/m)
使用萬能材料試驗機按照GB/T 528標準進行,確保內胎在復雜應力下的抗破壞能力。
3. 耐老化性能測試
模擬長期使用環境,進行70℃×72h熱空氣老化試驗后,要求拉伸強度變化率≤±30%,伸長率變化率≤±50%。通過紫外老化試驗評估抗臭氧能力,避免橡膠龜裂。
特殊工況適應性檢測
4. 極端溫度耐受性測試
- 低溫脆性測試:-40℃條件下保持5小時后彎曲180°無裂紋
- 高溫膨脹測試:100℃環境存放48小時,尺寸變化率≤5%
5. 動態耐久性試驗
在轉鼓試驗機上模擬實際騎行,以標準載荷的1.2倍、速度60km/h連續運行72小時,檢測內胎是否出現異常變形、簾線斷裂或接頭開裂。
材料與工藝專項檢測
6. 橡膠配方分析
通過紅外光譜(FTIR)和熱重分析(TGA)檢測天然橡膠/合成橡膠配比(通常NR含量≥60%),確認防老劑(如4010NA)、補強劑(炭黑)等添加劑的含量符合設計要求。
7. 接合部位強度檢測
對接頭部位進行剝離強度測試(≥6.0kN/m),采用X射線檢測接合面氣泡缺陷,確保硫化工藝參數(溫度143±2℃、壓力2.0MPa、時間15min)的精確控制。
檢測結果的應用與改進
通過系統檢測數據可繪制質量控制圖,對氣門嘴與胎體粘合強度(≥80N)、胎身厚度均勻性(偏差≤0.2mm)等關鍵指標進行SPC統計過程控制。對于檢測中發現的典型問題,如局部薄區、簾線排列不勻等,可反向優化壓延工藝參數和成型定位精度,提升產品合格率至99.5%以上。

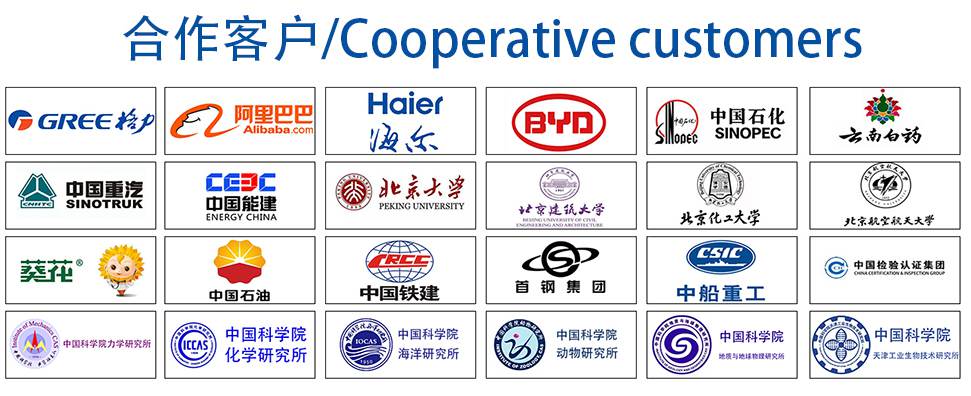