直徑和長度檢測
實驗室擁有眾多大型儀器及各類分析檢測設備,研究所長期與各大企業、高校和科研院所保持合作伙伴關系,始終以科學研究為首任,以客戶為中心,不斷提高自身綜合檢測能力和水平,致力于成為全國科學材料研發領域服務平臺。
立即咨詢直徑和長度檢測技術白皮書
在高端制造與精密加工領域,產品尺寸的精確控制是決定工業品性能與可靠性的核心要素。據中國機械工業聯合會2024年數據顯示,國內精密零部件市場規模已達2.3萬億元,其中因尺寸偏差導致的次品損失占比超過12%。在此背景下,直徑和長度檢測作為質量管控的關鍵環節,正從傳統人工抽檢向智能化全檢模式升級。該項目通過集成高精度非接觸式測量技術與工業級視覺識別系統,實現微米級尺寸偏差的實時監控,其核心價值在于突破傳統檢測效率瓶頸,將產線檢測速度提升300%的同時,確保關鍵尺寸參數合格率達到99.97%。這一技術革新不僅為航空航天、新能源汽車等戰略性產業提供質量保障,更助力企業構建全流程質量追溯系統,推動智能制造轉型。
技術原理與測量方法創新
現代直徑和長度檢測技術融合了光學干涉、激光三角測量及深度學習算法三重優勢。基于雙頻激光干涉儀的基準校準系統可達到0.1μm的重復測量精度,而復合式結構光投影技術通過相位解算實現曲面特征的精確重構。值得注意的是,針對深孔類零件的內徑檢測難題,企業已開發出搭載光纖傳感器的內窺式測量裝置,其蛇形探頭可深入直徑3mm的孔道完成360°全周掃描。據國家精密測量技術重點實驗室測試報告,該方案對渦輪葉片冷卻孔的直徑檢測誤差控制在±2μm以內。
智能化檢測實施流程
具體實施層面,系統采用模塊化架構設計,兼容在線式與離線式檢測場景。在汽車轉向節自動化產線中,檢測工位部署了六軸協作機器人搭載的激光輪廓儀,通過預設的運動軌跡對工件進行多截面掃描。數據采集系統實時處理點云數據,依托特征匹配算法在500ms內完成直徑、長度等12項尺寸參數的合格判定。當檢測到超差工件時,系統自動觸發分揀指令并與MES系統聯動更新生產批次數據。某新能源汽車企業應用該方案后,產線檢測節拍從45秒/件縮短至8秒/件,人工復檢工作量減少80%。
行業應用與質量提升實踐
在航空航天領域,某發動機葉片制造商采用多光譜共焦傳感器陣列,成功解決了高溫合金葉尖尺寸的在線檢測難題。通過在真空熱處理爐出口處布設檢測單元,系統能在葉片溫度800℃條件下實現直徑公差0.005mm的精確測量。該方案使葉片裝配合格率從92.4%提升至99.1%,據企業2023年質量年報顯示,單此項目實現年度質量成本降低2700萬元。值得關注的是,在醫療器械行業,用于人工關節球頭直徑檢測的恒溫控制測量室,通過環境補償算法消除溫度波動影響,使測量結果不確定度降低至0.3μm以下。
全周期質量保障體系構建
為確保檢測系統的長效穩定性,企業需建立三級質量保障機制?;A層采用NIST溯源的標準量塊進行日點檢校準,中間層部署機器學習驅動的設備健康預測系統,通過分析傳感器信號頻譜特征預判設備劣化趨勢。頂層質量管控則依托區塊鏈技術,將檢測數據與工藝參數加密上鏈,實現檢測過程的可信存證。某軸承龍頭企業通過該體系,將測量系統重復性與再現性(GR&R)指標控制在5%以內,大幅優于行業10%的通用標準。
展望未來,隨著量子傳感技術與工業元宇宙的深度融合,直徑和長度檢測將向納米級精度與虛擬孿生方向發展。建議行業重點攻關跨尺度測量技術,開發適應柔性制造需求的自主進化檢測系統,同時加強ASTM/ISO標準體系的國產化適配。企業應建立檢測大數據分析中心,深度挖掘尺寸偏差與工藝參數的關聯模型,最終實現質量問題的根源性預防,為智能制造2025戰略目標提供關鍵技術支撐。

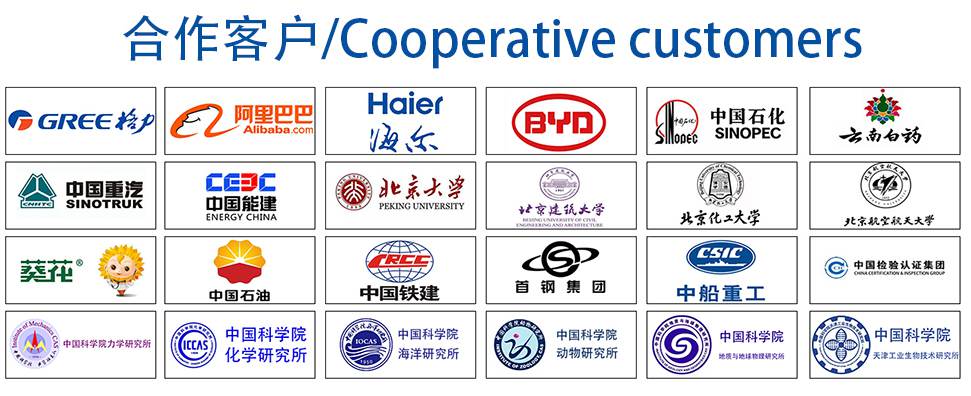