均勻性試驗(yàn)檢測(cè)
實(shí)驗(yàn)室擁有眾多大型儀器及各類分析檢測(cè)設(shè)備,研究所長(zhǎng)期與各大企業(yè)、高校和科研院所保持合作伙伴關(guān)系,始終以科學(xué)研究為首任,以客戶為中心,不斷提高自身綜合檢測(cè)能力和水平,致力于成為全國(guó)科學(xué)材料研發(fā)領(lǐng)域服務(wù)平臺(tái)。
立即咨詢聯(lián)系中化所
均勻性試驗(yàn)檢測(cè)技術(shù)白皮書
在智能制造與精準(zhǔn)質(zhì)量控制雙輪驅(qū)動(dòng)下,均勻性試驗(yàn)檢測(cè)已成為現(xiàn)代工業(yè)體系的核心質(zhì)量保障環(huán)節(jié)。據(jù)中國(guó)材料測(cè)試研究院2024年數(shù)據(jù)顯示,新材料領(lǐng)域因組分不均勻?qū)е碌呐钨|(zhì)量問題占比達(dá)23.7%,直接造成年經(jīng)濟(jì)損失超120億元。作為"多批次穩(wěn)定性驗(yàn)證"的關(guān)鍵技術(shù)手段,該項(xiàng)目通過構(gòu)建材料/制品的組分分布量化模型,有效解決了傳統(tǒng)抽檢模式存在的"以點(diǎn)代面"風(fēng)險(xiǎn)。其核心價(jià)值體現(xiàn)在三個(gè)維度:生產(chǎn)工藝閉環(huán)優(yōu)化提供數(shù)據(jù)支撐、產(chǎn)品可靠性驗(yàn)證建立科學(xué)依據(jù)、質(zhì)量事故溯源形成完整證據(jù)鏈,在動(dòng)力電池極片涂布、藥物緩釋制劑等20余個(gè)重點(diǎn)領(lǐng)域展現(xiàn)出不可替代的工程價(jià)值。
基于空間采樣矩陣的技術(shù)原理
該檢測(cè)體系以空間統(tǒng)計(jì)學(xué)為基礎(chǔ),采用分區(qū)層級(jí)采樣設(shè)計(jì)。針對(duì)不同形態(tài)樣本(粉體/液體/固態(tài)),分別建立三維網(wǎng)格化采樣模型,配合X射線熒光光譜(XRF)或近紅外光譜(NIRS)進(jìn)行原位檢測(cè)。通過變異系數(shù)(CV值)計(jì)算與蒙特卡洛模擬,精確評(píng)估樣本的全局均勻度。以鋰電正極材料檢測(cè)為例,按照GB/T 3723-2022標(biāo)準(zhǔn),在混料設(shè)備出口處布置9點(diǎn)環(huán)形采樣陣列,可實(shí)現(xiàn)粒徑分布與元素含量的同步分析,檢測(cè)靈敏度達(dá)到0.3%組分偏差。
全流程自動(dòng)化檢測(cè)實(shí)施方案
典型項(xiàng)目實(shí)施包含六個(gè)關(guān)鍵節(jié)點(diǎn):工藝參數(shù)采集→檢測(cè)方案定制→智能采樣執(zhí)行→數(shù)據(jù)云端處理→三維熱力圖生成→質(zhì)量決策輸出。某跨國(guó)藥企在其凍干粉針劑生產(chǎn)線部署的在線檢測(cè)系統(tǒng),通過集成機(jī)器視覺與拉曼光譜技術(shù),將原本需要8小時(shí)的均勻性檢測(cè)縮短至45分鐘。系統(tǒng)配備的"工藝參數(shù)優(yōu)化指導(dǎo)"模塊,能自動(dòng)關(guān)聯(lián)混合轉(zhuǎn)速、時(shí)間等12項(xiàng)關(guān)鍵參數(shù)與檢測(cè)結(jié)果,推動(dòng)產(chǎn)品合格率從89.6%提升至98.2%。
跨行業(yè)典型應(yīng)用場(chǎng)景解析
在新能源領(lǐng)域,某TOP5電池企業(yè)通過極片涂布均勻性檢測(cè),將面密度波動(dòng)控制在±1.5%以內(nèi),使電芯容量一致性提升40%。食品工業(yè)中,某乳制品龍頭企業(yè)運(yùn)用近紅外在線檢測(cè)系統(tǒng),實(shí)現(xiàn)奶粉營(yíng)養(yǎng)成分的實(shí)時(shí)監(jiān)控,蛋白質(zhì)分布CV值從2.8%降至1.2%。更值得關(guān)注的是在核燃料元件制造中的特殊應(yīng)用,通過中子衍射均勻性檢測(cè)技術(shù),成功將鈾-235分布偏差控制在0.05%級(jí),為反應(yīng)堆安全運(yùn)行提供保障。
四維質(zhì)量保障體系建設(shè)
項(xiàng)目構(gòu)建包含方法驗(yàn)證、設(shè)備計(jì)量、人員認(rèn)證、數(shù)據(jù)溯源的立體化質(zhì)控體系。按照ISO 13528:2023標(biāo)準(zhǔn),每年開展實(shí)驗(yàn)室間比對(duì)驗(yàn)證,確保不同檢測(cè)站點(diǎn)間En值≤0.7。關(guān)鍵檢測(cè)設(shè)備實(shí)行三級(jí)計(jì)量管理,配備區(qū)塊鏈溯源系統(tǒng),確保溫度、濕度等12項(xiàng)環(huán)境參數(shù)的全程可信記錄。人員資質(zhì)方面,要求檢測(cè)工程師必須通過 認(rèn)證的"微觀結(jié)構(gòu)分析工程師"考核,并每季度參與能力驗(yàn)證項(xiàng)目。
展望未來發(fā)展,建議從三方面深化技術(shù)應(yīng)用:一是建立細(xì)分行業(yè)的均勻性數(shù)據(jù)庫(kù),利用機(jī)器學(xué)習(xí)構(gòu)建工藝-質(zhì)量預(yù)測(cè)模型;二是推動(dòng)檢測(cè)設(shè)備微型化發(fā)展,拓展至分布式制造場(chǎng)景;三是加強(qiáng)ASTM與ISO標(biāo)準(zhǔn)協(xié)同,建立跨國(guó)界檢測(cè)結(jié)果互認(rèn)機(jī)制。只有持續(xù)完善"質(zhì)量數(shù)字孿生"體系,才能充分發(fā)揮均勻性檢測(cè)在工業(yè)4.0時(shí)代的核心樞紐作用。

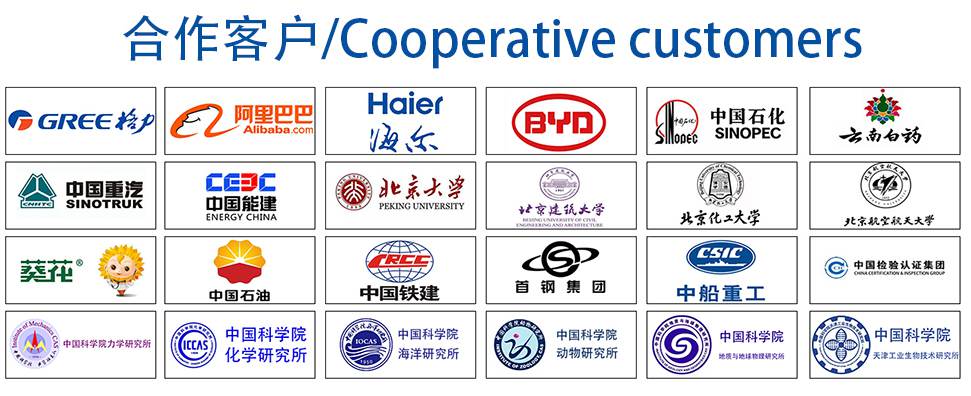