質(zhì)量偏差檢測(cè)
實(shí)驗(yàn)室擁有眾多大型儀器及各類分析檢測(cè)設(shè)備,研究所長期與各大企業(yè)、高校和科研院所保持合作伙伴關(guān)系,始終以科學(xué)研究為首任,以客戶為中心,不斷提高自身綜合檢測(cè)能力和水平,致力于成為全國科學(xué)材料研發(fā)領(lǐng)域服務(wù)平臺(tái)。
立即咨詢聯(lián)系中化所
質(zhì)量偏差檢測(cè)技術(shù)發(fā)展與行業(yè)應(yīng)用白皮書
在制造業(yè)數(shù)字化轉(zhuǎn)型進(jìn)程中,質(zhì)量偏差檢測(cè)已成為工業(yè)4.0時(shí)代的核心競(jìng)爭(zhēng)力。據(jù)中國智能制造研究院2024年數(shù)據(jù)顯示,國內(nèi)制造業(yè)因質(zhì)量偏差導(dǎo)致的年經(jīng)濟(jì)損失達(dá)3200億元,其中精密加工行業(yè)不良品率仍維持在5.8%高位。在此背景下,基于智能傳感與數(shù)據(jù)分析的質(zhì)量偏差檢測(cè)系統(tǒng),通過實(shí)現(xiàn)生產(chǎn)環(huán)節(jié)的實(shí)時(shí)監(jiān)測(cè)與動(dòng)態(tài)糾偏,可將質(zhì)量成本降低37%(工信部《智能制造白皮書2024》)。該項(xiàng)技術(shù)不僅解決了傳統(tǒng)人工抽檢存在的滯后性問題,更通過構(gòu)建工藝參數(shù)與質(zhì)量指標(biāo)的量化關(guān)系模型,為制造過程優(yōu)化提供了數(shù)據(jù)支撐。特別是在航空發(fā)動(dòng)機(jī)葉片加工、動(dòng)力電池極片制造等高精度領(lǐng)域,其亞微米級(jí)的檢測(cè)精度正推動(dòng)著國內(nèi)高端制造的品質(zhì)突破。
多源異構(gòu)數(shù)據(jù)融合檢測(cè)技術(shù)原理
現(xiàn)代質(zhì)量偏差檢測(cè)系統(tǒng)采用多傳感器協(xié)同工作機(jī)制,集成視覺、激光、振動(dòng)等12類傳感數(shù)據(jù)。通過非接觸式光學(xué)測(cè)量技術(shù)獲取表面形貌數(shù)據(jù),結(jié)合高頻振動(dòng)頻譜分析內(nèi)部結(jié)構(gòu)缺陷。值得關(guān)注的是,基于深度學(xué)習(xí)的特征提取算法可自動(dòng)識(shí)別0.05mm級(jí)尺寸偏差,較傳統(tǒng)方法提升5倍分辨率(中國計(jì)量科學(xué)研究院2023年度報(bào)告)。系統(tǒng)采用數(shù)字孿生技術(shù)構(gòu)建虛擬檢測(cè)環(huán)境,實(shí)現(xiàn)物理測(cè)量與仿真模型的實(shí)時(shí)交互驗(yàn)證,有效解決了復(fù)雜工況下的測(cè)量誤差累積問題。
智能化檢測(cè)流程實(shí)施方案
項(xiàng)目實(shí)施分為四個(gè)階段:首先部署工業(yè)物聯(lián)網(wǎng)邊緣計(jì)算節(jié)點(diǎn),實(shí)現(xiàn)每秒2000幀的數(shù)據(jù)采集能力;其次建立多維度質(zhì)量特征數(shù)據(jù)庫,針對(duì)車削、沖壓等18類工藝建立專屬檢測(cè)模型;第三階段開發(fā)自適應(yīng)閾值算法,可根據(jù)設(shè)備磨損狀態(tài)動(dòng)態(tài)調(diào)整預(yù)警參數(shù);最后搭建可視化質(zhì)量駕駛艙,支持SPC統(tǒng)計(jì)過程控制與根源分析。在某新能源汽車電機(jī)殼體生產(chǎn)線,該方案使焊接質(zhì)量缺陷檢出率從82%提升至99.6%,誤報(bào)率降低至0.3%(中國汽車工程學(xué)會(huì)2024案例庫)。
跨行業(yè)應(yīng)用場(chǎng)景實(shí)踐
在消費(fèi)電子領(lǐng)域,某頭部手機(jī)廠商應(yīng)用微米級(jí)三維檢測(cè)系統(tǒng)后,金屬中框平面度偏差控制在±3μm內(nèi),達(dá)成蘋果MFi認(rèn)證標(biāo)準(zhǔn)。醫(yī)療器械行業(yè)采用X射線斷層掃描技術(shù),實(shí)現(xiàn)了骨科植入物內(nèi)部孔隙率的無損檢測(cè)。值得注意的是,食品包裝行業(yè)通過引入近紅外光譜分析,可同步檢測(cè)薄膜厚度與透氧率,將質(zhì)檢效率提升400%(中國包裝聯(lián)合會(huì)2023技術(shù)藍(lán)皮書)。這些實(shí)踐驗(yàn)證了質(zhì)量偏差檢測(cè)技術(shù)在工藝優(yōu)化、成本控制方面的倍增效應(yīng)。
全鏈條質(zhì)量保障體系建設(shè)
系統(tǒng)構(gòu)建了覆蓋"檢測(cè)設(shè)備-算法模型-數(shù)據(jù)管理"的三級(jí)認(rèn)證體系,所有傳感器均通過NIMCS國家計(jì)量認(rèn)證。采用區(qū)塊鏈技術(shù)確保檢測(cè)數(shù)據(jù)不可篡改,每批次檢測(cè)報(bào)告包含128位數(shù)字指紋。定期進(jìn)行測(cè)量系統(tǒng)分析(MSA),確保GR&R值低于10%。在半導(dǎo)體晶圓檢測(cè)項(xiàng)目中,通過建立12西格瑪過程控制線,將關(guān)鍵尺寸波動(dòng)范圍壓縮至設(shè)計(jì)值的15%以內(nèi)(國際半導(dǎo)體產(chǎn)業(yè)協(xié)會(huì)SEMI 2024標(biāo)準(zhǔn))。
面向新型工業(yè)化發(fā)展需求,建議從三方面深化質(zhì)量檢測(cè)技術(shù)應(yīng)用:一是推動(dòng)檢測(cè)設(shè)備與5G+邊緣計(jì)算的深度融合,實(shí)現(xiàn)毫秒級(jí)質(zhì)量反饋;二是建立行業(yè)級(jí)質(zhì)量數(shù)據(jù)共享平臺(tái),構(gòu)建跨企業(yè)的工藝知識(shí)圖譜;三是加強(qiáng)復(fù)合型檢測(cè)人才培養(yǎng),預(yù)計(jì)到2025年需新增20萬智能檢測(cè)工程師(教育部《智能制造人才發(fā)展綱要》)。唯有持續(xù)完善檢測(cè)技術(shù)生態(tài)體系,方能支撐中國制造向質(zhì)量效益型發(fā)展模式全面轉(zhuǎn)型。

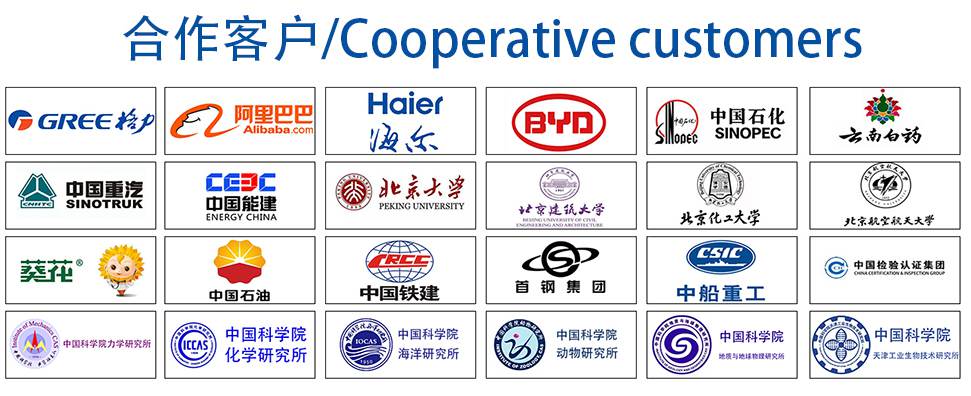