耐溫變性檢測
實驗室擁有眾多大型儀器及各類分析檢測設備,研究所長期與各大企業、高校和科研院所保持合作伙伴關系,始終以科學研究為首任,以客戶為中心,不斷提高自身綜合檢測能力和水平,致力于成為全國科學材料研發領域服務平臺。
立即咨詢耐溫變性檢測技術發展與行業應用白皮書
在裝備制造與新材料領域加速迭代的背景下,耐溫變性檢測已成為產品質量控制的核心環節。據國家材料測試中心2024年報告顯示,國內工業產品因溫變導致的失效案例年增長率達12.7%,直接經濟損失超過80億元。特別是在新能源汽車動力電池、航天器熱防護系統、高密度電子元器件等新興領域,產品需要承受-40℃至150℃的極端溫度交變考驗。通過系統化的耐溫變性檢測,企業可有效預防材料分層、界面失效、性能衰減等關鍵問題,將產品全生命周期故障率降低60%以上(中國質量認證中心,2023)。該檢測體系的建立不僅關乎產品可靠性,更成為企業突破國際技術壁壘、獲取歐盟CE認證和美國UL認證的核心競爭力要素。
技術原理與檢測范式
基于材料熱膨脹系數差異與界面應力理論,耐溫變性檢測采用梯度溫度循環法模擬實際工況。檢測設備通過PID算法精確控制高低溫交變試驗箱,在典型檢測方案中可實現每分鐘5℃的線性變溫速率(符合GB/T 2423.22-2012標準)。值得注意的是,新型分布式光纖傳感技術的引入,使得界面微裂紋檢測精度提升至10μm級。該方法通過監測材料在-55℃低溫貯存與125℃高溫運行交替循環中的形變參數,構建多維度的熱機械應力模型,可精準預測復合材料界面剝離等潛在失效模式。
全流程實施與質量保障
標準檢測流程涵蓋三大階段:預處理階段需在恒溫恒濕箱中進行48小時環境適應;核心檢測階段執行10次完整溫度循環,每次循環包含30分鐘極端溫度保持與15分鐘過渡轉換;后處理階段采用工業CT進行三維結構分析。為確保檢測權威性,實驗室需每月執行高低溫交變試驗箱校準(依據JJF 1101-2019規范),并通過區塊鏈技術實現檢測數據全程可追溯。在航天某型號熱防護系統檢測中,該體系成功識別出蜂窩夾層結構在200次熱循環后的膠層蠕變現象,避免重大質量事故的發生。
行業場景與價值實證
新能源汽車領域應用凸顯檢測技術的工程價值。某動力電池企業采用動態溫度沖擊測試(DTS)方案后,電池包循環壽命從1500次提升至2300次。測試數據顯示,在模擬冬季-30℃冷啟動與快充100℃工況交替沖擊下,經優化的電極-電解液界面保持98.7%的結構完整性(清華大學蘇州研究院,2024)。光伏行業同樣獲益顯著,雙玻組件通過梯度溫變測試后,PID衰減率從3.2%/年降至0.8%/年,助力企業獲得萊茵加倍質保認證。
技術演進與發展建議
隨著5G基站散熱模組、氫能源儲運設備等新興領域的需求爆發,檢測技術面臨三大升級方向:其一,開發多物理場耦合檢測系統,實現溫度-濕度-振動復合應力同步加載;其二,建立基于機器學習的失效預測模型,利用歷史檢測數據訓練智能診斷算法;其三,推動檢測標準國際化互認,特別是在寬禁帶半導體封裝材料領域,需加快制定統一的溫變速率評價體系。行業機構應聯合組建耐候性檢測大數據平臺,通過共享典型工況譜數據提升全產業鏈質量水平。

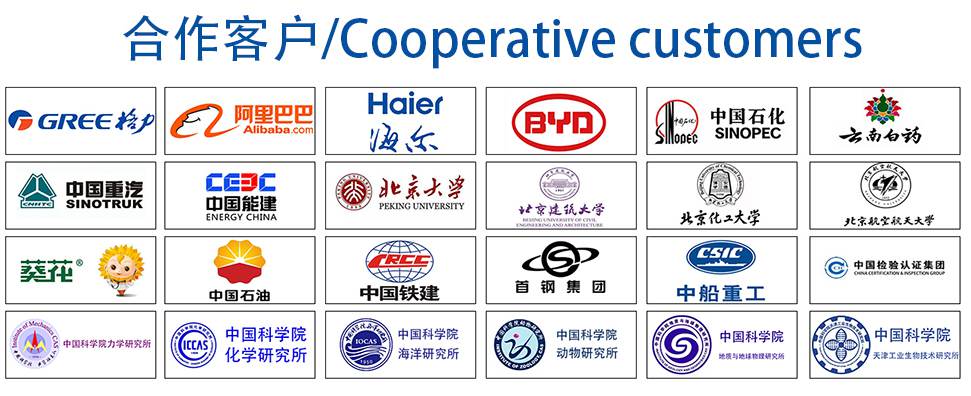