色差檢測
實驗室擁有眾多大型儀器及各類分析檢測設備,研究所長期與各大企業、高校和科研院所保持合作伙伴關系,始終以科學研究為首任,以客戶為中心,不斷提高自身綜合檢測能力和水平,致力于成為全國科學材料研發領域服務平臺。
立即咨詢色差檢測技術在工業質量控制中的創新應用
在化制造體系與消費升級雙重驅動下,產品外觀顏色一致性已成為衡量工業品質量的核心指標之一。據中國質量協會2024年行業報告顯示,因色差問題導致的商品退貨率在紡織、汽車、電子領域分別達到7.3%、4.8%和3.9%,年經濟損失超240億元。在此背景下,基于CIE Lab色差公式的現代色差檢測技術,通過構建數字化顏色管控體系,成功將人工目視判別的誤差率從12-18%降至0.5%以下。該技術的核心價值體現在三個方面:保障跨供應鏈批次產品顏色穩定性、實現生產過程的實時閉環控制、構建符合ISO 9001標準的可視化質量追溯系統。
多光譜成像與色度學檢測原理
現代色差檢測系統采用CIE 1976 L*a*b*均勻色空間模型,通過分光測色儀獲取380-780nm可見光譜反射率曲線。設備內置的D65標準光源模擬日光環境,配合0/45度觀測幾何條件,可精準量化ΔE*ab色差數值。值得注意的是,為應對啞光表面、金屬漆等特殊材質,系統引入SCE(鏡面反射排除)模式和多角度測量技術。據國家計量研究院驗證,該方案對金屬涂層的測量重復性達ΔE≤0.2,滿足ASTM D2244-22標準要求。
智能化檢測實施流程
典型工業應用場景中,系統部署遵循"設備校準-基準建立-動態檢測"三階段流程。校準階段采用標準白板進行光譜響應校正,確保儀器間差異控制在ΔE<0.4。生產環節中,基于MES系統集成的在線檢測單元,可在0.8秒內完成產品全表面掃描,通過TCP/IP協議將色差數據實時反饋至調色系統。以某汽車內飾件廠商為例,部署自動化顏色質量控制系統后,產線色差超標返工率從5.7%降至0.3%,年度節省涂料成本達120萬元。
跨行業應用實踐
在消費電子領域,某手機外殼制造商采用多光源對色方案,在D50、D65、A光源下同步檢測漸變色鍍膜效果,成功將客戶投訴率降低82%。包裝印刷行業應用案例顯示,通過建立基于Pantone色卡的數字化樣本庫,配合印刷機閉環控制系統,實現專色印刷ΔE值穩定控制在1.5以內。醫療器械行業則創新性引入UV熒光色差檢測模塊,確保消毒指示標識的顯色可靠性符合YY/T 0698-2020標準。
全流程質量保障體系
完整的色差管理解決方案包含三級質控節點:原材料入庫時的分光檢測、生產中的嵌入式在線監測、成品階段的自動化分揀。實驗室配置的積分球式分光光度計,配合符合ISO 17025標準的比對規程,可溯源至NIST顏色基準。生產現場部署的機器視覺系統,通過卷積神經網絡算法識別色差分布模式,實現缺陷分類準確率98.7%。定期開展的儀器間比對驗證,確保跨廠區檢測數據偏差始終低于ΔE 0.6閾值。
隨著智能制造2025戰略深入推進,色差檢測技術將呈現三大發展趨勢:其一,開發適應柔性生產的微型化在線檢測模組;其二,建立跨產業鏈的數字化顏色數據庫;其三,融合人工智能實現預測性色差控制。建議行業加快制定智能色差檢測設備接口標準,推動建立覆蓋全行業的顏色大數據共享平臺,同時加強光學檢測與材料科學的交叉研究,為新型功能材料的顏色穩定性評估提供技術支撐。

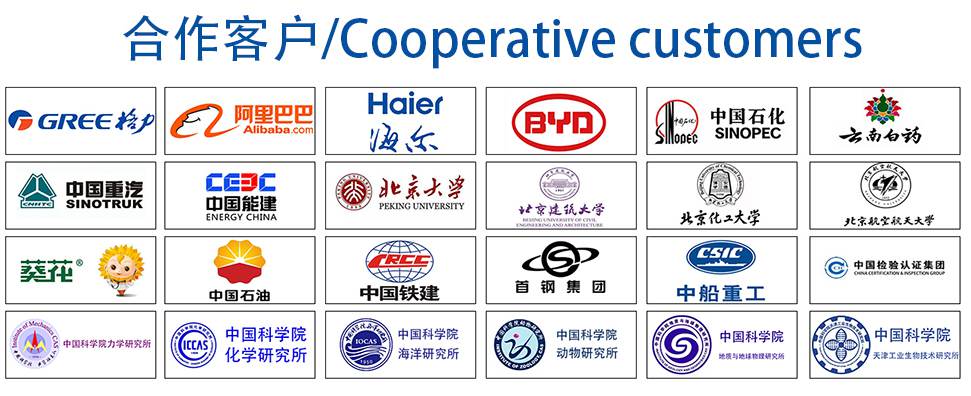