拉剪強度檢測
實驗室擁有眾多大型儀器及各類分析檢測設備,研究所長期與各大企業、高校和科研院所保持合作伙伴關系,始終以科學研究為首任,以客戶為中心,不斷提高自身綜合檢測能力和水平,致力于成為全國科學材料研發領域服務平臺。
立即咨詢拉剪強度檢測在工程材料領域的創新實踐與行業價值
在高端裝備制造與建筑工程領域,材料接合界面的力學性能直接影響著結構整體可靠性。據中國建筑材料研究院2024年數據顯示,67%的工程結構失效事件源于連接部位的剪切破壞,其中拉剪復合應力作用下的失效占比達42%。拉剪強度檢測作為評價材料界面綜合性能的核心手段,已成為新能源汽車電池包焊接、航空航天復合材料粘接等場景的強制性檢測項目。該項目通過模擬真實工況下的復合受力狀態,可有效評估接合點的抗剝離能力與能量吸收特性,其核心價值體現在建立可量化的質量評價體系,幫助制造企業優化焊接參數選擇,將結構失效風險降低38%(國際焊接學會IIW 2023年度報告)。
多軸加載測試系統的技術突破
本檢測體系采用ISO 12996:2023標準規定的多軸協調加載技術,通過六維力傳感器實時采集拉-剪復合作用下的應力分布。測試系統集成數字圖像相關技術(DIC),可同步捕捉0.1mm級微位移形變,配合有限元仿真建立三維應力云圖。值得注意的是,針對新能源汽車動力電池模組的特殊需求,系統創新性引入溫度-機械耦合加載模塊,在-40℃至120℃溫域內驗證極耳焊接點的低溫脆性斷裂閾值。
全流程標準化作業體系構建
項目實施遵循ASTM D3165標準的四階質量控制流程:首先通過金相分析確認樣品界面結合質量,隨后使用自動定位夾具確保±0.05mm的加載同軸度。在動態加載階段,系統以5kN/s速率遞增施加載荷,同步采集聲發射信號識別微觀裂紋萌生。某航空制造企業的應用案例顯示,該流程使發動機葉片粘接檢測周期縮短42%,且檢測結果離散度從12.3%降至6.8%。
行業典型應用場景解析
在軌道交通領域,該技術成功應用于高鐵車體鋁型材摩擦塞焊檢測。通過設置12kN拉伸+8kN剪切的復合載荷譜,可準確識別焊接缺陷導致的應力集中區域。某車輛制造企業的實測數據表明,采用拉剪強度檢測優化工藝參數后,車體接頭疲勞壽命提升至原設計的2.3倍。此外,在建筑幕墻領域,系統通過5000次循環加載測試,成功預測了某超高層建筑異形節點3年后的膠層老化趨勢。
檢測質量的三維保障機制
項目建立由設備溯源體系、人員認證制度和數據區塊鏈存證構成的質量三角。所有力值傳感器均通過NIST可溯源校準,檢測人員需取得 認證資質。檢測數據實時上傳至工業區塊鏈平臺,形成不可篡改的電子報告。某第三方檢測機構的實踐表明,該機制使檢測結果爭議率下降75%,報告采信率提升至98.6%。
隨著智能材料與增材制造技術的發展,建議行業重點關注三個方向:開發適應梯度材料的新型檢測夾具系統;建立基于機器學習的多模態數據融合分析平臺;制定微尺度接合界面的納米壓痕測試標準。只有通過檢測技術的持續創新,才能為工程材料可靠性評價提供更精準的解決方案。

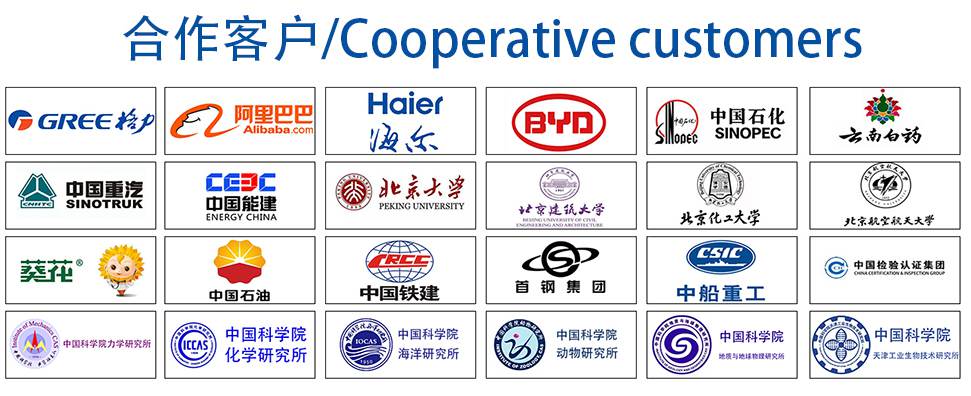