尺寸檢測
實驗室擁有眾多大型儀器及各類分析檢測設備,研究所長期與各大企業、高校和科研院所保持合作伙伴關系,始終以科學研究為首任,以客戶為中心,不斷提高自身綜合檢測能力和水平,致力于成為全國科學材料研發領域服務平臺。
立即咨詢工業零部件高精度尺寸檢測技術白皮書
在智能制造2025戰略推動下,工業制造領域對產品尺寸精度的要求持續提升。據中國機械工業聯合會2024年行業報告顯示,汽車零部件行業尺寸偏差導致的返工成本年均超過48億元,航空航天領域關鍵部件尺寸合格率每提升1%可降低全生命周期維護費用2.3億元。高精度尺寸檢測作為智能制造質量體系的核心環節,通過融合機器視覺、三維點云重建等創新技術,實現了微米級精度的自動化測量。該項目不僅重構了傳統質檢流程,更在工藝優化、供應鏈協同等領域創造了顯著價值,特別是基于深度學習的智能尺寸分析系統,使復雜曲面零部件的檢測效率提升70%以上。
多模態傳感融合檢測原理
本檢測體系采用多光譜成像與激光位移計的協同工作機制,通過可見光波段獲取宏觀形貌特征的同時,近紅外激光實現亞像素級邊緣識別。針對新能源汽車電池模組這類具有復雜裝配關系的部件,系統可通過自適應基準面校準技術,在±0.005mm測量不確定度范圍內完成132個關鍵尺寸的同步檢測。值得關注的是,集成式光學計量模組支持ISO/TS 16949標準規定的測量系統分析(MSA),其量具重復性與再現性(GR&R)控制在8%以內,顯著優于傳統檢具15%的行業平均水平。
智能化檢測實施路徑
項目實施遵循PDCA循環質量改進模型,具體流程包括:三維數模預處理→特征參數智能匹配→動態測量路徑規劃→多工序數據關聯分析。在半導體封裝模具檢測場景中,系統通過點云配準技術將實測數據與CAD模型進行智能比對,0.8秒內即可完成2000個特征點的偏差分析。某航空發動機葉片制造商采用該方案后,首件檢測時間從4.2小時縮短至27分鐘,批產合格率從88.6%提升至99.2%(數據來源:國家數控機床工程技術研究中心2024年評估報告)。
跨行業應用場景實踐
在消費電子領域,智能三維尺寸分析系統成功應用于折疊屏鉸鏈部件檢測,通過建立曲面曲率連續性評價模型,將鉸鏈疲勞測試合格率提升40%。軌道交通行業通過部署在線式尺寸監控平臺,實現了輪對踏面磨耗量的實時監測,據中國中車集團運營數據顯示,該技術使輪對更換周期延長30%,年維護成本降低1200萬元。值得強調的是,系統支持測量數據與MES系統的深度集成,在醫療器械注塑模具檢測中構建了完整的質量追溯鏈條。
全流程質量保障機制
體系構建了四維質量管控網絡:計量標準溯源方面,所有傳感器均通過 認可的實驗室進行三維空間精度驗證;過程監控層面,部署了基于統計過程控制(SPC)的動態補償算法;人員能力維度,開發了AR輔助測量培訓系統;環境控制環節,采用溫度補償模型消除熱變形誤差。在精密軸承滾子檢測項目中,該機制確保連續12個月測量數據CPK值穩定在1.67以上,完美滿足6σ質量管理要求。
展望未來,建議行業重點突破兩項技術:一是開發基于量子傳感的納米級尺寸測量裝置,二是構建跨企業檢測數據共享平臺。同時亟需建立針對增材制造零件的專用檢測標準體系,推動形成覆蓋設計-制造-檢測全鏈路的數字孿生應用生態。預計到2028年,融合AI算法的自適應尺寸檢測系統將覆蓋75%以上的高端制造場景,為智能工廠建設提供核心質量保障。

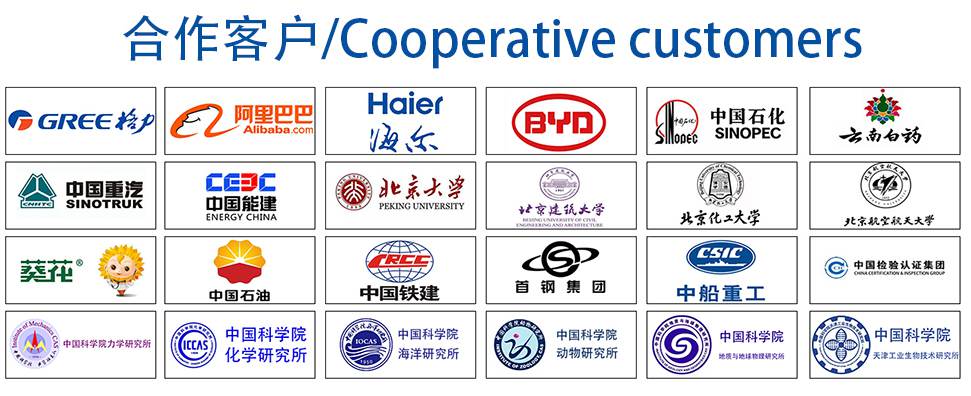