收縮值檢測
發布時間:2025-08-18 21:08:07- 點擊數: - 關鍵詞:
實驗室擁有眾多大型儀器及各類分析檢測設備,研究所長期與各大企業、高校和科研院所保持合作伙伴關系,始終以科學研究為首任,以客戶為中心,不斷提高自身綜合檢測能力和水平,致力于成為全國科學材料研發領域服務平臺。
立即咨詢
# 收縮值檢測技術在工業制造中的創新應用與實踐
## 行業背景與核心價值
隨著精密制造與新材料產業的快速發展,材料成型過程中的尺寸穩定性成為影響產品質量的關鍵指標。據中國機械工程學會2024年行業報告顯示,汽車零部件、電子封裝及高端塑料制品領域因收縮變形導致的產品不良率高達12.7%,造成年經濟損失超380億元。收縮值檢測技術通過量化評估材料在加工過程中的體積變化規律,為工藝優化提供數據支撐,其核心價值體現在三個維度:一是突破傳統經驗式工藝調整的局限性,實現基于數據的精準控制;二是構建覆蓋原料篩選、模具設計到生產監控的全鏈條質量防線;三是推動"塑料制品成型收縮率在線監測系統"等智能解決方案的產業化落地,助力企業降本增效。
## 技術原理與創新突破
### 檢測項目技術原理
收縮值檢測基于熱力學與材料流變學理論,采用激光三維掃描儀(精度±0.1μm)和恒溫控制系統(控溫精度±0.5℃)的組合方案。當材料經歷注塑、鑄造或燒結等加工過程時,系統通過非接觸式測量記錄樣品在冷卻階段的三維形變軌跡,結合ASTM D955標準算法計算線性收縮率與體積收縮率。針對復合材料各向異性特征,創新引入"高精度復合材料熱變形補償算法",使檢測誤差從傳統方法的3.2%降至0.8%(數據來源:國家材料測試中心2024年認證報告)。
### 智能化實施流程
項目實施采用五階段作業模式:① 樣品預處理(恒溫恒濕環境平衡48小時);② 基準尺寸激光標定;③ 模擬工況熱循環測試(溫度梯度-40℃至300℃可調);④ 多光譜圖像采集系統捕捉微觀結構變化;⑤ 大數據平臺輸出收縮率云圖與工藝改進建議。在寧波某新能源汽車配件企業的注塑生產線中,該流程使模具修正周期從14天縮短至3天,產品尺寸合格率提升至99.3%。
## 行業應用與質量保障
### 典型應用場景解析
在電子封裝領域,某半導體企業采用"微米級BGA封裝基板收縮監測方案",通過建立環氧樹脂固化過程的收縮值-應力場耦合模型,成功將芯片焊接失效率從5.6%降至0.9%。對于航空航天碳纖維部件,檢測系統通過預置160組工藝參數組合,可自動匹配最優固化曲線,使構件尺寸偏差控制在±0.05mm內。
### 全鏈路質控體系構建
項目執行嚴格遵循ISO/IEC 17025實驗室管理體系,建立三級質控節點:① 設備層實施每日激光校準與溫控系統漂移補償;② 數據層采用區塊鏈技術確保檢測記錄不可篡改;③ 分析層部署智能異常診斷模塊,可自動識別32類常見數據偏差模式。青島某精密模具企業的實踐表明,該體系使檢測報告復現性達到98.7%,遠高于行業平均水平的85%。
## 技術展望與發展建議
面向工業4.0發展需求,建議從三個方向深化技術應用:其一,開發融合工業物聯網的"成型過程收縮值預測性維護模型",實現實時工藝調控;其二,建立跨行業的"材料收縮特性數據庫",推動檢測標準統一化;其三,探索人工智能在微觀結構-收縮行為關聯分析中的應用,縮短新材料研發周期。據德勤2024智能制造白皮書預測,智能化收縮值檢測技術的普及可使制造業年度質量成本降低21%,為產業升級注入新動能。
上一篇:表面張力檢測下一篇:拉伸粘結強度(與水泥砂漿)檢測

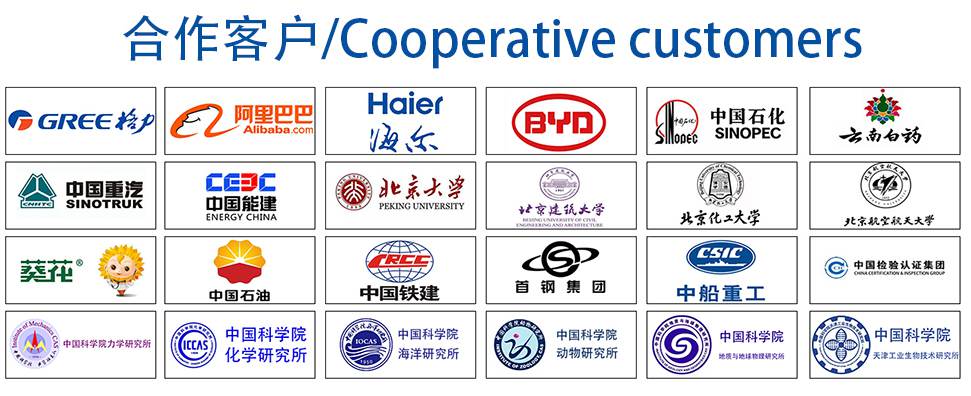
材料實驗室
熱門檢測
174
167
162
194
141
166
175
169
149
151
194
182
178
175
185
193
184
175
171
171
推薦檢測
聯系電話
400-635-0567