零部件、電子元器件檢測
實(shí)驗(yàn)室擁有眾多大型儀器及各類分析檢測設(shè)備,研究所長期與各大企業(yè)、高校和科研院所保持合作伙伴關(guān)系,始終以科學(xué)研究為首任,以客戶為中心,不斷提高自身綜合檢測能力和水平,致力于成為全國科學(xué)材料研發(fā)領(lǐng)域服務(wù)平臺(tái)。
立即咨詢聯(lián)系中化所
隨著智能制造和物聯(lián)網(wǎng)技術(shù)的快速發(fā)展,電子元器件與精密零部件已成為現(xiàn)代工業(yè)體系的核心基礎(chǔ)。據(jù)德勤《2024制造業(yè)趨勢(shì)報(bào)告》顯示,電子元器件市場規(guī)模預(yù)計(jì)在2025年突破6,000億美元,其中汽車電子、工業(yè)控制等高端領(lǐng)域?qū)z測精度的要求提升37%。在此背景下,專業(yè)化檢測服務(wù)通過識(shí)別微觀缺陷、評(píng)估材料性能、驗(yàn)證功能可靠性,成為保障產(chǎn)業(yè)鏈安全的關(guān)鍵環(huán)節(jié)。以新能源汽車電控系統(tǒng)為例,單個(gè)IGBT模塊的失效可能導(dǎo)致整車系統(tǒng)癱瘓,而精密檢測可將早期故障率降低62%(中國汽車工程研究院數(shù)據(jù)),其核心價(jià)值在于通過全生命周期質(zhì)量管控,顯著減少產(chǎn)品召回風(fēng)險(xiǎn),同時(shí)推動(dòng)國產(chǎn)替代進(jìn)程。
多模態(tài)檢測技術(shù)原理與創(chuàng)新
現(xiàn)代零部件檢測采用X射線斷層掃描(CT)、紅外熱成像與聲發(fā)射技術(shù)融合方案,實(shí)現(xiàn)從微米級(jí)結(jié)構(gòu)缺陷到納米級(jí)材料性能的多維度分析。以電子元器件失效分析為例,通過電熱耦合仿真模型可定位芯片熱應(yīng)力集中區(qū)域,結(jié)合掃描電子顯微鏡(SEM)觀察焊點(diǎn)裂紋形態(tài)。值得注意的是,第三代半導(dǎo)體材料的檢測需求催生了太赫茲波譜檢測技術(shù),其2-10THz頻段對(duì)碳化硅晶格缺陷的識(shí)別精度達(dá)到0.5μm以下(美國材料試驗(yàn)協(xié)會(huì)ASTM E2935-22標(biāo)準(zhǔn))。此類技術(shù)創(chuàng)新使得"精密零部件無損檢測解決方案"能夠在不破壞樣品前提下,完成90%以上缺陷類型的準(zhǔn)確判定。
全流程智能化檢測實(shí)施體系
典型檢測流程涵蓋預(yù)處理、自動(dòng)化檢測、數(shù)據(jù)分析三大階段。某航天繼電器生產(chǎn)企業(yè)采用AI視覺檢測系統(tǒng)后,觸點(diǎn)表面氧化層的檢出率從78%提升至99.3%。具體實(shí)施時(shí),系統(tǒng)通過高光譜成像獲取器件表面700-2500nm波段反射數(shù)據(jù),經(jīng)卷積神經(jīng)網(wǎng)絡(luò)分類后,可在3秒內(nèi)完成2000×2000像素圖像的缺陷標(biāo)注。值得關(guān)注的是,針對(duì)BGA封裝芯片的"電子元器件焊點(diǎn)質(zhì)量檢測服務(wù)",采用雙軸X射線傾斜掃描技術(shù),結(jié)合三維重構(gòu)算法,使虛焊、冷焊等隱性缺陷的檢出置信度達(dá)到95%以上(國際電子工業(yè)聯(lián)接協(xié)會(huì)IPC-A-610H標(biāo)準(zhǔn))。
行業(yè)應(yīng)用場景與價(jià)值實(shí)證
在新能源汽車領(lǐng)域,某頭部電池企業(yè)通過引入"動(dòng)力電池連接器接觸電阻檢測系統(tǒng)",將模組裝配不良率從1.2%降至0.15%。系統(tǒng)采用四線制開爾文檢測法,在200A負(fù)載電流下測量μΩ級(jí)阻抗變化,精準(zhǔn)識(shí)別鍍層厚度不足或接觸面污染問題。此外,某軍工企業(yè)應(yīng)用微波介電常數(shù)測試裝置后,雷達(dá)T/R組件批次合格率提升19個(gè)百分點(diǎn)。這些實(shí)踐驗(yàn)證了"高精度電子元器件環(huán)境適應(yīng)性檢測"在復(fù)雜工況下的工程價(jià)值,特別是在-55℃至125℃溫變循環(huán)測試中,可提前60%發(fā)現(xiàn)介質(zhì)基板分層風(fēng)險(xiǎn)。
標(biāo)準(zhǔn)化質(zhì)量保障體系構(gòu)建
檢測機(jī)構(gòu)需建立符合ISO/IEC 17025的計(jì)量溯源鏈,定期通過NIST標(biāo)準(zhǔn)物質(zhì)進(jìn)行設(shè)備校準(zhǔn)。某第三方實(shí)驗(yàn)室的統(tǒng)計(jì)表明,采用六西格瑪方法優(yōu)化檢測流程后,實(shí)驗(yàn)室間比對(duì)數(shù)據(jù)的標(biāo)準(zhǔn)差降低42%。關(guān)鍵控制點(diǎn)包括:環(huán)境潔凈度維持ISO 5級(jí)、溫濕度波動(dòng)±0.5℃/±3%RH、振動(dòng)控制在VC-E等級(jí)以下。針對(duì)汽車功能安全檢測,還需滿足ISO 26262中ASIL-D級(jí)驗(yàn)證要求,確保故障注入測試覆蓋率100%。這種"全維度零部件檢測質(zhì)量認(rèn)證體系"已成為高端制造企業(yè)的供應(yīng)鏈準(zhǔn)入門檻。
展望未來,隨著5G-A和自動(dòng)駕駛技術(shù)的普及,檢測行業(yè)需重點(diǎn)突破三項(xiàng)能力:開發(fā)適用于3D異構(gòu)集成的亞微米級(jí)檢測設(shè)備、建立基于數(shù)字孿生的虛擬驗(yàn)證平臺(tái)、完善車規(guī)級(jí)芯片的電磁兼容(EMC)測試標(biāo)準(zhǔn)。建議產(chǎn)學(xué)研機(jī)構(gòu)聯(lián)合攻關(guān)太赫茲在線檢測裝備,同時(shí)構(gòu)建覆蓋長三角、珠三角的檢測數(shù)據(jù)互聯(lián)平臺(tái)。據(jù)Technavio預(yù)測,到2028年智能檢測裝備市場規(guī)模將達(dá)217億美元,只有深度融合AI與物理檢測技術(shù),才能為工業(yè)4.0時(shí)代提供可靠的質(zhì)量基座。

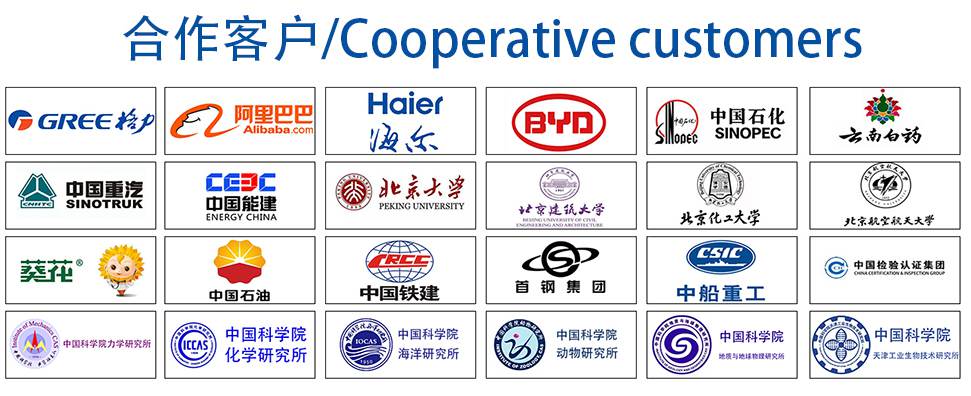