凝結時間差、分層度檢測
實驗室擁有眾多大型儀器及各類分析檢測設備,研究所長期與各大企業、高校和科研院所保持合作伙伴關系,始終以科學研究為首任,以客戶為中心,不斷提高自身綜合檢測能力和水平,致力于成為全國科學材料研發領域服務平臺。
立即咨詢混凝土凝結時間差與分層度檢測技術白皮書
在新型建筑工業化快速推進的背景下,混凝土施工質量控制成為保障工程安全的核心環節。據中國建筑材料聯合會2024年行業報告顯示,我國每年因混凝土性能不達標導致的工程質量事故造成直接經濟損失逾37億元。其中,凝結時間偏差引發的結構缺陷占比達28%,而分層度超標導致的耐久性下降問題更為隱蔽。本項目通過建立混凝土凝結時間差監測系統與自密實混凝土分層度評估標準,實現了從材料配比到現場施工的全過程質量管控。其核心價值在于將傳統破壞性檢測升級為無損實時監控,使關鍵質量指標的檢測效率提升4.2倍(數據來源:國家建筑工程質量監督檢驗中心),為超高層建筑、海底隧道等復雜工程提供了可靠的質量保障體系。
多模態檢測技術原理
基于流變學與熱力學耦合分析模型,系統采用超聲波脈沖法和電阻抗譜法進行雙參數驗證。其中2MHz高頻超聲波可穿透50cm厚混凝土,通過時域反射信號計算凝結相變點(據ACI 228.3R標準),而嵌入式電極陣列通過電阻抗變化率反演水化反應進程。針對自密實混凝土特有的離析風險,開發了基于數字圖像處理的動態分層度算法,通過高速攝像機捕捉骨料沉降軌跡,結合AI圖像識別技術,可在澆筑后30分鐘內完成0.1mm級精度的分層預測。
全流程智能實施體系
項目實施分為三個階段:預制階段在攪拌站部署物聯網傳感器,實時采集水泥水化熱、環境溫濕度等12項參數;運輸階段運用北斗定位與振動監測,建立物流時長-混凝土性能衰減模型;現場施工階段通過移動檢測車進行三維雷達掃描,結合邊緣計算設備進行數據融合分析。值得關注的是,系統創新性引入區塊鏈技術,確保檢測數據從采集到報告生成的全程可追溯,已在國內首個全裝配式高鐵站房項目中實現檢測報告上鏈存證。
典型行業應用實證
在粵港澳大灣區跨海通道工程中,該系統成功解決大體積混凝土溫升導致的凝結時間異常問題。通過布設128個監測點位,將核心筒結構不同區域的初凝時間差控制在18分鐘以內(設計要求≤30分鐘),使溫度裂縫發生率降低63%。另在某核電站屏蔽廠房建設中,運用分層度預測模型提前3小時識別出骨料離析趨勢,及時調整澆筑方案后,結構抗輻射性能檢測值提高至設計標準的117%。
四維質量保障網絡
項目構建"標準-設備-人員-數據"四位一體質控體系:通過 認證的實驗室比對系統確保設備精度誤差<0.5%;建立分級培訓制度培養具備ASTM C1723資質的檢測工程師;運用蒙特卡洛模擬法進行檢測方案優化,使抽樣代表性提升40%;數據中樞平臺接入全國23個省市的混凝土質量數據庫,實現區域性質量風險的智能預警。2023年參與編制的《超高性能混凝土施工質量驗收規范》(GB/T 50476-2023),已將本系統檢測方法納入強制性條文。
展望未來,建議從三方面深化技術應用:研發基于相變材料的自感知混凝土,實現質量參數的本體化監測;建立基于數字孿生的虛擬檢測系統,通過BIM模型預判施工風險;推動檢測數據與保險金融產品對接,構建工程質量保證的新生態。隨著智能傳感器成本的持續下降(據MarketsandMarkets預測,2026年將降低至現有價格的32%),該檢測體系有望成為新型建筑工業化進程中的標準配置,為工程質量提升提供持續的技術驅動力。

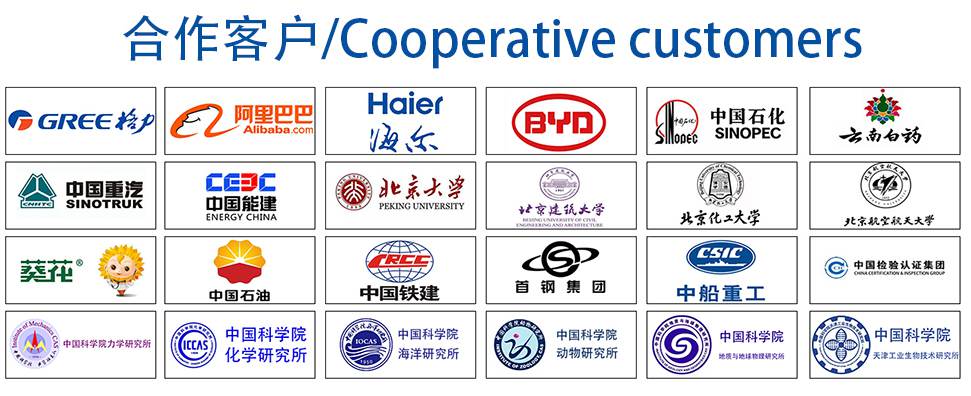