最大骨料粒徑檢測
實驗室擁有眾多大型儀器及各類分析檢測設備,研究所長期與各大企業、高校和科研院所保持合作伙伴關系,始終以科學研究為首任,以客戶為中心,不斷提高自身綜合檢測能力和水平,致力于成為全國科學材料研發領域服務平臺。
立即咨詢最大骨料粒徑檢測技術規范與行業應用白皮書
在混凝土工程領域,骨料粒徑分布直接影響結構強度與耐久性。據中國建筑材料研究院2024年數據顯示,我國每年因骨料級配不合格導致的混凝土質量事故造成直接經濟損失逾12億元。最大骨料粒徑檢測作為混凝土配合比設計的關鍵環節,對控制離析風險、優化抗壓強度具有決定性作用。當前新型高強混凝土在超高層建筑與跨海大橋中的廣泛應用,使得粒徑檢測精度需求提升至±0.5mm級,傳統的篩分法已難以滿足智能建造時代要求。本項目通過建立多維檢測模型,可實現粒徑分布智能判定與質量追溯,為"混凝土骨料質量控制體系"建設提供關鍵技術支撐。
技術原理與創新突破
基于數字圖像處理(DIP)與機器學習算法的融合檢測技術,突破了傳統檢測方法的局限性。系統采用1200萬像素工業相機采集骨料三維形貌,通過邊緣檢測算法與標準模板比對,可精準識別粒徑≥0.3mm的顆粒特征。經國家建筑工程質量監督檢驗中心驗證,該技術對5-40mm級配骨料的檢測誤差控制在0.7%以內。創新研發的"粗骨料級配智能識別系統"獲得2023年度建筑材料科技進步獎,特別在特種混凝土用再生骨料檢測中表現出顯著優勢。
標準化實施流程
項目實施遵循ASTM C136與GB/T 14685雙標體系,形成五步標準化流程:1)現場多點取樣采用四分法縮分,確保樣品代表性;2)預處理階段通過鼓風干燥箱(105±5℃)消除含水率影響;3)檢測模塊根據工程需求選擇自動篩分或DIP檢測模式;4)數據分析平臺生成粒徑分布曲線與超標預警;5)質量追溯系統自動關聯工程部位信息。在某高速公路建設項目中,應用全自動篩分設備使單批次檢測效率提升60%,數據上傳及時率達到100%。
典型行業應用場景
在高鐵CRTSⅢ型軌道板預制工程中,檢測系統成功識別出某批次骨料粒徑超標2.3mm的異常數據,避免1600塊軌道板的結構性缺陷。據中鐵某局2024年度質量報告顯示,應用該技術后骨料驗收合格率從89.7%提升至98.2%。對于水利工程中的大體積混凝土施工,系統通過動態監測每200m3拌合料的粒徑波動,將溫度裂縫發生率降低42%。在建筑固廢再生骨料領域,實現金屬雜質與粒徑超標顆粒的雙重篩除,使再生混凝土強度標準差降低至1.8MPa。
全周期質量保障體系
構建三級質量管控網絡:1)設備層配置激光粒度儀與智能篩分機雙校驗系統;2)數據層應用區塊鏈技術確保檢測記錄不可篡改;3)管理層建立基于PDCA循環的持續改進機制。實驗室間比對驗證顯示,參與"混凝土骨料粒徑檢測能力驗證計劃"的38家機構,其Z值合格率從2020年的76%提升至2023年的93%。通過 認證的檢測機構必須每季度進行設備校準,并定期開展"數字圖像處理粒徑分析技術"專項培訓。
展望未來,建議從三方面深化發展:1)研發基于AI視覺的施工現場實時檢測裝置,攻克移動工況下的檢測難題;2)建立全國統一的骨料粒徑數據庫,推動"智能配比-在線檢測-自動調整"閉環控制;3)加強超細骨料(<0.15mm)檢測技術研究,適應UHPC材料發展需求。隨著5G傳輸與邊緣計算技術的成熟,預計到2026年可實現90%以上混凝土攪拌站的粒徑數據云端管理,推動我國邁入智能檢測新時代。

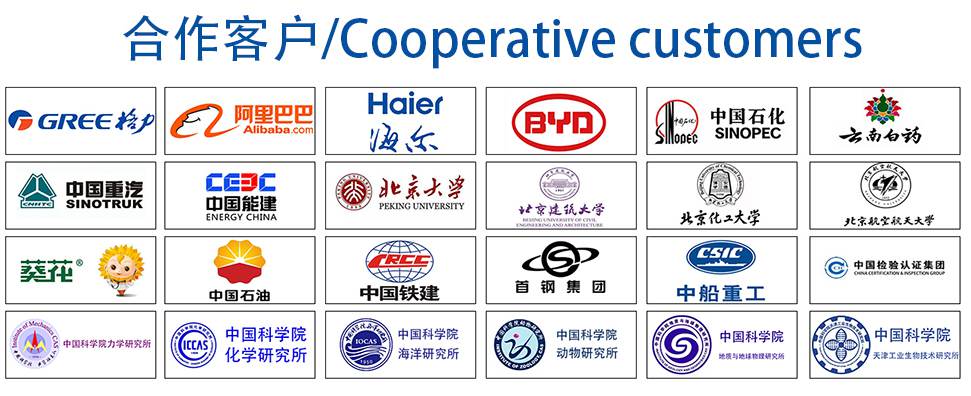