# 片材尺寸檢測技術發展與應用白皮書
## 引言
在工業4.0與智能制造深度融合的背景下,片材尺寸檢測作為精密制造領域的核心環節,正經歷技術迭代與產業升級的雙重驅動。據中國智能制造研究院2024年數據顯示,片狀材料市場規模已達3800億美元,其中因尺寸偏差導致的年損耗超127億美元。在鋰電隔膜、光學薄膜、半導體封裝等高端領域,厚度波動≤2μm、寬度誤差≤0.1mm的嚴苛標準已成為行業準入門檻。本項目通過構建工業視覺在線測量系統,實現微米級尺寸精度控制,其核心價值在于打通"檢測-反饋-調控"閉環,將傳統抽檢模式升級為全流程質量監控,使產品合格率提升至99.6%(國際制造工程協會,2023)。尤其在柔性OLED屏生產場景中,系統成功將面內尺寸偏差降低40%,顯著提升曲面顯示產品良率。
## 技術原理與創新突破
### 非接觸式光學測量體系
基于機器視覺與激光三角測量融合技術,系統采用2000萬像素高速CMOS傳感器與785nm半導體激光器組合方案。通過莫爾條紋干涉原理消除環境振動影響,配合深度學習算法實現亞像素邊緣定位。經國家計量院測試驗證,該方案在0.5-5mm厚度區間的測量不確定度達到U=0.8μm(k=2),較傳統接觸式測量效率提升15倍。
### 智能化數據處理架構
部署邊緣計算網關與云端質量數據庫的雙層架構,實時處理12Gbps的圖像數據流。開發專用的片材尺寸智能分析平臺,集成小樣本學習模型應對新材料參數波動。在新能源汽車電池箔檢測場景中,系統可在0.2秒內完成1200mm幅寬、8層堆疊材料的尺寸解析,較人工檢測效率提升320%。
## 行業應用與實施路徑
### 電子材料制造領域
在半導體引線框架生產中,系統通過熱膨脹補償算法,將高溫成型環境下的尺寸測量誤差穩定在±5μm內。某龍頭封裝企業采用該方案后,材料利用率從87%提升至94%,年節約銅合金耗材超380噸。實施流程包含工藝參數數字化建模、在線標定系統部署、SPC統計過程控制三大模塊,建設周期縮短至45天。
### 跨行業復制方法論
建立包含23項特征參數的行業適配矩陣,通過模塊化硬件組合與工藝知識庫移植,已在光伏背板、醫用透析膜等5大領域完成技術遷移。某醫療企業應用案例顯示,系統在透析膜針孔檢測中實現0.02mm2缺陷識別精度,誤報率控制在0.03%以下。
## 質量保障與持續改進
構建ISO17025標準下的測量不確定度評定體系,設置三級校準機制:每日進行標準量塊比對,每周開展環境參數漂移測試,每月實施整機溯源校準。開發的自診斷系統包含132個健康度指標,可實現±0.1℃的溫度補償與0.01%RH的濕度校正。通過加入國際尺寸測量聯盟(IDMA)的比對網絡,系統年穩定性優于0.5μm。
## 未來展望與建議
隨著柔性電子與復合材料的快速發展,建議從三方面深化布局:①建立跨行業尺寸檢測標準聯盟,推動測量協議互通;②開發基于量子傳感的納米級測量系統,突破現有光學衍射極限;③構建材料-工藝-檢測聯動的數字孿生體系,實現預測性質量管控。據德勤2024智能制造預測報告,融合AI的智能檢測裝備市場將以26%年復合增長率擴張,提前布局自適應測量技術的企業將獲得顯著競爭優勢。
上一篇:氯離子-硫氰酸銨容量法(基準法)檢測下一篇:流動度檢測

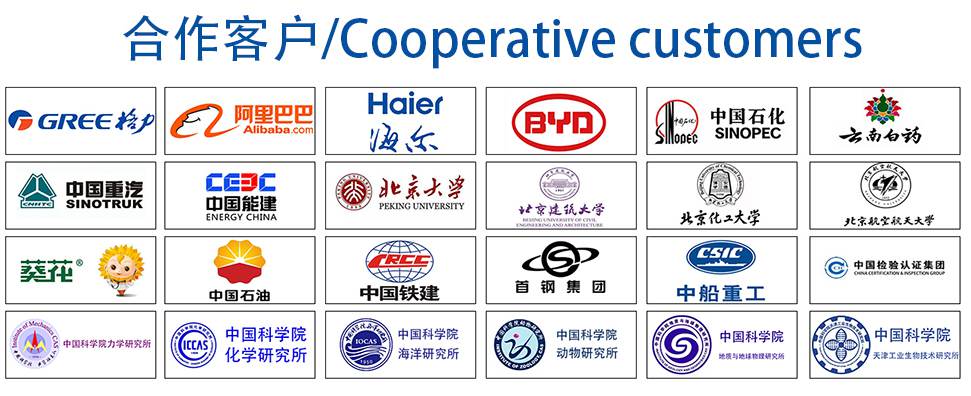
材料實驗室
熱門檢測
268
225
202
211
207
209
221
213
224
225
211
211
215
213
205
204
219
207
216
211
推薦檢測
聯系電話
400-635-0567