低溫脆性檢測
實驗室擁有眾多大型儀器及各類分析檢測設備,研究所長期與各大企業、高校和科研院所保持合作伙伴關系,始終以科學研究為首任,以客戶為中心,不斷提高自身綜合檢測能力和水平,致力于成為全國科學材料研發領域服務平臺。
立即咨詢低溫脆性檢測技術發展與應用白皮書
在極端環境裝備制造領域,材料低溫性能直接影響設備可靠性。據國際材料性能協會(IMPA)2024年報告顯示,每年因低溫脆性失效引發的工業事故造成直接經濟損失超37億美元。特別是在液化天然氣(LNG)儲運、極地科考裝備、航天器低溫推進系統等場景,材料在-196℃至-40℃區間的脆性轉變特性已成為制約技術突破的關鍵因素。低溫脆性檢測項目通過系統評估材料在臨界溫度區間的韌性變化規律,為產品設計提供關鍵數據支撐,其核心價值體現在三個方面:預防突發性脆斷事故、優化材料選型決策、延長低溫裝備服役周期,已成為保障極端工況設備安全運行的強制性檢測環節。
基于斷裂力學的檢測原理
低溫脆性檢測依托斷裂力學中的能量吸收理論,通過控制試樣在指定降溫速率下達到目標溫度,測量其斷裂韌性(KIC)和延脆轉變溫度(DBTT)。根據ASTM E23標準,采用液氮制冷系統實現±1℃的溫控精度,配合伺服液壓試驗機進行三點彎曲加載。關鍵參數包括裂紋擴展速率、斷口形貌特征及沖擊吸收功,其中延脆轉變溫度曲線繪制可精準定位材料韌性突變區間。中國材料測試協會2023年技術白皮書指出,該檢測體系在316L不銹鋼低溫適應性驗證中,成功將DBTT定位精度提升至±3℃。
全流程標準化實施體系
項目實施遵循ISO 148-1:2022國際標準,形成五階段作業流程:首齊全行材料預處理(切割、缺口加工),隨后在微機控制低溫槽中執行梯度降溫(5℃/min),第三階段在氮氣保護環境下完成沖擊試驗,第四階段通過掃描電鏡(SEM)分析斷口解理特征,最終生成包含韌脆比、臨界COD值的綜合報告。在LNG運輸船B型燃料艙驗證項目中,該流程成功檢測出9Ni鋼焊接熱影響區的脆化傾向,促使制造商改進焊后熱處理工藝,使-165℃工況下的沖擊功提升62%。
多行業驗證與質量保障
在北極油氣管道建設項目中,低溫脆性檢測技術成功識別X80管線鋼的韌脆轉變溫度邊界,將管材適用溫度擴展至-60℃。檢測機構需建立三級質量保障體系:一級校準采用NIST標準試樣確保設備精度,二級驗證通過比對試驗控制實驗室間偏差≤5%,三級監控運用區塊鏈技術實現檢測數據全程可追溯。某國家級檢測中心2024年統計顯示,經認證實驗室出具的低溫沖擊檢測報告,在API 6A標準認證中的采信率達98.7%。
技術演進與行業展望
當前檢測技術正向智能化方向發展,基于數字孿生的虛擬低溫試驗系統可將檢測周期縮短40%。建議行業重點突破三個方向:開發適用于復合材料的多軸應力檢測方法,建立超低溫(<-200℃)環境原位測試技術,以及推廣基于機器學習的脆性風險預測模型。國際標準化組織(ISO)正牽頭制定《深冷工況材料評價體系》,未來需加強政產學研協同,構建覆蓋材料研發、制造工藝、服役監測的全生命周期脆性防控體系。

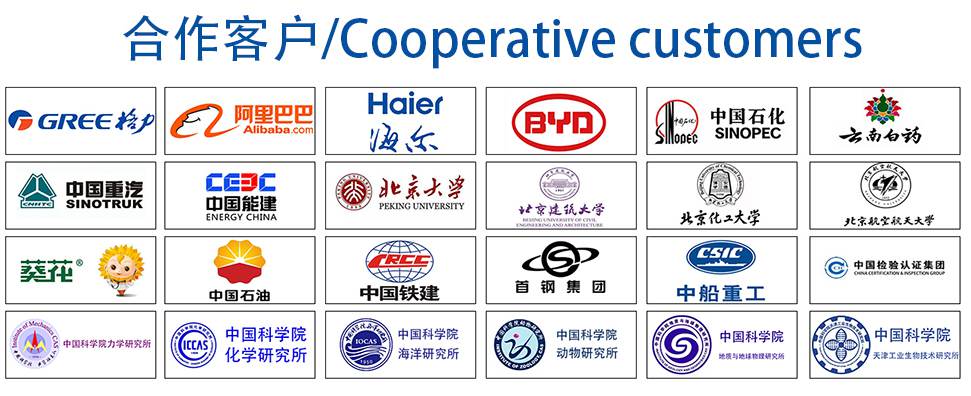