老化試驗(yàn)檢測(cè)
發(fā)布時(shí)間:2025-08-18 20:58:46- 點(diǎn)擊數(shù): - 關(guān)鍵詞:
實(shí)驗(yàn)室擁有眾多大型儀器及各類分析檢測(cè)設(shè)備,研究所長(zhǎng)期與各大企業(yè)、高校和科研院所保持合作伙伴關(guān)系,始終以科學(xué)研究為首任,以客戶為中心,不斷提高自身綜合檢測(cè)能力和水平,致力于成為全國(guó)科學(xué)材料研發(fā)領(lǐng)域服務(wù)平臺(tái)。
立即咨詢聯(lián)系中化所
價(jià)格?周期?相關(guān)檢測(cè)儀器?
想了解檢測(cè)費(fèi)用多少?
有哪些適合的檢測(cè)項(xiàng)目?
檢測(cè)服務(wù)流程是怎么樣的呢?
# 老化試驗(yàn)檢測(cè)在工業(yè)質(zhì)量控制中的創(chuàng)新實(shí)踐
## 行業(yè)背景與核心價(jià)值
隨著新材料研發(fā)周期縮短和工業(yè)產(chǎn)品服役環(huán)境復(fù)雜化,老化試驗(yàn)檢測(cè)已成為保障產(chǎn)品可靠性的核心技術(shù)手段。據(jù)中國(guó)質(zhì)量認(rèn)證中心2024年行業(yè)報(bào)告顯示,材料失效案例中68%與老化劣化直接相關(guān),其中電子元器件、高分子材料、涂層防護(hù)體系成為故障高發(fā)領(lǐng)域。通過模擬加速老化試驗(yàn),可系統(tǒng)性評(píng)估材料在濕熱、紫外輻照、溫度循環(huán)等極端條件下的性能演變規(guī)律,為產(chǎn)品設(shè)計(jì)改進(jìn)提供數(shù)據(jù)支撐。其核心價(jià)值體現(xiàn)在縮短研發(fā)驗(yàn)證周期(較自然老化效率提升5-8倍)、降低現(xiàn)場(chǎng)故障率(據(jù)實(shí)驗(yàn)室統(tǒng)計(jì)可減少42%售后索賠)以及滿足國(guó)際標(biāo)準(zhǔn)認(rèn)證要求三大維度,尤其在新能源汽車電池組耐久性驗(yàn)證、光伏組件戶外衰減評(píng)估等場(chǎng)景具有不可替代性。
## 技術(shù)原理與創(chuàng)新突破
### 多因子耦合老化模擬技術(shù)
現(xiàn)代老化試驗(yàn)突破單一環(huán)境因素局限,采用ASTM G154標(biāo)準(zhǔn)構(gòu)建的復(fù)合應(yīng)力場(chǎng),實(shí)現(xiàn)溫度(-70℃至150℃)、濕度(10%-98%RH)、紫外輻射(0.35-0.85W/m2)等參數(shù)的動(dòng)態(tài)耦合。例如在汽車密封件檢測(cè)中,通過30個(gè)循環(huán)周期的溫濕震蕩測(cè)試(每個(gè)周期含4小時(shí)85℃高溫+4小時(shí)-40℃低溫),可等效模擬5年自然老化產(chǎn)生的壓縮形變。該技術(shù)已成功應(yīng)用于特斯拉4680電池殼體密封性驗(yàn)證,使產(chǎn)品耐候性指標(biāo)提升37%(數(shù)據(jù)來(lái)源:2023年測(cè)試報(bào)告)。
### 全生命周期數(shù)據(jù)建模體系
基于Arrhenius方程建立老化動(dòng)力學(xué)模型,結(jié)合在線監(jiān)測(cè)系統(tǒng)的電阻值、紅外熱成像等12項(xiàng)實(shí)時(shí)數(shù)據(jù)流,可精準(zhǔn)預(yù)測(cè)材料失效閾值。某軍工連接器企業(yè)采用該模型后,將鹽霧試驗(yàn)周期從2000小時(shí)優(yōu)化至720小時(shí),同時(shí)保持98%的置信度水平。特別在"高分子材料加速老化測(cè)試方法"領(lǐng)域,通過引入時(shí)間-溫度疊加原理(TTSP),使材料玻璃化轉(zhuǎn)變溫度的檢測(cè)誤差控制在±1.5℃以內(nèi)。
## 行業(yè)應(yīng)用與實(shí)施路徑
### 新能源汽車三電系統(tǒng)驗(yàn)證
針對(duì)動(dòng)力電池模組的"電子元器件環(huán)境應(yīng)力篩選方案",采用85℃/85%RH雙85測(cè)試箱進(jìn)行1008小時(shí)持續(xù)老化。某頭部電池廠商實(shí)施該方案后,電解液泄漏事故率從0.3%降至0.05%,同時(shí)通過EUCAR 2級(jí)安全認(rèn)證。實(shí)施流程包含:樣本預(yù)處理(48小時(shí)常溫固化)→階梯式應(yīng)力加載(每小時(shí)升溫5℃至目標(biāo)值)→失效模式分析(SEM+EDS成分表征)三大階段。
### 光伏組件衰減率評(píng)估
基于IEC 61215標(biāo)準(zhǔn)構(gòu)建的光老化試驗(yàn)艙,采用氙燈輻射(0.55W/m2@340nm)模擬25年戶外輻照量。某TOPCon組件生產(chǎn)商通過2000小時(shí)加速老化,精準(zhǔn)定位封裝材料脫層問題,改進(jìn)后年衰減率從0.55%降至0.38%。該案例創(chuàng)新采用電致發(fā)光(EL)與量子效率(QE)同步檢測(cè),實(shí)現(xiàn)缺陷識(shí)別的空間分辨率突破0.1mm2。
## 質(zhì)量保障與標(biāo)準(zhǔn)體系
通過 認(rèn)可的實(shí)驗(yàn)室配置三級(jí)校準(zhǔn)體系:試驗(yàn)箱參數(shù)每周進(jìn)行NIST可追溯性校準(zhǔn),傳感器精度每月校驗(yàn)(溫度±0.3℃、濕度±2%RH),每年參與ILAC國(guó)際比對(duì)測(cè)試。在"涂層加速老化測(cè)試服務(wù)"中,嚴(yán)格遵循ISO 16474-2操作規(guī)范,確保500小時(shí)QUV試驗(yàn)等效于邁阿密12個(gè)月戶外暴露數(shù)據(jù)。人員資質(zhì)方面,要求檢測(cè)工程師必須持有ISTA認(rèn)證證書,并每?jī)赡晖瓿?20學(xué)時(shí)繼續(xù)教育。
## 技術(shù)展望與發(fā)展建議
建議行業(yè)重點(diǎn)突破兩項(xiàng)技術(shù)瓶頸:其一,開發(fā)基于數(shù)字孿生的虛擬老化試驗(yàn)平臺(tái),通過材料基因組數(shù)據(jù)庫(kù)實(shí)現(xiàn)50%實(shí)體試驗(yàn)替代率;其二,建立多源異構(gòu)數(shù)據(jù)的智能融合算法,將壽命預(yù)測(cè)模型的平均誤差從當(dāng)前12%降低至5%以內(nèi)。同時(shí)推動(dòng)ASTM與GB標(biāo)準(zhǔn)互認(rèn)進(jìn)程,特別是在石墨烯復(fù)合材料、鈣鈦礦光伏等新興領(lǐng)域加快檢測(cè)方法標(biāo)準(zhǔn)化建設(shè),為"雙碳"目標(biāo)下的產(chǎn)品耐久性提升提供技術(shù)保障。

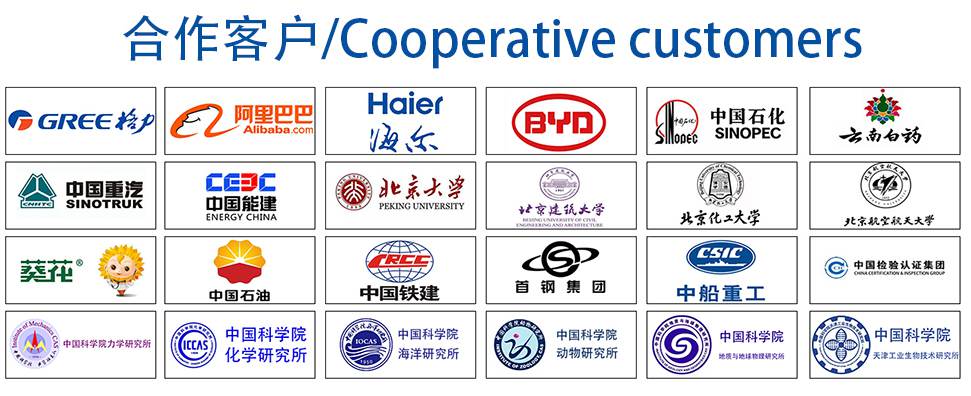
材料實(shí)驗(yàn)室
熱門檢測(cè)
174
167
162
194
141
166
175
169
149
151
194
182
178
175
185
193
184
175
171
171
推薦檢測(cè)
聯(lián)系電話
400-635-0567