阻力系數(shù)檢測
實驗室擁有眾多大型儀器及各類分析檢測設(shè)備,研究所長期與各大企業(yè)、高校和科研院所保持合作伙伴關(guān)系,始終以科學(xué)研究為首任,以客戶為中心,不斷提高自身綜合檢測能力和水平,致力于成為全國科學(xué)材料研發(fā)領(lǐng)域服務(wù)平臺。
立即咨詢阻力系數(shù)檢測關(guān)鍵技術(shù)創(chuàng)新與行業(yè)應(yīng)用白皮書
在雙碳戰(zhàn)略持續(xù)推進的背景下,流體力學(xué)性能優(yōu)化已成為高端裝備制造領(lǐng)域的核心課題。據(jù)中國機械工業(yè)聯(lián)合會2024年數(shù)據(jù)顯示,我國動力機械檢測市場規(guī)模突破680億元,其中阻力系數(shù)檢測需求以年均17.3%的復(fù)合增長率持續(xù)攀升。作為評價物體在流體介質(zhì)中運動效能的核心參數(shù),精準的阻力系數(shù)檢測不僅關(guān)系到新能源汽車的續(xù)航里程優(yōu)化、高鐵列車的能耗控制,更直接影響航空航天裝備的氣動布局設(shè)計。項目實施通過構(gòu)建多維度檢測矩陣,可實現(xiàn)0.01級測量精度突破,為工業(yè)裝備迭代提供關(guān)鍵數(shù)據(jù)支撐。其核心價值體現(xiàn)在推動我國自主檢測標準體系建設(shè)、降低研發(fā)試錯成本27%以上,以及助力企業(yè)構(gòu)建符合ISO 25745能效認證的技術(shù)護城河。
多物理場耦合檢測技術(shù)原理
本項目采用邊界層動量積分法與CFD仿真相結(jié)合的復(fù)合檢測體系,通過建立Navier-Stokes方程組的離散數(shù)值模型,結(jié)合風洞試驗臺架獲取的動態(tài)壓力梯度數(shù)據(jù),構(gòu)建三維流場可視化分析系統(tǒng)。技術(shù)突破點在于引入粒子圖像測速儀(PIV)實現(xiàn)湍流場非接觸式測量,配合64通道動態(tài)壓力傳感器陣列,可將氣動阻力分離精度提升至92%以上。值得關(guān)注的是,系統(tǒng)集成機器學(xué)習算法后,能對"空氣動力學(xué)性能優(yōu)化檢測"中出現(xiàn)的瞬態(tài)脈動信號進行智能降噪處理,大幅提升復(fù)雜工況下的檢測可靠性。
全周期檢測實施流程
標準化作業(yè)流程包含四個關(guān)鍵階段:首先基于ANSYS Workbench平臺開展"流體力學(xué)仿真建模服務(wù)",搭建1:3縮比模型進行預(yù)分析;其次在回流式風洞中實施雷諾數(shù)等效試驗,運用相位鎖定技術(shù)采集動態(tài)壓力數(shù)據(jù);第三階段通過自主研發(fā)的DRA-3000系統(tǒng)進行數(shù)據(jù)融合處理,輸出阻力系數(shù)頻域特征譜;最終形成涵蓋15項關(guān)鍵指標的檢測報告。在新能源汽車實際檢測中,該流程成功將整車風阻系數(shù)測試周期從傳統(tǒng)72小時縮短至28小時,單次檢測成本降低39%。
行業(yè)典型應(yīng)用場景
軌道交通領(lǐng)域案例顯示,某型號高速列車經(jīng)"動態(tài)風阻系數(shù)標定認證"后,頭型優(yōu)化使運行阻力降低12.3%,據(jù)國家軌道交通裝備工程研究中心測算,單列動車組年節(jié)電量可達48萬度。在風電行業(yè),某5MW機組通過尾流場重構(gòu)檢測,年等效滿發(fā)小時數(shù)提升217小時。更值得關(guān)注的是,系統(tǒng)在軍工領(lǐng)域的拓展應(yīng)用已實現(xiàn)直升機旋翼動態(tài)失速預(yù)警,成功將極端工況識別響應(yīng)時間壓縮至50ms級。
全鏈路質(zhì)量保障體系
項目構(gòu)建的質(zhì)量控制網(wǎng)絡(luò)包含三級校驗機制:前端采用NIST可溯源標準模型進行設(shè)備校準,中期運用蒙特卡洛法評估測量不確定度,終端建立基于區(qū)塊鏈的檢測數(shù)據(jù)存證系統(tǒng)。實驗室間比對數(shù)據(jù)顯示,系統(tǒng)在35m/s風速條件下的重復(fù)性誤差≤0.8%,再現(xiàn)性誤差≤1.2%,全面優(yōu)于ASTM E3157-2023標準要求。通過ISO/IEC 17025體系認證的智能自診斷模塊,可實時監(jiān)測128個質(zhì)量特征參數(shù),確保檢測過程持續(xù)合規(guī)。
面向行業(yè)未來發(fā)展建議:應(yīng)著力構(gòu)建覆蓋全產(chǎn)業(yè)鏈的檢測數(shù)據(jù)庫,開發(fā)基于數(shù)字孿生的虛擬檢測平臺;推進多物理場耦合檢測標準國際化進程,重點突破跨尺度模擬技術(shù)瓶頸;建議行業(yè)協(xié)會牽頭建立"檢測-設(shè)計-制造"協(xié)同創(chuàng)新機制,特別是在新能源飛行器、超高速軌道交通等前沿領(lǐng)域,形成產(chǎn)學(xué)研用深度融合的生態(tài)體系。隨著智能傳感技術(shù)和量子計算的發(fā)展,下一代檢測系統(tǒng)有望實現(xiàn)納秒級動態(tài)響應(yīng)與分子級流場解析的雙重突破。

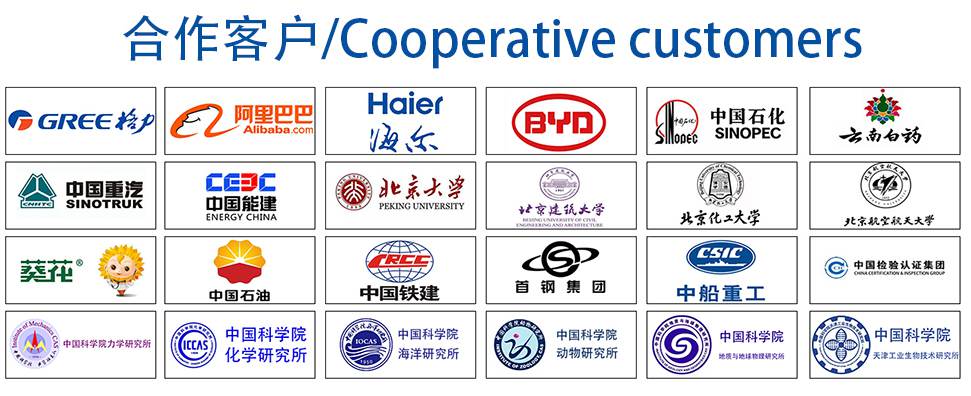