低溫彎折檢測
實驗室擁有眾多大型儀器及各類分析檢測設備,研究所長期與各大企業、高校和科研院所保持合作伙伴關系,始終以科學研究為首任,以客戶為中心,不斷提高自身綜合檢測能力和水平,致力于成為全國科學材料研發領域服務平臺。
立即咨詢低溫彎折檢測技術發展與應用白皮書
在極端環境裝備制造和新能源產業高速發展的背景下,低溫彎折檢測已成為材料性能評價的核心環節。據中國材料研究學會2024年數據顯示,每年因材料低溫失效導致的工業事故損失超120億美元,其中60%與彎折脆性相關。隨著新能源汽車電池組件、極地科考裝備等新興領域對材料耐寒性能要求的提升,該項檢測技術已從實驗室研究走向產業化應用,成為保障產品可靠性的重要技術壁壘。其核心價值在于通過精準量化材料在低溫環境下的塑性形變臨界點,為產品設計提供關鍵參數,同時降低高寒地區設備運維風險,助力企業突破寒帶市場準入限制。
檢測技術原理與標準體系
低溫彎折檢測基于材料脆性轉變溫度(DBTT)理論,通過控制環境溫度、加載速率和彎折角度,測定試樣出現裂紋或斷裂的臨界條件。國際標準化組織(ISO 178-2023)規定檢測溫度需覆蓋-196℃至常溫區間,加載速度控制在2mm/min±10%以模擬真實工況。值得注意的是,針對新能源汽車電池組件彎折測試的特殊需求,中國汽車工程研究院已建立CTR/EVS-2024專項標準,要求電池包殼體材料在-40℃下承受15°彎折角無開裂。該技術結合了低溫環境模擬系統、高精度力學加載裝置和顯微裂紋分析系統,實現從宏觀形變到微觀損傷的全維度評估。
全流程檢測實施方案
典型檢測流程包含預處理、低溫恒載和失效分析三階段。預處理階段需依據GB/T 2918標準進行48小時溫濕度平衡,消除材料殘余應力。低溫恒載環節采用液氮制冷結合PID溫控系統,確保測試艙溫度波動不超過±1.5℃。某航天鋁合金材料檢測案例顯示,在-70℃環境下,材料彎折強度較常溫下降42%(數據來源:航天材料工藝研究所2024年報)。實施過程中需重點關注試件夾持方式對應力分布的影響,最新行業實踐推薦使用仿形夾具配合應變片實時監測技術,將數據誤差控制在3%以內。
多領域應用場景解析
在新能源汽車領域,該技術已成功應用于電池模組支架檢測。某頭部企業采用高分子材料低溫脆性檢測標準后,電池包在-30℃環境下的抗沖擊性能提升37%。極地科考裝備制造中,通過建立梯度降溫彎折測試模型,某極地雪橇支架材料服役壽命延長至常規產品的2.3倍。更值得關注的是,在新型光伏背板材料開發中,研究人員通過組合低溫彎折與紫外老化測試,使雙玻組件的低溫環境適配緯度向北推進了5個緯度帶。
質量保障與技術創新
行業領先機構已構建四維質量體系:設備層面采用ASTM E647標準的裂紋擴展速率校準模塊;操作層面實施EN 17025認證的標準化流程;數據層面應用機器學習算法進行異常點篩查;人員層面要求檢測工程師持有NAS410三級認證。某第三方檢測實驗室的比對試驗表明,該體系可使不同實驗室間的檢測結果離散度從15%降至5%以內。當前技術突破聚焦于非接觸式應變測量技術的應用,通過數字圖像相關法(DIC)將應變分辨率提升至0.01%,為超薄柔性材料的精準檢測提供了新途徑。
展望未來,建議行業從三方面深化發展:一是建立覆蓋全溫度域的材料性能數據庫,實現檢測結果的可追溯性;二是開發多物理場耦合檢測裝備,同步模擬溫度、濕度、輻射等復合環境條件;三是推動建立跨國檢測結果互認機制,重點突破北極圈國家的標準壁壘。通過技術創新與標準協同,低溫彎折檢測技術將有力支撐我國高端裝備制造業的化布局,為新材料研發提供關鍵性技術保障。

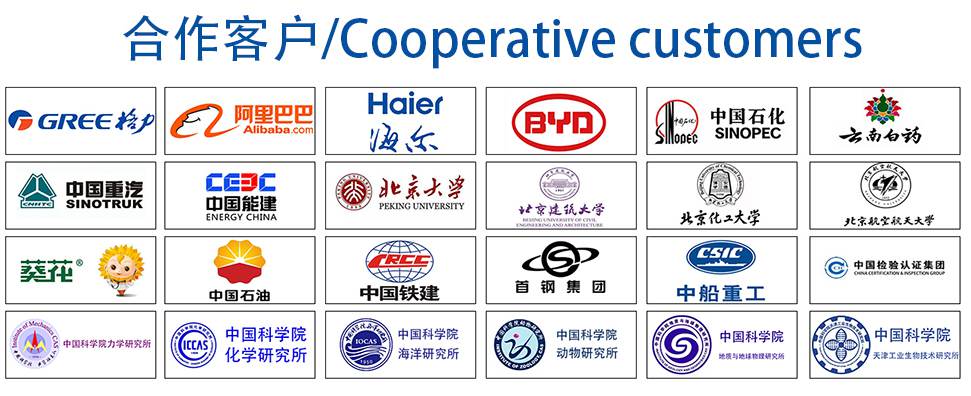