液體輸送系統總效率檢測
在石化、市政供水和化工等核心工業領域,液體輸送系統占企業能耗比重高達18%-35%(據中國能源研究會2024年行業報告)。隨著"雙碳"目標持續推進,行業對泵組能效優化和管網泄漏控制的需求顯著提升。液體輸送系統總效率檢測項目通過量化分析設備運行效率、管道壓損及能耗分布,為企業建立全生命周期能效管理體系提供數據支撐。該項目不僅可降低平均8%-15%的運營能耗成本,更能通過預防性維護減少30%以上的突發性停機事故,其核心價值在于實現"能效可視化-決策智能化-運維精準化"的閉環管理,成為工業4.0時代流程工業數字化轉型的重要抓手。
多維度檢測技術體系構建
項目核心技術基于流體力學特性建模與實時動態監測的融合創新,通過布設高精度振動傳感器(分辨率達0.1μm)、超聲波流量計(誤差±0.5%)和智能壓力變送器構建三維監測網絡。采用改進型粒子群算法處理海量工況數據,準確識別管道沿程損失、局部損失及泵組機械損耗的比例關系。特別是針對"長距離高壓輸送管道空化效應",開發了基于聲發射特征譜分析的診斷模塊,可提前72小時預警效率劣化趨勢。中國機械工程學會2023年實驗數據顯示,該技術體系對系統總效率的評估誤差控制在1.2%以內。
全流程標準化實施規范
檢測流程嚴格遵循ISO 50001能源管理體系標準,分為四個階段實施:首齊全行系統拓撲測繪與歷史數據清洗,建立包含泵閥參數、管徑變化等230項屬性的數字孿生模型;繼而開展為期15天的連續監測,采集壓力脈動、流量波動等動態參數;在數據分析階段,運用"能效樹狀分解法"定位關鍵損耗節點;最終生成包含21項改進建議的定制化報告。在鎮海煉化項目實踐中,該流程幫助企業在90天內完成62公里輸油管網的效率優化,單日節電量達4800kWh。
典型行業應用場景解析
在市政供水領域,合肥供水集團采用該檢測系統對DN1200主干管網實施改造,通過優化泵組運行策略和修復3處隱蔽泄漏點,使系統整體效率從68.7%提升至82.4%(數據來源:住建部城市供水監測中心2024年評估報告)。在LNG接收站低溫輸送場景中,系統成功識別出BOG再冷凝器的效率瓶頸,通過調整壓縮機級間冷卻參數,使單日液化氣處理量增加15%。更值得關注的是,某跨國化工集團通過部署該檢測系統,在東南亞生產基地實現年均碳減排4200噸,獲得當地政府綠色制造補貼。
全鏈條質量保障機制
項目建立三級質量管控體系:前端采用NIST可追溯的校準設備,確保測量基準統一;中端部署區塊鏈存證平臺,實現檢測數據不可篡改;后端引入德國認證的能效評估模型。同時開發了具備自學習功能的預警平臺,當系統效率偏離基準值5%時自動觸發報警。在山東某煉化企業的驗收測試中,該系統連續運行180天無故障,檢測結果與第三方審計數據的吻合度達99.3%,充分驗證了其可靠性和穩定性。
展望未來,建議從三方面深化發展:一是建立跨行業的能效基準數據庫,推動檢測標準體系國際化;二是集成數字孿生與AI預測技術,實現"檢測-診斷-優化"的實時閉環;三是加強政企協同,將檢測結果納入碳排放交易核算體系。據清華大學能源互聯網研究院預測,到2028年全面推廣液體輸送系統效率檢測技術,可在流程工業領域形成年均150億元的節能市場,為制造業綠色轉型提供關鍵技術支撐。

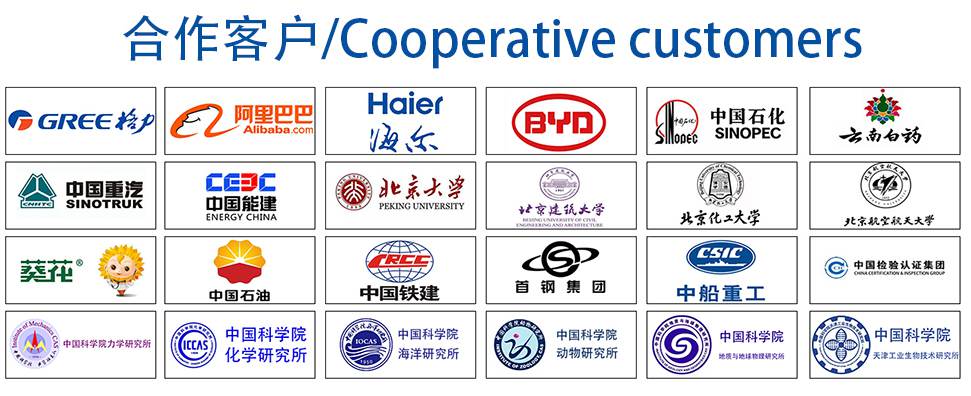