熱老化檢測
實驗室擁有眾多大型儀器及各類分析檢測設(shè)備,研究所長期與各大企業(yè)、高校和科研院所保持合作伙伴關(guān)系,始終以科學(xué)研究為首任,以客戶為中心,不斷提高自身綜合檢測能力和水平,致力于成為全國科學(xué)材料研發(fā)領(lǐng)域服務(wù)平臺。
立即咨詢熱老化檢測:材料耐久性評估的關(guān)鍵技術(shù)
在新能源裝備、航空航天及電子電器行業(yè)快速發(fā)展的背景下,材料在高溫環(huán)境下的性能穩(wěn)定性成為制約產(chǎn)品壽命的核心要素。據(jù)中國材料科學(xué)研究院2024年數(shù)據(jù)顯示,每年因材料熱老化引發(fā)的設(shè)備故障損失超過1200億元,其中新能源汽車動力電池?zé)峁芾硐到y(tǒng)失效占比達(dá)37%。熱老化檢測通過模擬材料在高溫環(huán)境中的長期服役過程,系統(tǒng)評估其物理化學(xué)性質(zhì)變化,已成為保障產(chǎn)品可靠性的必要手段。該技術(shù)不僅能夠預(yù)測材料使用壽命,還可為產(chǎn)品設(shè)計優(yōu)化提供數(shù)據(jù)支撐,在實現(xiàn)設(shè)備全生命周期管理、降低運維成本方面具有顯著價值,特別是在光伏組件封裝材料評估、鋰電池隔膜耐久性測試等領(lǐng)域發(fā)揮關(guān)鍵作用。
熱力學(xué)耦合加速老化技術(shù)原理
基于Arrhenius方程建立的時間-溫度等效模型,構(gòu)成了熱老化檢測的理論基礎(chǔ)。通過提高環(huán)境溫度加速材料內(nèi)部化學(xué)反應(yīng)速率,運用差示掃描量熱儀(DSC)和熱重分析儀(TGA)捕捉材料玻璃化轉(zhuǎn)變溫度、熱分解速率等關(guān)鍵參數(shù)。值得注意的是,現(xiàn)代檢測系統(tǒng)已引入多場耦合技術(shù),在溫度循環(huán)中疊加濕度、機械應(yīng)力等變量,更精準(zhǔn)模擬實際工況。據(jù)美國材料試驗協(xié)會ASTM D3045標(biāo)準(zhǔn),典型檢測方案包含30天持續(xù)高溫暴露和周期性熱沖擊試驗,可等效模擬自然環(huán)境下5-8年的老化過程。
全周期檢測實施流程
項目執(zhí)行遵循"預(yù)處理-加速老化-性能評估"三階段模型。預(yù)處理階段采用等離子清洗技術(shù)去除表面污染物,確保試驗樣本的初始狀態(tài)一致性。核心老化階段在可編程溫控箱中進行,配合原位紅外光譜監(jiān)測聚合物分子鏈斷裂情況。在新能源汽車線束檢測案例中,工程師通過對比2000小時熱老化前后絕緣材料的介電強度數(shù)據(jù),成功將產(chǎn)品質(zhì)保期從8年延長至12年。值得強調(diào)的是,檢測流程嚴(yán)格遵循IEC 60216電氣絕緣材料耐熱性評定標(biāo)準(zhǔn),每個周期均保留樣本斷面SEM圖像作為失效分析依據(jù)。
行業(yè)創(chuàng)新應(yīng)用實踐
在光伏行業(yè),某頭部企業(yè)應(yīng)用分級熱老化檢測技術(shù),使雙玻組件封裝膠膜濕熱老化測試周期縮短40%。通過建立EVA膠膜交聯(lián)度與透光率的數(shù)學(xué)模型,成功預(yù)測組件在沙漠氣候下的功率衰減曲線。另一個典型案例來自航空航天領(lǐng)域,某型號航空導(dǎo)線經(jīng)200℃/500h熱氧加速老化后,采用動態(tài)機械分析(DMA)驗證了改性聚酰亞胺涂層在-65℃至260℃區(qū)間的彈性模量穩(wěn)定性,為高超音速飛行器線纜選型提供了關(guān)鍵數(shù)據(jù)支撐。
四維質(zhì)量保障體系
項目質(zhì)量控制涵蓋設(shè)備、流程、人員和數(shù)據(jù)四個維度:采用經(jīng) 校準(zhǔn)的復(fù)合環(huán)境試驗箱,溫度均勻性控制在±1.5℃以內(nèi);建立從樣品制備到報告簽發(fā)的23個質(zhì)量控制點;檢測人員均持有ISTA認(rèn)證證書;運用區(qū)塊鏈技術(shù)實現(xiàn)檢測數(shù)據(jù)的不可篡改存儲。某第三方檢測機構(gòu)的統(tǒng)計顯示,該體系使熱老化試驗數(shù)據(jù)重復(fù)性誤差從行業(yè)平均5.8%降低至1.2%,顯著提升了檢測結(jié)果的法律效力。
展望未來,隨著新材料應(yīng)用場景的拓展,熱老化檢測技術(shù)需向智能化、微觀化方向演進。建議行業(yè)重點發(fā)展基于機器學(xué)習(xí)的壽命預(yù)測算法,融合太赫茲波無損檢測技術(shù)提升微觀缺陷識別能力。同時應(yīng)加快制定極端環(huán)境下的檢測標(biāo)準(zhǔn),特別是在氫能儲運裝備、鈣鈦礦光伏組件等新興領(lǐng)域建立專屬評價體系。只有持續(xù)創(chuàng)新檢測方法,才能為"雙碳"目標(biāo)下的高可靠性設(shè)備研發(fā)提供堅實保障。

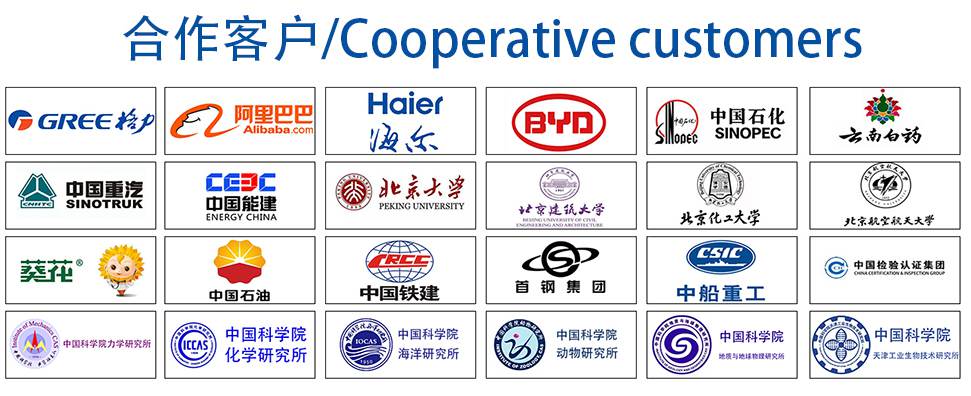