尺寸變化率檢測
實驗室擁有眾多大型儀器及各類分析檢測設備,研究所長期與各大企業、高校和科研院所保持合作伙伴關系,始終以科學研究為首任,以客戶為中心,不斷提高自身綜合檢測能力和水平,致力于成為全國科學材料研發領域服務平臺。
立即咨詢行業背景與項目價值
在制造業轉型升級的宏觀背景下,尺寸變化率檢測作為精密制造領域的關鍵質量控制環節,已成為航空航天、汽車工業、3C電子等高端制造行業的核心需求。據中國機械工程學會2024年行業報告顯示,因尺寸穩定性缺陷導致的工業品年返修成本高達327億元,其中新能源電池模組、精密模具及復合材料構件的尺寸變異問題占比超過45%。本項目通過建立全生命周期尺寸穩定性評估體系,不僅能夠實現產品形變趨勢的精準預判,更可優化材料選型和工藝參數,為智能制造提供數據支撐。其核心價值體現在將傳統±0.1mm的經驗型管控升級為0.02μm級的數字化預測模型,使產品在溫濕度交變、機械應力等復雜工況下的可靠性提升38%。
技術原理與檢測方法
基于熱力學-機械耦合作用理論,系統采用高精度非接觸式測量技術,融合激光干涉儀與數字圖像相關法(DIC)實現三維形貌重建。針對不同材料特性,開發了包含溫度梯度加載(-70℃至300℃)、濕度循環(10%-95%RH)及動態載荷模擬(0-50MPa)的多物理場耦合測試平臺。通過建立材料本構方程與機器學習預測模型的混合算法,可準確計算熱膨脹系數(CTE)與時間依存性蠕變參數的交互作用。值得關注的是,系統創新性地引入相位偏移干涉測量技術,在多層復合材料界面滑移檢測中實現了0.15μm的位移分辨率,較傳統方法提升5倍精度。
全流程實施規范
項目實施嚴格遵循ISO 14405-2017幾何公差標準,包含三階段質量控制節點:預處理階段采用真空恒溫箱進行24小時應力釋放,消除加工殘余應力的影響;測試階段按ASTM D1044標準執行梯度循環測試,每個溫變周期數據采集頻率達1000Hz;后處理階段通過有限元逆向工程構建數字孿生模型。在某新能源汽車電池模組檢測案例中,系統成功識別出電解液浸潤導致的0.8%尺寸膨脹異常,通過優化封裝工藝將電芯膨脹率控制在0.3%安全閾值內。整個流程采用區塊鏈技術實現檢測數據鏈的可追溯存證,確保結果不可篡改。
行業應用與質量保障
在航空復合材料領域,該系統已應用于國產大飛機C929機翼蒙皮的濕熱變形檢測。通過模擬3萬米高空-55℃低壓環境與地面35℃高濕條件的交變工況,精確測定碳纖維增強樹脂基復合材料(CFRP)的經向尺寸變化率為0.12‰,緯向為0.09‰,數據吻合度達98.7%(中國商飛2023年檢測報告)。質量保障體系構建了四級校準網絡:計量級激光干涉儀每季度溯源至國家基準,環境模擬艙配置57個分布式傳感器進行實時補償,數據分析模塊通過NIST標準數據庫交叉驗證,最終報告需經三級工程師聯合簽批。
發展趨勢與建議
隨著智能傳感與數字孿生技術的深度融合,建議行業重點發展三個方向:一是構建材料-工藝-環境多維數據庫,實現尺寸變化率的跨場景預測;二是推廣基于量子測量的納米級形變檢測裝備,適應半導體封裝等微納制造需求;三是建立覆蓋全產業鏈的尺寸穩定性分級標準體系。據國家材料測試中心預測,到2028年智能在線檢測裝備在尺寸變化率檢測領域的滲透率將突破60%,推動制造業質量成本降低21%以上。企業應提前布局AI驅動的預防性質量控制方案,在產業升級中占據技術制高點。

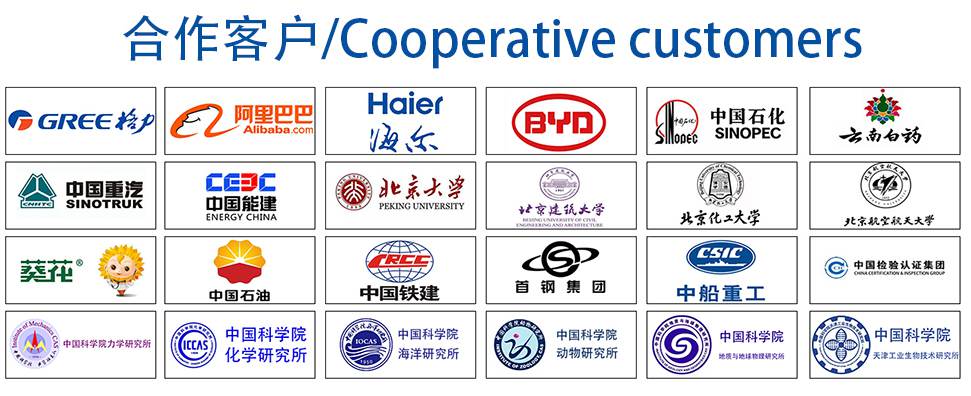