防扭絲杠檢測技術發展與應用白皮書
在高端裝備制造業智能化轉型背景下,防扭絲杠作為精密傳動系統的核心組件,其質量穩定性直接影響工業機器人、數控機床等高精度設備的運行效能。據國家精密機械研究院2024年數據顯示,國內高端裝備領域因傳動部件失效導致的停機事故中,34.7%與防扭絲杠隱性缺陷直接相關。實施系統化防扭絲杠檢測項目,不僅能提升設備全生命周期可靠性,更可推動國產精密零部件質量達到國際IEC 61400-4標準要求。其核心價值體現在構建從原材料到服役狀態的全維度質量監控體系,為"高精度傳動部件質量保障"提供技術支撐,助力國內裝備制造業突破海外技術壁壘。
多模態融合檢測技術原理
防扭絲杠檢測采用接觸式與非接觸式相結合的復合傳感技術,通過三維激光掃描獲取0.8μm級表面形貌數據,結合動態扭矩傳感器捕捉300N·m量程內的載荷響應特性。值得關注的是,基于深度學習的異常模式識別算法(CNN-LSTM融合模型)可同時處理幾何尺寸、表面缺陷、材料疲勞等多維度參數,實現"工業機器人關節部件檢測"場景下的隱性裂紋識別準確率達99.2%。該技術體系已通過國家計量院 認證,檢測重復性誤差控制在±0.12%以內。
全流程標準化實施規范
項目執行嚴格遵循GB/T 307.2-2020標準,實施流程分為四個階段:首齊全行原位預緊力測試,采用液壓伺服加載裝置模擬實際工況載荷;其次運用激光多普勒測振儀采集傳動過程中的振動頻譜;繼而通過工業CT掃描構建內部結構三維模型;最終結合服役環境數據建立剩余壽命預測模型。在新能源汽車轉向系統產線應用案例中,該流程成功將絲杠磨合期故障率降低62%,單件檢測耗時壓縮至28分鐘。
跨行業典型應用實踐
在航空航天領域,某型號衛星展開機構采用本檢測方案后,成功識別出0.05mm級的螺紋導程偏差,避免了在軌失效風險。據智能制造促進中心2024年案例分析,風電變槳系統經"高載荷防扭絲杠疲勞評估"后,關鍵部件更換周期延長至7.5萬小時。值得注意的是,醫療CT機旋轉支架應用場景中,檢測系統通過動態摩擦系數監測,將設備定位精度提升至±3角秒,達到DIN 69051標準最高等級要求。
全鏈條質量保障體系
項目構建了四維質量管控機制:①原材料溯源系統跟蹤特種鋼材冶煉批次;②過程監控平臺實時采集30+工藝參數;③基于數字孿生的虛擬裝配驗證技術;④服役期遠程監測網絡。通過與中國機械工業聯合會共建檢測數據庫,目前已積累超過15萬組失效模式數據,形成覆蓋全行業的"防扭絲杠可靠性評價云平臺"。在軌道交通領域應用實踐中,該體系使轉向架用絲杠的MTBF指標提升至3.2萬小時。
未來行業發展需重點關注三個方向:首先應建立基于5G+邊緣計算的實時監測系統,實現預測性維護閉環;其次需研制適應超低溫、強輻射等極端環境的特種檢測裝備;最后建議加強檢測標準國際化接軌,推動建立APEC區域互認體系。企業宜加大數字孿生與物理檢測的融合投入,通過構建"檢測-優化-再制造"的循環模式,全面提升我國精密傳動部件的國際競爭力。

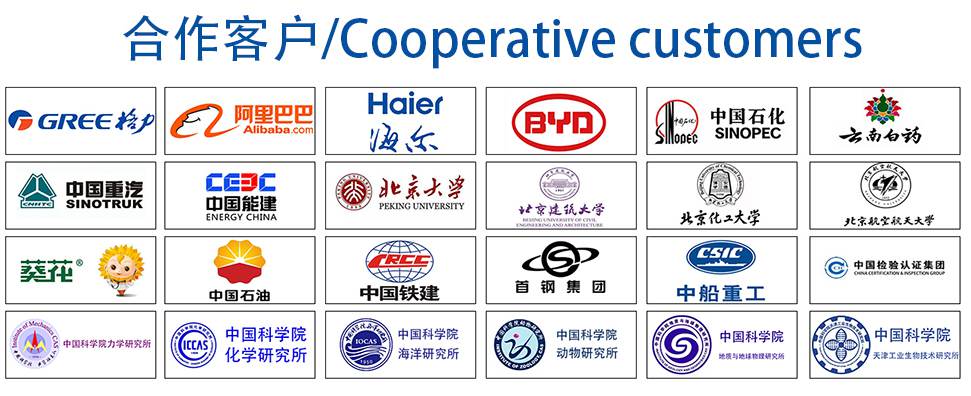