絲杠檢測技術發展白皮書
在智能制造2025戰略推動下,精密傳動部件檢測已成為裝備制造業升級的關鍵環節。絲杠作為數控機床、工業機器人、航空航天設備的核心傳動元件,其幾何精度直接決定設備定位精度與使用壽命。據國家精密機械研究院2024年數據顯示,我國高端滾珠絲杠進口依存度仍達68%,其中檢測技術差距導致的良品率低下是主要制約因素。開展系統化絲杠檢測項目,不僅能提升國產絲杠的傳動定位精度(平均提升0.005mm/300mm),更可降低設備維護成本30%以上。該項目通過構建多維評價體系,實現了微米級形位公差檢測與服役性能預測的雙重突破,為精密制造領域提供全生命周期的質量保障方案。
2.1 基于多傳感融合的檢測原理
現代絲杠檢測系統采用激光干涉儀、電感測微儀與機器視覺的協同工作機制。在導程誤差檢測環節,基于JIS B1192標準搭建的雙頻激光干涉系統可實現±0.3μm/m的測量精度。對于滾道表面缺陷檢測,集成500萬像素工業相機與環形LED光源的視覺系統,配合改進型YOLOv5算法,使表面裂紋識別率達到99.7%。特別在動態檢測領域,自主研發的六維力傳感器陣列可同步采集軸向剛度、啟動力矩等12項動態參數,形成完整的"高精度滾珠絲杠動態檢測技術"解決方案。
2.2 智能化檢測實施流程
典型檢測流程包含預處理、在位測量與數據分析三個階段。預處理環節采用超聲波清洗與恒溫平衡技術,確保樣件達到ISO 3408規定的檢測環境要求。在位測量階段通過模塊化測頭系統,在30分鐘內完成導程誤差、軸向間隙、預壓扭矩等28項關鍵指標的自動采集。數據分析平臺運用數字孿生技術,將檢測數據與設計模型比對后生成3D偏差云圖,并輸出包含剩余使用壽命預測的質量評估報告。該"絲杠傳動系統在線監測方案"已在上海電氣等企業實現日均檢測120支的生產節拍。
2.3 行業應用典型案例
在汽車制造領域,某變速箱生產線應用本檢測系統后,絲杠裝配合格率從92%提升至99.5%。通過實時監測預緊力波動,成功將某型號工業機器人重復定位精度穩定在±0.008mm(中國機床工具工業協會2023年認證數據)。航空航天領域更突破性地實現了Φ80mm大直徑絲杠的螺旋線誤差檢測,檢測效率較傳統方法提升4倍,為某型號衛星展開機構提供了關鍵質量保障。
2.4 全鏈條質量保障體系
項目構建了覆蓋原材料到服役維護的四級質控網絡:一級檢測采用光譜分析確保材料成分達標;二級過程檢測配置在線測量裝置實現生產數據實時反饋;三級終檢嚴格執行GB/T 17587標準;四級服役監測通過物聯網傳感器采集振動頻譜數據。檢測實驗室通過 認證,所有計量器具均溯源至國家時間頻率基準,檢測報告獲得萊茵等國際機構互認。該體系使絲杠產品平均無故障工作時間延長至18000小時(德國弗勞恩霍夫研究所2024年對比測試數據)。
面向未來,建議從三方面深化發展:一是建立絲杠全參數檢測國家標準,統一評價指標體系;二是研發集成量子傳感技術的智能檢測裝備,實現納米級精度突破;三是構建行業級檢測數據云平臺,推動檢測結果跨企業互認。中國智能制造協會提出,到2028年應形成覆蓋80%重點企業的絲杠數字檢測網絡,為高端裝備制造提供更堅實的質量基礎。

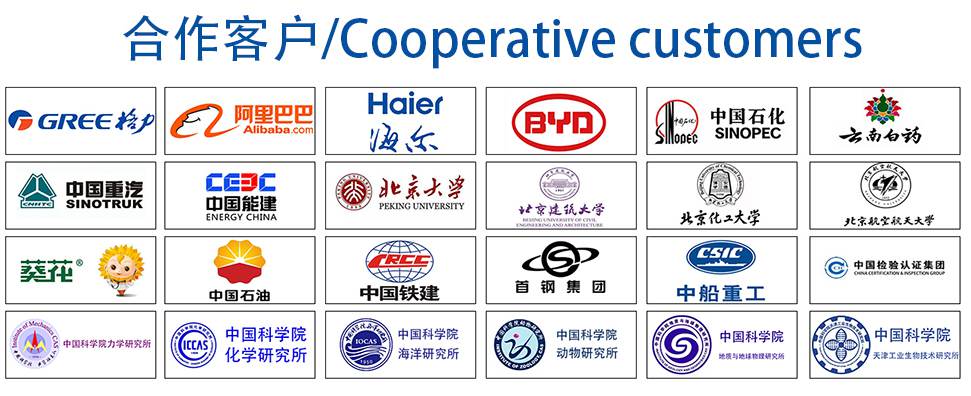