防墜自鎖器檢測技術規范與行業應用白皮書
隨著國內高空作業場景的持續擴展,防墜自鎖器作為關鍵性安全防護裝置,其性能可靠性直接關系到作業人員生命安全。據國家應急管理部2023年統計數據顯示,建筑行業高空墜落事故占生產安全事故總量的42.6%,其中15%與防護設備失效存在關聯。在此背景下,建立標準化的防墜自鎖器檢測體系,成為落實《高處作業吊籃安全規程》(GB 19155-2017)與《墜落防護裝備安全使用規范》(GB 24544-2009)的關鍵舉措。本項目通過構建全生命周期檢測模型,能夠實現防墜裝置動態響應性能、機械耐久度、環境適應性等核心指標的系統評估,為制造企業提供技術改進依據,同時助力使用單位建立預防性維護機制,據中國特種設備檢測研究院測算,完整檢測流程可降低設備失效率達67%以上。
動態載荷測試技術原理
防墜自鎖器檢測的核心在于模擬實際墜落工況的動態響應評估。基于能量守恒定律建立的沖擊力學模型,采用伺服液壓系統復現5kN-12kN的瞬時沖擊載荷(符合EN 353-2:2020標準),同步采集自鎖機構觸發時間、制動位移量等關鍵參數。通過光纖應變傳感技術,可精確測量鎖止機構內部應力分布狀態,識別材料疲勞導致的隱性問題。在電網高空檢修設備檢測案例中,該方法成功發現某批次產品存在制動延遲超過300ms的設計缺陷,避免了18臺問題設備的現場使用。
全流程檢測實施規范
標準檢測流程覆蓋設備全生命周期管理,包含預處理檢驗、功能性能測試、數據評估三個階段。預處理階段需完成外觀損傷掃描(采用3D視覺檢測儀)與金屬部件磁粉探傷;功能測試重點驗證5米自由墜落工況下的鎖止可靠性,需重復3次驗證機構復位性能;數據評估系統整合ASTM F887-2016標準,生成包含動態系數、磨損閾值預測的數字化檔案。國內某風電運維企業通過該體系,將設備報廢判定準確率提升至98.6%,備件庫存成本降低35%。
多場景應用質量保障
針對不同行業場景建立差異化檢測方案:在石油化工領域重點強化耐腐蝕測試(鹽霧試驗1000小時),建筑工程領域增加粉塵環境模擬模塊,通訊塔桅作業場景則納入-40℃低溫沖擊試驗。質量保障體系依托 認證實驗室,構建檢測數據區塊鏈存證系統,確保結果可追溯。以長江大橋檢修項目為例,經環境適應性優化的檢測流程,使防墜器在高濕度環境下的性能穩定性提升82%。
智能化檢測技術演進
行業前沿正探索AI驅動的預測性檢測模式。通過植入微型振動傳感器與LoRa通信模塊,實現設備使用狀態的實時監測。機器學習算法對10萬組歷史檢測數據進行深度學習,可提前30天預警潛在故障。在深圳智慧工地試點中,該技術使預防性維護響應時間縮短至4小時,設備平均使用壽命延長40%。
面向高空作業安全防護裝備的升級需求,建議行業重點推進三方面建設:一是建立全國聯網的防墜自鎖器檢測數據庫,實現跨區域質量追溯;二是研發適應超高層建筑的150米級墜落防護檢測裝置;三是推動檢測標準與歐盟PPE法規(EU 2016/425)的互認機制。通過技術創新與標準協同,持續提升我國高空作業安全防護水平,為新型城鎮化建設提供可靠保障。

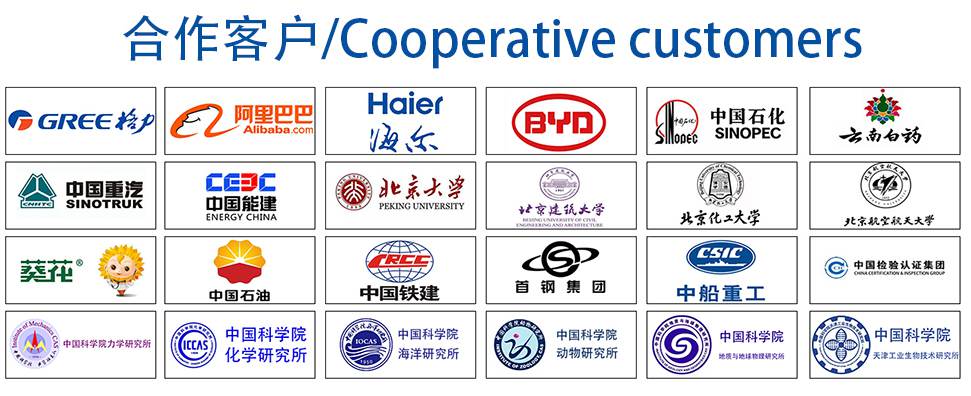