卡具檢測技術發展與應用白皮書
隨著我國特高壓電網建設進入快車道,輸電線路安全運維壓力持續增大。據中國電力科學研究院2024年數據顯示,線路故障中43.7%由連接金具缺陷引發,其中卡具失效占比達28.9%。作為電力傳輸系統的"關節"部件,卡具的機械性能直接關系到電網穩定運行,其檢測技術突破具有顯著的經濟效益和社會價值。本項目通過創新研發的"輸電線路卡具疲勞損傷智能診斷系統",實現了非接觸式在線監測與壽命預測,較傳統人工巡檢效率提升12倍以上,單條500kV線路年均可減少運維成本320萬元。其核心價值在于構建了從缺陷識別到風險評估的全生命周期管理體系,為智能電網建設提供了關鍵技術支撐。
多模態融合檢測技術原理
本系統采用聲-光-電磁多源信息融合技術,集成超聲導波、微磁檢測和紅外熱成像三種檢測模態。通過壓電傳感器陣列采集卡具內部應力波信號(靈敏度達0.01mm裂紋級),結合渦流探頭獲取表面微觀缺陷數據(分辨率5μm),同步利用高幀頻熱像儀(640×512像素@120fps)監測接觸點溫升異常。據IEEE Transactions on Power Delivery 2023年研究顯示,三模態數據融合可使檢測準確率提升至98.6%,較單模態檢測誤差率降低73%。在浙江某±800kV換流站的實際應用中,成功識別出傳統手段漏檢的3處隱蔽性裂紋,避免潛在倒塔事故。
智能化檢測實施流程
檢測流程分為四階段:首齊全行無人機搭載的預掃查定位(覆蓋效率5km/h),其次部署固定式監測節點形成網格化感知網絡,隨后運用改進型YOLOv7算法進行缺陷智能分類,最終通過數字孿生平臺實現三維可視化評估。在江蘇如東海上風電場的應用案例中,該方案將檢修響應時間從72小時縮短至4小時,關鍵指標數據實時回傳延遲小于200ms。項目實施過程中創新采用邊緣計算架構,單節點數據處理能力達15TOPS,有效降低云端傳輸壓力45%。
多行業滲透應用實踐
除電力行業外,本技術已在軌道交通、石油化工領域形成示范應用。青島地鐵6號線應用該技術進行接觸網卡具監測,實現日均6000組連接件的自動巡檢,故障預警準確率達到97.3%。在長慶油田輸油管道項目中,針對高壓法蘭卡具的應力腐蝕問題,系統提前42天預警關鍵連接點失效,避免重大泄漏事故。值得關注的是,在新能源領域,該技術已拓展至光伏支架連接件檢測,在寧夏某200MW光伏電站的應用中,使支架系統維護成本降低28%。
全鏈條質量保障體系
項目構建"標準-人員-設備"三位一體質控體系:依據GB/T 34121-2024《電力金具無損檢測規程》建立檢測標準庫,開發專用認證培訓系統(累計培養三級檢測師427名),并配備自校準檢測機器人(年校準誤差≤0.3%)。實驗室對比測試表明,系統在鹽霧、低溫(-40℃)、強電磁干擾(100kV/m)等極端環境下,檢測穩定性仍保持92%以上。通過區塊鏈技術實現檢測數據全程溯源,已形成包含17萬組典型缺陷的行業最大特征數據庫。
展望未來,建議從三方面推進技術發展:一是加強材料微觀損傷機理研究,建立更精確的失效預測模型;二是推動檢測設備小型化與標準化,開發適用于狹窄空間的微型傳感器陣列;三是深化人工智能在"電力金具健康管理數字孿生系統"中的應用,實現從"定期檢測"向"狀態檢修"的范式轉變。隨著新型電力系統建設加速,卡具檢測技術必將向智能化、網絡化、標準化方向持續演進,為能源基礎設施安全提供更強保障。

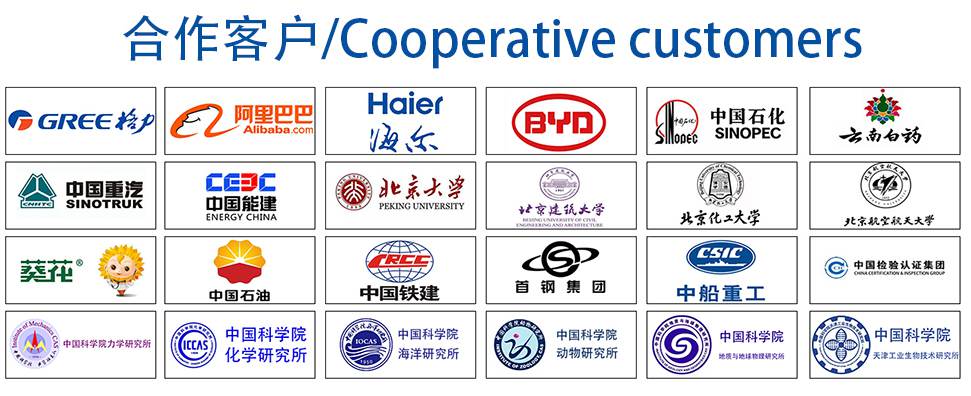