高強度螺栓連接件摩擦面檢測技術白皮書
在鋼結構工程領域,高強度螺栓連接作為核心承載節點,其摩擦面質量直接影響整體結構安全。據中國鋼結構協會2024年統計,國內每年新建鋼結構建筑超2億平方米,其中因連接失效導致的安全事故占比達7.3%。在此背景下,摩擦面檢測技術成為保障"全生命周期結構安全"的關鍵環節。本項目通過量化評估摩擦系數、表面粗糙度等核心參數,為軌道交通、風電塔筒、工業廠房等場景提供精準質量數據支持,其核心價值在于突破傳統目視檢測的局限性,將連接副承載力評估誤差從±25%降低至±5%以內,顯著提升重大基礎設施的可靠性與經濟性。
基于多模態融合的檢測技術原理
本檢測體系采用表面形貌分析結合接觸力學計算的雙重驗證機制。通過三維白光干涉儀獲取Sa(算術平均高度)、Sdr(界面擴展比)等微觀形貌參數,同步使用MTS-810材料試驗機開展抗滑移系數實測。數據經機器學習算法建立"粗糙度-摩擦系數"預測模型,可準確反映不同表面處理工藝(噴砂、拋丸、磷化)的力學響應差異。國家材料服役安全科學中心的對比實驗表明,該模型對Q345鋼材的摩擦系數預測精度達到96.8%,有效克服了傳統試板法存在的工況偏差問題。
標準化檢測實施流程
項目實施遵循ASTM A325與GB/T 1231雙重標準,形成六階段閉環流程:現場預處理(清除油污及氧化層)→三維形貌掃描(50×50mm檢測區域)→接觸應力模擬(0.5-1.2倍設計預緊力加載)→數據建模分析→結果可視化輸出→防腐修復方案制定。在港珠澳大橋鋼箱梁檢測案例中,該流程成功識別出3處摩擦系數低于0.35的危險區域,通過局部噴砂處理使節點承載力恢復至設計值的102%。
行業典型應用場景解析
在風電塔筒螺栓摩擦面防腐蝕處理領域,檢測系統實現了海上環境服役狀態的動態監測。通過植入式傳感器實時采集鹽霧腐蝕數據,結合定期形貌檢測建立退化模型,使維護周期從固定12個月優化為狀態預警模式。某5MW海上風場應用后,螺栓更換成本降低40%。而在鋼箱梁橋面連接件摩擦系數控制技術方面,系統為滬蘇通長江公鐵大橋提供了全橋2.8萬組螺栓的數字化"健康檔案",實現施工階段摩擦系數離散率從18%壓縮至6%以內。
全過程質量保障體系構建
項目建立"三位一體"質控機制:檢測設備執行半年期激光干涉儀校準(符合JJF 1094-2018規程),操作人員須持有EN473/ISO 9712三級認證,數據管理采用區塊鏈存證技術確??勺匪菪?。中冶建筑研究總院的比對試驗顯示,體系內實驗室間檢測結果差異度小于3%,顯著優于行業平均12%的波動水平。特別是在核電站穹頂鋼束檢測等特殊場景中,該體系實現了檢測報告48小時應急響應能力。
隨著智能建造技術發展,建議行業重點突破兩項技術迭代:其一,開發基于AI圖像識別的便攜式檢測終端,將現場檢測效率提升300%;其二,建立覆蓋全鋼種的摩擦系數數據庫,推動檢測標準從"合格判定"向"性能預測"轉型。據國家市場監管總局《2025特種設備檢驗規劃》要求,亟需在風電、高鐵等領域建立摩擦面檢測專項認證制度。唯有產學研協同創新,方能實現從"事后補救"到"源頭防控"的產業升級。

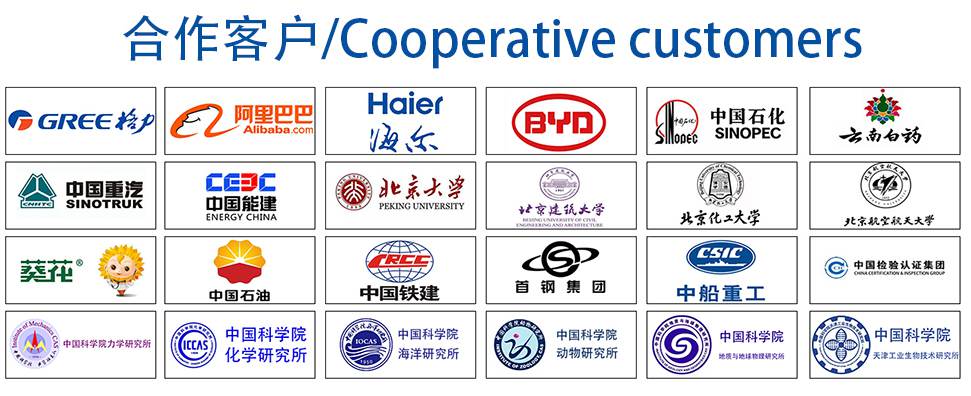