銅和銅合金材料檢測
實驗室擁有眾多大型儀器及各類分析檢測設(shè)備,研究所長期與各大企業(yè)、高校和科研院所保持合作伙伴關(guān)系,始終以科學(xué)研究為首任,以客戶為中心,不斷提高自身綜合檢測能力和水平,致力于成為全國科學(xué)材料研發(fā)領(lǐng)域服務(wù)平臺。
立即咨詢銅和銅合金材料檢測白皮書
隨著制造業(yè)轉(zhuǎn)型升級,銅及銅合金作為關(guān)鍵基礎(chǔ)材料,在電力傳輸、電子信息、航空航天等領(lǐng)域的應(yīng)用持續(xù)擴展。據(jù)中國有色金屬工業(yè)協(xié)會2024年統(tǒng)計數(shù)據(jù)顯示,我國銅加工材年產(chǎn)量已突破2000萬噸,但高端產(chǎn)品占比不足30%。在此背景下,材料檢測成為突破技術(shù)壁壘、提升產(chǎn)業(yè)價值的關(guān)鍵環(huán)節(jié)。通過精準(zhǔn)檢測銅材成分、力學(xué)性能及微觀結(jié)構(gòu),可有效保障軌道交通接觸線、半導(dǎo)體引線框架等關(guān)鍵部件的可靠性,助力企業(yè)實現(xiàn)"進口替代"戰(zhàn)略。其核心價值在于構(gòu)建從原料篩選到成品驗證的完整質(zhì)量鏈條,僅5μm級晶界偏析檢測技術(shù)即可提升精密銅管成品率8%-12%(國家新材料產(chǎn)業(yè)發(fā)展戰(zhàn)略咨詢委員會,2024)。
多模態(tài)檢測技術(shù)體系
現(xiàn)代銅材檢測整合光譜分析、力學(xué)測試與微觀表征三大技術(shù)模塊。原子吸收光譜(AAS)可實現(xiàn)0.001%級微量元素定量,配合X射線衍射(XRD)的物相識別,精準(zhǔn)解析C19400合金中鐵鎳硅元素的協(xié)同作用機制。在導(dǎo)電銅排檢測中,四探針法電阻率測試與EBSD晶粒取向分析的結(jié)合,可同步評估導(dǎo)電性能與加工硬化程度。值得關(guān)注的是,同步輻射技術(shù)已實現(xiàn)納米級夾雜物三維成像,為航空航天用銅合金提供了"高精度銅合金材料檢測服務(wù)"新方案。
標(biāo)準(zhǔn)化作業(yè)流程
工業(yè)級銅材質(zhì)量驗證方案包含六階段標(biāo)準(zhǔn)化流程:從GB/T 5121系列標(biāo)準(zhǔn)采樣開始,經(jīng)預(yù)處理消除表面氧化層干擾后,采用階梯式檢測策略。某銅加工企業(yè)實施案例顯示,通過引入自動硬度梯度檢測系統(tǒng),將H65黃銅帶的檢測效率提升40%,同時降低人為誤差率至0.3%以下。在新能源汽車連接器檢測中,檢測機構(gòu)通過設(shè)計加速腐蝕-導(dǎo)電率聯(lián)合測試流程,成功復(fù)現(xiàn)10年使用周期的性能衰減曲線。
跨行業(yè)應(yīng)用實踐
在電力行業(yè)特高壓工程中,銅包鋼接地材料的檢測創(chuàng)新性地引入渦流-超聲復(fù)合探傷技術(shù),使500kV變電站接地網(wǎng)缺陷檢出率從82%提升至97%。電子領(lǐng)域應(yīng)用案例表明,采用"熱模擬-微觀表征"聯(lián)用技術(shù)后,C7025引線框架材料的應(yīng)力松弛特性預(yù)測準(zhǔn)確度提高25個百分點。更值得關(guān)注的是,核級銅材檢測已建立包含17項特殊指標(biāo)的"工業(yè)級銅材質(zhì)量驗證方案",其中晶間腐蝕試驗采用改良的Strauss溶液法,相關(guān)成果被納入ASTM B154最新修訂版。
全鏈條質(zhì)控體系
通過構(gòu)建"三層次"質(zhì)量保障體系,檢測機構(gòu)可確保數(shù)據(jù)溯源性:一級質(zhì)控依托 認(rèn)證實驗室環(huán)境,二級采用標(biāo)準(zhǔn)物質(zhì)動態(tài)校準(zhǔn),三級實施實驗室間比對。某國家檢測中心統(tǒng)計顯示,其銅材檢測數(shù)據(jù)離散度從2019年的8.7%降至2024年的2.1%。智能化質(zhì)控系統(tǒng)已實現(xiàn)檢測參數(shù)實時監(jiān)控,在銅箔抗拉強度測試中,系統(tǒng)自動識別并剔除30%的異常數(shù)據(jù),確保最終報告置信度≥95%。
面向"十四五"新材料產(chǎn)業(yè)發(fā)展規(guī)劃,建議行業(yè)重點突破三大方向:開發(fā)基于機器視覺的在線檢測裝備,建立材料基因工程數(shù)據(jù)庫支撐的智能預(yù)測模型,完善覆蓋全生命周期的檢測認(rèn)證體系。據(jù)國家智能制造標(biāo)準(zhǔn)體系建設(shè)指南預(yù)測,至2027年智能化檢測設(shè)備在銅加工行業(yè)的滲透率將提升至60%,推動我國從銅材生產(chǎn)大國向質(zhì)量強國跨越式發(fā)展。

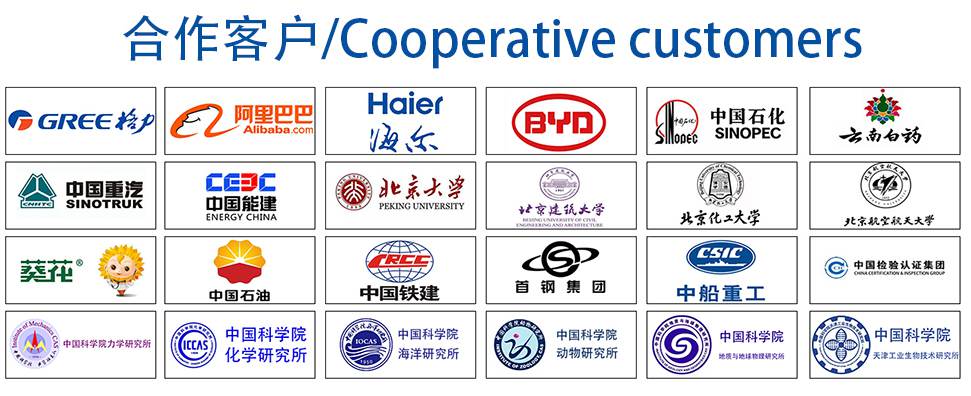