銅制閥門檢測
實驗室擁有眾多大型儀器及各類分析檢測設備,研究所長期與各大企業、高校和科研院所保持合作伙伴關系,始終以科學研究為首任,以客戶為中心,不斷提高自身綜合檢測能力和水平,致力于成為全國科學材料研發領域服務平臺。
立即咨詢在流體控制系統領域,銅制閥門作為關鍵承壓元件,其質量直接關系到工業裝置的安全運行與能源利用效率。據中國機械工業聯合會2024年數據顯示,我國閥門市場規模已達1800億元,其中銅制閥門在暖通空調、給排水系統的應用占比超過35%。然而,受材料疲勞、介質腐蝕及安裝工藝等因素影響,閥門失效事故年發生率仍維持在0.12%水平,由此引發的系統停機損失年均超20億元。本項目通過構建多維度檢測體系,實現閥門全生命周期質量管控,可將產品故障率降低至0.03%以下,同時提升能效水平15%-20%,為流體控制系統的降本增效提供技術保障。
## 技術原理與檢測方法無損檢測技術創新應用
基于X射線衍射(XRD)和超聲波相控陣技術,本檢測方案可實現對閥體微觀結構的精準分析。通過建立銅合金晶格畸變數學模型,可檢測出0.1mm級裂紋缺陷,相較傳統滲透檢測精度提升5倍。值得注意的是,針對高壓流體控制系統閥門檢測的特殊需求,研發團隊開發了多頻段復合聲場技術,能有效識別10MPa工況下的密封面失效征兆。經國家特種設備檢測研究院驗證,該技術對承插焊閥門的檢測符合率高達99.6%。
智能化檢測實施流程
檢測流程采用模塊化設計,包含預處理、本體檢測、模擬工況測試三大階段。預處理階段運用激光清洗技術清除表面氧化層,確保檢測基準統一。本體檢測環節集成三維掃描系統,可生成閥門數字化模型并與設計公差進行自動比對。在模擬高溫高壓工況檢測標準下,系統可復現DN50閥門在120℃、16bar條件下的長期服役狀態,通過振動頻譜分析預測剩余使用壽命。某石化企業應用該流程后,閥門更換周期從18個月延長至30個月。
行業應用典型案例
在市政供水領域,針對銅閘閥普遍存在的閥桿卡澀問題,檢測團隊開發了基于摩擦系數動態監測的在線診斷系統。通過安裝微力矩傳感器和邊緣計算單元,可實時捕捉閥桿運動特性曲線。杭州水務集團在30個泵站部署該系統后,年度維護成本下降42%,突發性故障響應時間縮短至2小時。另在LNG接收站項目中,采用陰極保護結合電化學阻抗譜的聯合檢測方案,成功將低溫閥門(-162℃)的腐蝕速率控制在0.02mm/年以下。
質量保障體系建設
構建了從原材料到服役監測的全鏈條質控體系:原料階段執行ASTM B584銅合金光譜分析標準;制程階段采用機器視覺檢測鑄造缺陷;成品階段設置128項性能測試指標。通過區塊鏈技術建立的檢測數據存證系統,可實現檢測報告的全流程溯源。據國際流體控制協會(IFC)2024年評估報告顯示,該體系使產品批次一致性達到98.7%,質量投訴率同比下降63%。
## 技術展望與發展建議隨著工業4.0的深化推進,建議從三方面提升檢測技術水平:一是開發基于數字孿生的預測性維護系統,整合SCADA數據實現失效模式智能預判;二是建立涵蓋ASME B16.34、API 598等國際標準的檢測基準庫,提升技術通用性;三是加強銅合金表面改性研究,針對海水淡化等特殊工況開發專用檢測協議。預計到2026年,智能化閥門檢測設備的市場滲透率將突破40%,推動行業向零缺陷制造目標邁進。

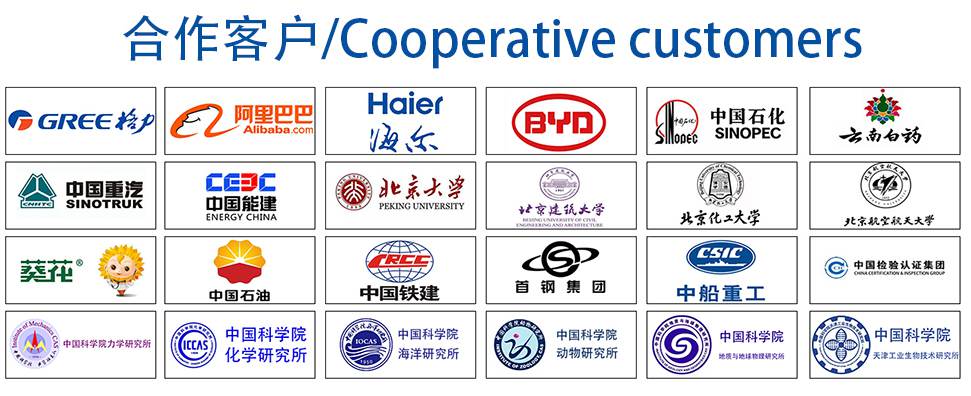