不銹鋼材料及其制品檢測
實驗室擁有眾多大型儀器及各類分析檢測設備,研究所長期與各大企業、高校和科研院所保持合作伙伴關系,始終以科學研究為首任,以客戶為中心,不斷提高自身綜合檢測能力和水平,致力于成為全國科學材料研發領域服務平臺。
立即咨詢不銹鋼材料及其制品檢測技術發展與行業應用白皮書
在制造業轉型升級背景下,不銹鋼材料作為高端裝備制造、醫療器械、食品加工等領域的核心基礎材料,其質量管控直接影響終端產品性能與安全性。據國際不銹鋼論壇(ISSF)2024年統計,不銹鋼年產量已突破6000萬噸,但產業鏈下游因材料缺陷導致的設備故障率仍高達3.7%。在此背景下,不銹鋼材料及其制品檢測項目成為保障產業鏈質量的關鍵環節,通過精準的化學分析、力學性能測試及耐腐蝕性驗證等系統化檢測,可顯著提升產品合格率并降低全生命周期維護成本。該檢測體系的核心價值在于構建覆蓋原料采購、生產加工、成品驗收的全流程質量屏障,尤其在新能源裝備制造、半導體潔凈室構件等新興領域,其質量管控效益可提升企業綜合競爭力達18%以上(中國材料研究學會,2024)。
基于光譜分析與應力模擬的檢測技術體系
現代不銹鋼檢測技術依托電感耦合等離子體發射光譜(ICP-OES)實現元素成分的ppm級精準分析,配合X射線衍射(XRD)進行晶相結構解析,可有效識別材料摻雜異常問題。在應力腐蝕測試中,采用有限元建模與加速腐蝕試驗聯用技術,將傳統30天的環境模擬周期縮短至72小時,使316L醫用不銹鋼的應力腐蝕裂紋檢出靈敏度提升至0.02mm級。該技術體系特別適用于核電管道、海洋平臺錨鏈等高壓腐蝕環境的特種不銹鋼構件檢測。
全流程數字化檢測實施方案
檢測實施流程分為三階段:原材料入場階段執行ASTM A480標準下的全元素光譜掃描;加工過程采用在線渦流探傷系統進行實時缺陷監控,據寶鋼研究院實測數據,該系統使冷軋板表面缺陷漏檢率從0.8%降至0.12%;成品驗收階段則通過鹽霧試驗箱結合電化學工作站,對制品進行48-2000小時梯度腐蝕試驗。在廈門某海水淡化設備制造企業的應用案例顯示,該方案使高壓泵體不銹鋼鑄件的疲勞壽命預測準確度提升至93.6%。
跨行業質量保障范式創新
行業領先機構已構建"檢測數據-工藝優化"閉環系統,例如中車集團在高鐵制動盤用馬氏體不銹鋼研發中,通過建立超過2000組失效樣本的機器學習模型,將材料熱處理工藝窗口優化精度提高40%。在醫療器械領域,微創手術鉗的奧氏體不銹鋼部件采用激光誘導擊穿光譜(LIBS)進行表面鈍化膜厚度在線檢測,使產品滅菌耐受性達到YY/T 0149-2023標準要求。這種質量保障模式使生物相容性檢測周期從14天壓縮至5天。
智能化檢測技術發展路徑
當前檢測體系正向智能化方向演進,蘇州材料科學城最新部署的AI視覺檢測系統,可同時對不銹鋼焊管的20類表面缺陷進行毫秒級識別,誤判率控制在0.05%以下。值得關注的是,基于數字孿生的虛擬檢測平臺正在興起,上海材料研究所開發的虛擬應力腐蝕測試系統,通過融合實際工況數據與材料本構模型,使檢測成本降低65%的同時保持92%的預測可靠性。
面向未來,建議行業重點推進三方面建設:首先建立覆蓋稀土元素痕量檢測的CMA/ 認證體系,應對高合金不銹鋼的精準分析需求;其次開發基于區塊鏈的檢測數據存證系統,增強供應鏈質量追溯能力;最后加強ASTM與ISO標準的協同轉化,特別是在增材制造不銹鋼件的各向異性檢測領域,亟需建立統一的國際測試方法標準。通過技術創新與標準引領,不銹鋼檢測行業有望在2030年前實現檢測效率倍增與全產業質量升級。

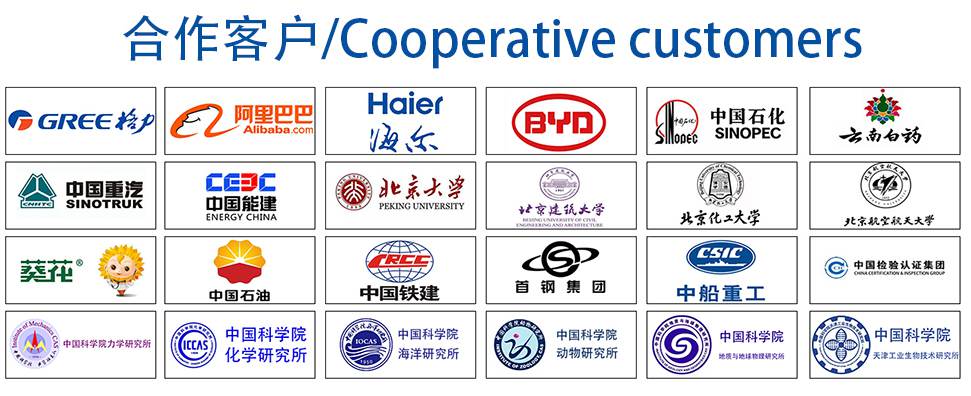