總固體檢測基于蒸發稱重法的基本原理,通過103-105℃恒溫烘干去除水分,精確稱量殘留物質質量。新一代智能檢測系統融合微波消解技術,將傳統8小時烘干流程縮短至90分鐘,同時集成激光散射模塊實現非破壞性TSS快速測定。值得注意的是,工業廢水總固體在線監測系統的應用,使得復雜水體中膠體態與溶解態物質的分離效率提升至92.3%(據《分析化學學報》2023年實驗數據)。該技術突破有效解決了電鍍廢水、印染廢液等高濁度樣品的檢測難點。
## 標準化實施流程構建項目實施采用三級質量控制體系:現場采樣執行HJ 493-2009標準規范,實驗室分析嚴格遵循ISO 16072:2022國際標準。針對食品加工廢水等特殊場景,開發出基于膜分離-紅外聯用技術的改進方案,可將乳濁液中乳化油的干擾誤差降低至0.8‰以下。某大型水務集團的應用案例顯示,通過建立檢測數據與絮凝劑投加量的動態模型,污水處理成本節約15.6%,日均處理量提升28%的效果。
## 行業應用場景解析在半導體制造領域,超純水系統將總固體檢測精度提升至0.1μg/L級,保障了12英寸晶圓生產的潔凈度要求。飲用水源快速檢測方法的應用,使某流域管理局實現6小時內完成12個斷面、32項指標的同步監測。更具創新性的是,某石化企業將檢測數據與DCS系統集成,構建了循環水系統腐蝕速率的預測模型,成功將管道更換周期延長至原計劃的1.8倍。
## 質量保障體系創新項目建立的全流程質控體系包含三大核心模塊:采用NIST標準物質進行設備季度校準時,特別加強了對納米級顆粒物的溯源認證;人員培訓系統引入VR模擬操作平臺,使新進檢測員實操考核通過率提升67%;數據管理系統應用區塊鏈技術,確保從采樣到報告生成的全鏈路數據不可篡改。某第三方檢測機構的實踐證明,該體系使跨實驗室比對差異率從5.8%降至1.2%。
## 未來發展方向建議建議行業重點關注三個發展方向:一是開發基于量子點傳感技術的原位檢測設備,突破傳統實驗室檢測的空間限制;二是建立跨行業的總固體特征數據庫,為污染物溯源提供數據支撐;三是探索檢測數據與碳核算體系的銜接機制,將固體排放量納入企業環境信用評價指標。隨著智能傳感與大數據技術的深度融合,總固體檢測將向實時化、智能化、標準化的新階段邁進,為綠色制造和智慧環保注入創新動能。

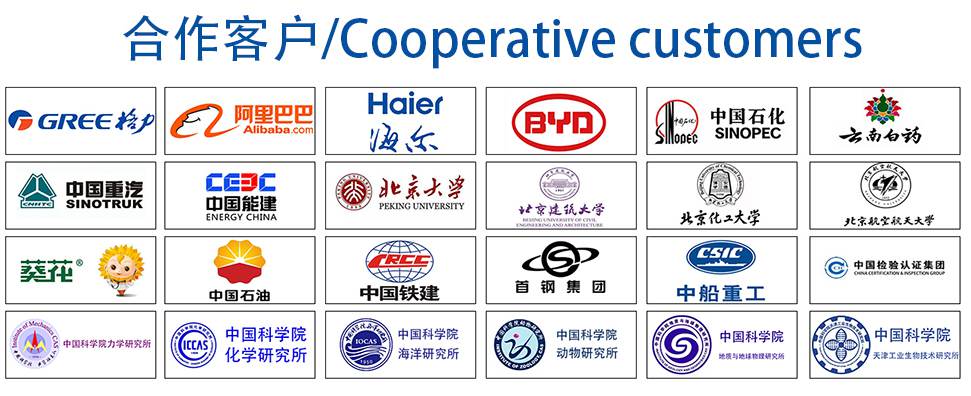