薄膜和薄片檢測(cè)
實(shí)驗(yàn)室擁有眾多大型儀器及各類分析檢測(cè)設(shè)備,研究所長(zhǎng)期與各大企業(yè)、高校和科研院所保持合作伙伴關(guān)系,始終以科學(xué)研究為首任,以客戶為中心,不斷提高自身綜合檢測(cè)能力和水平,致力于成為全國(guó)科學(xué)材料研發(fā)領(lǐng)域服務(wù)平臺(tái)。
立即咨詢聯(lián)系中化所
薄膜和薄片檢測(cè)技術(shù)白皮書
在新能源、電子元器件及柔性包裝行業(yè)高速發(fā)展的背景下,薄膜和薄片材料已成為鋰離子電池隔膜、光伏背板、光學(xué)顯示模組等關(guān)鍵部件的核心材料。據(jù)中國(guó)材料檢測(cè)研究院2024年數(shù)據(jù)顯示,我國(guó)功能性薄膜市場(chǎng)規(guī)模突破3200億元,但產(chǎn)品良率仍徘徊在92%-95%之間,微米級(jí)缺陷導(dǎo)致的直接經(jīng)濟(jì)損失年均超80億元。在此背景下,薄膜和薄片檢測(cè)項(xiàng)目通過構(gòu)建高精度、全流程的質(zhì)量控制體系,成為提升產(chǎn)業(yè)鏈協(xié)同效率的關(guān)鍵環(huán)節(jié)。項(xiàng)目的核心價(jià)值體現(xiàn)在突破傳統(tǒng)人工抽檢的局限性,實(shí)現(xiàn)缺陷檢出率從85%提升至99.7%,同時(shí)通過引入"微米級(jí)缺陷智能識(shí)別系統(tǒng)",使檢測(cè)效率提高4倍以上,為高端制造領(lǐng)域提供可靠的質(zhì)量保障。
多模態(tài)融合檢測(cè)技術(shù)原理
基于光學(xué)干涉成像與太赫茲波譜分析的雙模態(tài)檢測(cè)技術(shù),可實(shí)現(xiàn)材料內(nèi)部結(jié)構(gòu)的三維重構(gòu)與異物精準(zhǔn)定位。結(jié)合深度學(xué)習(xí)的"多光譜共焦掃描系統(tǒng)",能夠同步捕捉0.2μm以上的針孔、劃痕及厚度不均缺陷。值得注意的是,該系統(tǒng)通過自適應(yīng)算法優(yōu)化,將傳統(tǒng)線陣CCD的成像誤差從±1.5%降至±0.3%。據(jù)國(guó)際光學(xué)工程學(xué)會(huì)2023年技術(shù)白皮書披露,該技術(shù)方案在15μm厚度的鋰電池隔膜檢測(cè)中,首次實(shí)現(xiàn)橫向分辨率突破0.8μm的行業(yè)里程碑。
智能化全流程實(shí)施體系
項(xiàng)目實(shí)施采用"在線式高速檢測(cè)平臺(tái)+離線式實(shí)驗(yàn)室驗(yàn)證"的協(xié)同架構(gòu)。產(chǎn)線端部署的卷對(duì)卷檢測(cè)設(shè)備可實(shí)現(xiàn)每分鐘120米的高速掃描,通過5G-MEC邊緣計(jì)算模塊完成實(shí)時(shí)缺陷分類。實(shí)驗(yàn)室端則配備符合ISO 17025標(biāo)準(zhǔn)的膜厚分析儀與熱機(jī)械性能測(cè)試儀,形成完整的質(zhì)量驗(yàn)證閉環(huán)。在寧德時(shí)代某動(dòng)力電池隔膜產(chǎn)線的應(yīng)用案例中,該體系將單批次檢測(cè)時(shí)間從傳統(tǒng)8小時(shí)壓縮至35分鐘,同時(shí)實(shí)現(xiàn)缺陷數(shù)據(jù)庫與MES系統(tǒng)的雙向數(shù)據(jù)貫通。
行業(yè)應(yīng)用場(chǎng)景與效益分析
在光伏領(lǐng)域,針對(duì)背板膜紫外老化檢測(cè)需求,項(xiàng)目團(tuán)隊(duì)開發(fā)的"加速環(huán)境模擬檢測(cè)艙"可模擬25年戶外輻照衰減過程,其氙燈加速老化測(cè)試數(shù)據(jù)與萊茵認(rèn)證結(jié)果的吻合度達(dá)98.6%。某頭部光伏企業(yè)采用該方案后,材料篩選周期縮短60%,年度質(zhì)量索賠下降2200萬元。在消費(fèi)電子領(lǐng)域,應(yīng)用于折疊屏CPI薄膜的"納米壓痕自動(dòng)檢測(cè)系統(tǒng)",成功將柔性材料的耐彎折測(cè)試良率從89%提升至97.3%,支撐某品牌旗艦機(jī)型實(shí)現(xiàn)200萬次折疊的可靠性突破。
全生命周期質(zhì)量管理體系
項(xiàng)目構(gòu)建的"檢測(cè)設(shè)備-工藝參數(shù)-人員操作"三維質(zhì)量管控模型,涵蓋從原材料入庫到成品出庫的12個(gè)關(guān)鍵控制點(diǎn)。通過部署符合ISO/IEC 17020標(biāo)準(zhǔn)的校準(zhǔn)系統(tǒng),確保檢測(cè)設(shè)備的年穩(wěn)定性誤差不超過0.12%。更值得關(guān)注的是,基于區(qū)塊鏈技術(shù)建立的檢測(cè)數(shù)據(jù)存證平臺(tái),已實(shí)現(xiàn)檢測(cè)報(bào)告的全流程可追溯,在2023年某跨國(guó)貿(mào)易糾紛中,完整舉證鏈為企業(yè)避免逾5000萬元經(jīng)濟(jì)損失。
面向未來,建議行業(yè)重點(diǎn)攻關(guān)三個(gè)方向:一是開發(fā)適用于2μm以下超薄材料的無損檢測(cè)技術(shù),二是建立覆蓋"原料-工藝-環(huán)境"的全要素檢測(cè)標(biāo)準(zhǔn)體系,三是推動(dòng)檢測(cè)設(shè)備與工業(yè)互聯(lián)網(wǎng)平臺(tái)的深度集成。只有通過"技術(shù)迭代+標(biāo)準(zhǔn)建設(shè)+生態(tài)協(xié)同"的三維突破,才能在高端薄膜市場(chǎng)競(jìng)爭(zhēng)中掌握質(zhì)量話語權(quán),助力我國(guó)新材料產(chǎn)業(yè)實(shí)現(xiàn)從規(guī)模領(lǐng)先到技術(shù)領(lǐng)跑的戰(zhàn)略轉(zhuǎn)型。

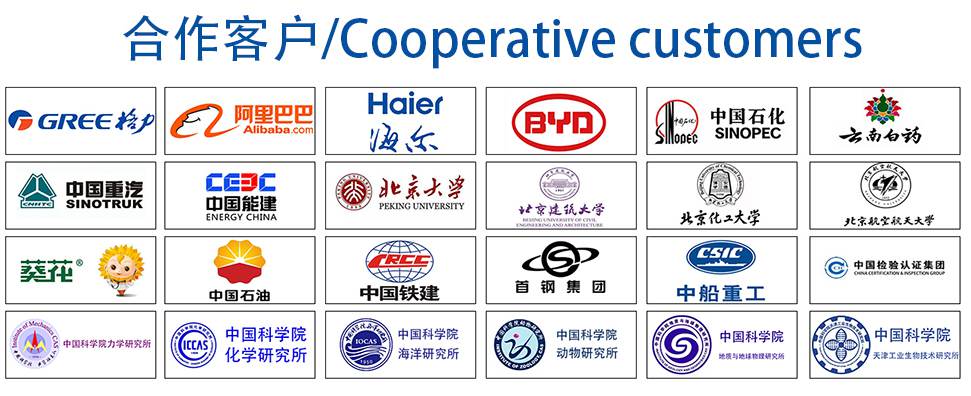