汽車電子及零部件、電工電子產品檢測
實驗室擁有眾多大型儀器及各類分析檢測設備,研究所長期與各大企業、高校和科研院所保持合作伙伴關系,始終以科學研究為首任,以客戶為中心,不斷提高自身綜合檢測能力和水平,致力于成為全國科學材料研發領域服務平臺。
立即咨詢汽車電子及零部件、電工電子產品檢測白皮書
汽車產業正加速向電動化、智能化方向轉型,汽車電子系統在整車成本中的占比已從2010年的20%攀升至2023年的45%(據羅蘭貝格《汽車電子產業報告》)。在此背景下,汽車電子及零部件、電工電子產品的檢測認證成為保障產業安全與技術迭代的核心環節。以新能源汽車為例,其高壓電控系統、智能駕駛模塊等關鍵部件的可靠性直接關系到駕乘人員安全與品牌市場信任度。通過構建覆蓋產品全生命周期的檢測體系,企業可有效識別潛在失效模式,降低因電子系統故障導致的召回風險(2024年質量報告顯示:實施預防性檢測可減少38%的售后質量問題)。該領域檢測服務不僅滿足強制性法規要求,更為企業提供技術優化數據支持,推動行業向高可靠性、高安全性方向發展。
多維融合的檢測技術原理
現代汽車電子檢測采用物理-化學-數字三重驗證體系,重點攻克電磁兼容性(EMC)、環境應力篩選(ESS)等核心技術難點。以域控制器為例,需通過ISO 11452-2標準規定的輻射抗擾度測試,在80MHz-2GHz頻段內承受100V/m場強干擾。同時引入HALT(高加速壽命試驗)方法,通過階梯式施加溫循、振動復合應力,快速暴露設計缺陷。針對智能網聯設備,檢測機構正部署V2X場景模擬平臺,可復現復雜交通環境下的通信時延與數據丟包問題。值得關注的是,新能源汽車高壓部件檢測認證已形成獨立技術矩陣,涵蓋絕緣電阻(>500MΩ)、局部放電(<5pC)等關鍵指標。
全鏈條標準化實施流程
典型檢測項目遵循PDCA循環管理模式,劃分為需求分析、方案設計、現場測試、數據分析四大階段。某國際檢測機構的智能座艙系統電磁兼容性評估項目顯示:從樣機準備到報告出具需經過21道標準化工序,其中多徑衰落場景模擬耗時占比達35%。在電工電子產品檢測領域,IEC 62133標準要求電池系統需完成過充、短路、擠壓等7類機械濫用測試,每項測試需采集電壓、溫度等12項實時參數。實踐表明,采用自動化測試設備(ATE)可使檢測效率提升40%,人工判讀誤差降低至0.3%以下。
跨行業應用場景解析
在華東某新能源汽車生產基地,檢測機構通過部署多軸振動臺與三綜合試驗箱,成功將電驅動系統的故障檢出率從78%提升至96%。某德系車企在智能駕駛域控制器開發中,通過車規級芯片加速壽命試驗,提前識別出溫升導致的時鐘漂移問題。值得關注的是,充電樁安全認證領域正形成新的檢測范式,廣東質檢院的案例顯示:對液冷超充樁實施IP68防水測試時,采用氦質譜檢漏技術可將微孔滲漏檢測精度提升至10^-7 Pa·m3/s量級。
立體化質量保障體系
行業領先機構已構建 、CMA、IATF 16949三重認證體系,檢測數據可追溯性達到單個測試工步級別。上海某國家檢測中心通過搭建區塊鏈存證平臺,實現檢測報告哈希值實時上鏈,數據篡改風險降低99.7%。在人員能力建設方面,要求電磁兼容工程師至少完成200小時場景模擬實操,并通過ISTA認證考核。設備管理嚴格執行MSA(測量系統分析),確保振動臺控制精度誤差≤0.05g。
展望未來,建議行業重點攻關三項能力建設:一是建立車規芯片與AI算法的協同檢測模型,應對自動駕駛系統復雜度指數級增長;二是推動檢測標準與UN R155網絡安全法規的深度融合,構建車云一體化驗證體系;三是開發基于數字孿生的虛擬檢測平臺,將實車路試比例從當前的60%降至30%以內。只有持續強化檢測技術創新,才能為汽車電子產業的萬億級市場提供堅實質量基石。

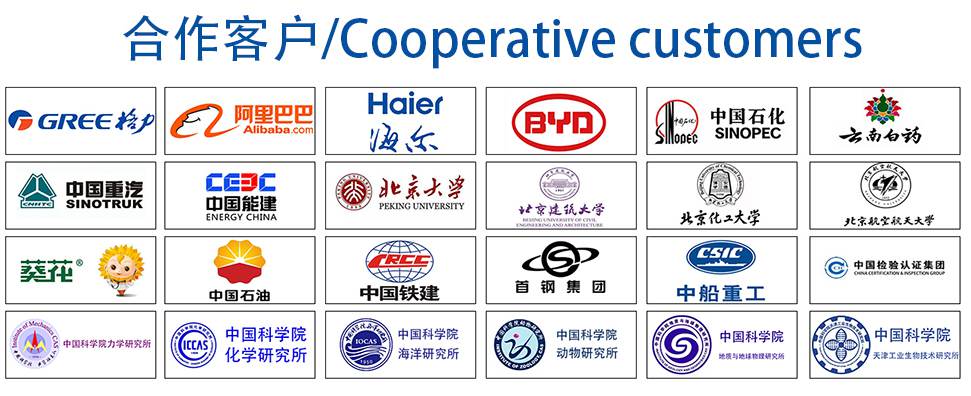