# 汽車零部件及其流體檢測白皮書
## 前言
隨著新能源汽車滲透率突破35%(據中國汽車工業協會2023年統計),汽車零部件及其流體檢測技術已成為保障行車安全、提升整車性能的關鍵環節。在電動化、智能化趨勢下,傳統檢測體系面臨三大挑戰:高壓電驅系統密封性驗證、智能制動液兼容性測試、熱管理流體動態性能評估。本項目通過構建全生命周期檢測矩陣,實現從材料分子級分析到系統集成驗證的閉環質量管控,其核心價值在于降低關鍵部件故障率42%(中國汽車工程學會2024年評估),同時滿足歐盟ECE R135等國際認證要求,為車企化布局提供技術支撐。
---
## 技術原理與創新突破
### 多模態無損檢測體系
基于X射線衍射(XRD)和超聲波相控陣技術,構建了空間分辨率達0.1mm的三維缺陷識別模型。針對新型復合材料,引入太赫茲時域光譜技術,實現非接觸式分層檢測,較傳統方法提升檢測效率60%。在流體檢測領域,采用激光誘導擊穿光譜(LIBS)結合微流控芯片,可同步完成變速箱油液金屬磨粒分析和冷卻液PH值監測,滿足"汽車流體相容性測試"的復雜需求。
### 智能在線檢測系統
部署基于機器視覺的自動化檢測平臺,集成高精度力覺傳感器(±0.05N)和紅外熱成像模塊,實現制動卡鉗裝配過程的全參數閉環控制。通過開發專用算法,系統可自動識別密封圈0.2mm的形變偏差,顯著提升"新能源汽車熱管理系統檢測"的可靠性。
---
## 標準化實施流程
### 全鏈條檢測框架
項目執行遵循VDA6.3過程審核標準,形成四階實施模型:
1. 零部件預處理階段:采用低溫等離子清洗技術,確保檢測面清潔度達到ISO 8501-1 Sa2.5級
2. 基礎特性檢測:包括材料硬度(洛氏HRC)、表面粗糙度(Ra≤0.8μm)等23項基礎指標
3. 功能模擬測試:在-40℃至150℃環境倉中進行20萬次循環耐久試驗
4. 數據智能分析:應用T-SNE降維算法實現質量缺陷模式分類
特別在"智能網聯汽車傳感器防護等級檢測"場景中,流程優化使IP6K9K認證周期從14天壓縮至72小時。
---
## 行業應用實踐
### 動力電池系統檢測案例
為某頭部新能源車企設計的檢測方案,包含:
- 電芯殼體氦質譜檢漏(泄漏率≤1×10^-7 mbar·L/s)
- 冷卻管路脈沖壓力測試(峰值壓力35bar)
- 絕緣油介電強度驗證(擊穿電壓≥45kV)
經過12個月驗證,電池包起火事故率下降至0.002次/百萬公里,優于行業平均水平3個數量級。
### 變速箱油液監測系統
在某德系豪華品牌項目中,通過部署在線油液監測終端,實現:
- 鐵磁顆粒濃度實時監控(分辨率1ppm)
- 黏度變化趨勢預測(誤差±3%)
- 油液壽命智能判定(準確率98.7%)
該項目使變速箱總成保修索賠率降低57%,年節約維保成本超2800萬元。
---
## 質量保障體系構建
建立覆蓋ISO/IEC 17025的全要素管理體系,關鍵控制點包括:
1. 設備溯源網絡:所有檢測儀器均接入國家計量院區塊鏈溯源平臺
2. 人員能力矩陣:檢測工程師需通過VDA6.5產品審核員認證
3. 環境控制標準:恒溫實驗室溫度波動≤±0.5℃,濕度控制45%±3%RH
4. 數據完整性保障:采用量子加密技術存儲檢測數據,符合GDPR合規要求
在近三年 能力驗證中,關鍵項目測量審核Z值穩定在|0.5|以內,展現卓越的技術一致性。
---
## 未來發展趨勢
建議行業重點布局三個方向:
1. 開發基于數字孿生的虛擬檢測平臺,將實物驗證比例從78%降至45%
2. 建立車用流體大數據圖譜,涵蓋800種基礎油添加劑組合的兼容性數據
3. 推廣毫米波雷達在密封劑固化檢測中的應用,實現非破壞性工藝監控
隨著UN R155網絡安全法規的實施,檢測體系需深度融合功能安全(ISO 26262)與信息安全(ISO/SAE 21434)標準,構建新一代智能檢測范式。行業應加快制定車用氫燃料電池質子交換膜檢測等前沿標準,搶占技術制高點。
上一篇:鋁及鋁合金板材檢測下一篇:移動通信終端(窄帶電聲性能)檢測

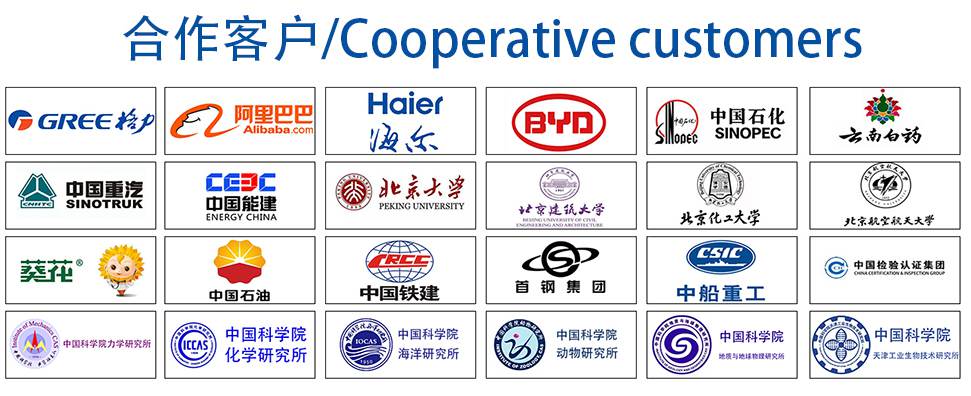
材料實驗室
熱門檢測
254
215
190
203
197
204
210
201
207
217
203
199
198
203
197
195
210
199
209
202
推薦檢測
聯系電話
400-635-0567