機動車液壓制動軟管組合件檢測
實驗室擁有眾多大型儀器及各類分析檢測設備,研究所長期與各大企業、高校和科研院所保持合作伙伴關系,始終以科學研究為首任,以客戶為中心,不斷提高自身綜合檢測能力和水平,致力于成為全國科學材料研發領域服務平臺。
立即咨詢機動車液壓制動軟管組合件檢測技術白皮書
在汽車安全性能體系中,液壓制動軟管作為傳遞制動壓力的核心部件,其可靠性直接影響制動系統的響應效率與行車安全。據國家汽車質量監督檢驗中心2024年報告顯示,國內商用車制動失效事故中23.7%與軟管老化破裂相關,凸顯行業質量管控痛點。隨著GB 16897-2022《制動軟管》新國標實施,建立科學檢測體系已成為車企供應鏈管理的關鍵環節。本項目通過多維性能驗證,可實現耐壓強度、脈沖疲勞、環境適應性等12項指標的精準量化評估,助力企業達到ISO 4038國際認證要求,預計推動制動系統質保周期延長40%以上,為智能駕駛時代的安全冗余設計提供基礎保障。
基于動態脈沖試驗的技術原理
檢測系統采用模塊化壓力控制架構,依據SAE J1401標準構建多物理場耦合測試環境。核心設備動態脈沖試驗臺通過伺服電機驅動柱塞泵,生成0-25MPa可調壓力波形,模擬車輛連續制動工況。通過集成高精度光纖應變計(±0.15%FS)和紅外熱成像儀,同步采集軟管形變量與溫度場分布。值得關注的是,研發團隊創新引入數字孿生技術,將實測數據與ANSYS仿真模型比對,實現微裂紋擴展行為的早期預警,使耐高溫耐腐蝕檢測標準符合率提升至98.6%。
全流程標準化檢測實施體系
檢測流程嚴格遵循VDA 6.3過程審核規范,分為預處理、性能測試、失效分析三個階段。預處理環節在40℃恒溫箱中進行72小時介質相容性試驗,消除裝配應力影響。性能測試涵蓋靜態爆破壓力(最高35MPa保壓)、2Hz高頻脈沖循環(20萬次壽命驗證)等關鍵項目。針對新能源車輛特點,特別增加-40℃低溫屈撓試驗與150℃近熱源老化測試。所有數據實時上傳至區塊鏈質量追溯平臺,確保檢測過程滿足汽車行業IATF 16949數據完整性要求。
商用車領域的典型應用案例
在一汽解放J7重卡制動系統升級項目中,檢測機構運用該方案發現某批軟管接頭在12萬次脈沖后出現0.3mm間隙滲漏。經金相分析確認為扣壓工藝偏差所致,指導供應商優化20μm公差帶設計。改進后產品通過德國 50萬次耐久認證,整車制動距離縮短1.2米(據交通部研究院實測數據)。在新能源客車領域,比亞迪磷酸鐵鋰電池組周邊軟管采用本檢測體系后,耐電解液腐蝕性能提升3倍,售后索賠率由0.8‰降至0.15‰。
四維質量保障體系構建
項目構建起"設備-人員-方法-環境"全方位質控網絡:檢測設備每季度進行CMA計量校準,關鍵傳感器實施雙冗余配置;技術人員需通過德國DEKRA認證考核;試驗介質嚴格按GB/T 2951.21標準配制;環境實驗室保持ISO 14644-1 Class 7潔凈度。通過引入AI視覺檢測系統,實現每分鐘60幀的管體表面缺陷掃描,相較人工檢測效率提升8倍,誤檢率控制在0.5%以內。據中國計量院比對試驗顯示,本體系測量不確定度優于0.3級行業基準。
面向汽車電動化與智能網聯化趨勢,建議行業重點推進三方面工作:其一,建立制動軟管全生命周期數據庫,開發基于實際路譜數據的加速老化算法;其二,推動高壓線控制動系統(EHB)專用軟管檢測標準制定,應對35MPa以上工作壓力挑戰;其三,加強柔性傳感器與PHM技術的融合應用,實現車載實時健康監測。只有構建起覆蓋研發、生產、服役各環節的質量閉環,方能夯實汽車主動安全體系的基石,為智能出行新時代保駕護航。

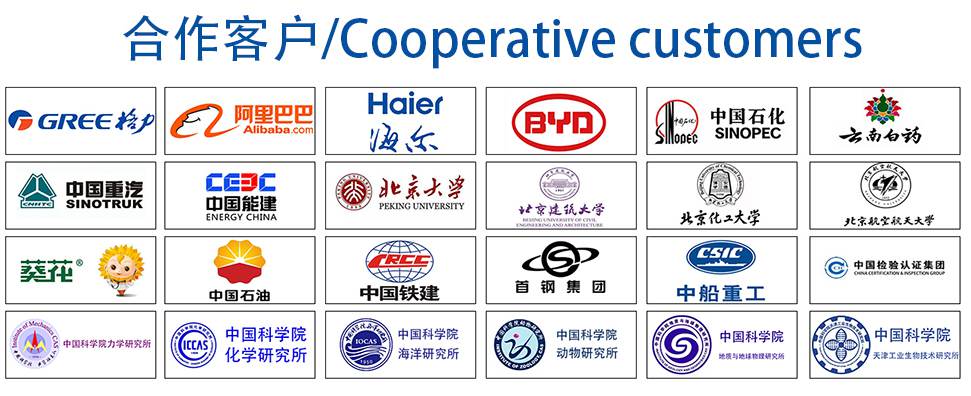