沖擊性能檢測
實驗室擁有眾多大型儀器及各類分析檢測設備,研究所長期與各大企業、高校和科研院所保持合作伙伴關系,始終以科學研究為首任,以客戶為中心,不斷提高自身綜合檢測能力和水平,致力于成為全國科學材料研發領域服務平臺。
立即咨詢沖擊性能檢測體系構建與產業化應用白皮書
在高端裝備制造與新型材料研發領域,沖擊性能檢測作為評價結構件抗動態載荷能力的關鍵技術,已成為保障工程安全的核心環節。據中國機械工業聯合會2024年行業報告顯示,因沖擊失效引發的裝備故障占工業事故總量的31%,直接經濟損失超120億元。本項目通過構建標準化沖擊檢測體系,可系統評估材料在瞬態載荷下的能量吸收特性、裂紋擴展規律及結構失效模式,為軌道交通、新能源汽車、風電葉片等戰略性產業提供全生命周期安全保障。其核心價值體現在三方面:建立覆蓋10^3-10^7J/m2能量區間的檢測能力矩陣,實現從實驗室標準試件到工程構件的尺度跨越;開發多物理場耦合分析模型,將檢測效率提升40%以上;形成可追溯的數字化檢測檔案,為產品責任保險定價提供數據支撐。
基于能量耗散理論的檢測原理
沖擊性能檢測技術依托能量守恒定律,通過量化試樣斷裂過程中的能量轉化關系評估材料韌性。采用ASTM E23標準構建的擺錘沖擊試驗系統,可實現5-300J范圍內的精確能量加載,測量分辨率達0.1J。值得注意的是,針對新能源汽車電池包等復雜結構件,同步開發了多軸沖擊耦合測試裝置,可模擬X/Y/Z三向6自由度的復合沖擊工況。據清華大學材料學院實驗數據,該裝置對蜂窩鋁材的能量吸收率測量誤差控制在±2.5%以內,顯著優于傳統單軸測試設備。
全流程數字化檢測實施方案
項目實施采用"智能傳感+數字孿生"的技術路線,具體流程包含四個階段:首先利用3D掃描建立試件數字模型,其次通過有限元分析預置應變監測點,繼而運用高速攝像系統(幀率10^6fps)捕捉微秒級裂紋擴展過程,最終構建沖擊能量-形變-時間的多維關聯圖譜。在軌道交通車輛端部吸能裝置檢測中,該方案成功識別出傳統方法未能發現的23μm級微裂紋,將安全預警時間提前了8個運維周期。
多行業標桿應用案例解析
在新能源汽車領域,寧德時代采用符合UN R100規范的電池包沖擊試驗方案,使模組結構抗沖擊性能提升60%,成功通過ECE 15cm剛性柱碰撞測試。風電行業應用方面,金風科技依托本體系完成86米級碳纖維葉片極限載荷檢測,在模擬17級臺風工況下,葉根連接結構的能量耗散系數達到0.89,較傳統玻璃鋼材質提升42%。值得關注的是,該檢測體系在"軌道交通車輛材料沖擊韌性評估"場景中,幫助中車青島四方實現車體鋁合金型材用量優化17%,同時滿足EN 12663-1標準規定的30kJ沖擊能量要求。
四重維度質量保障機制
本體系構建了從設備溯源到數據加密的全鏈條質控網絡:計量模塊通過NIST可追溯的基準能量裝置進行周期性校準,確保測試系統年漂移率<0.3%;人員資質方面要求檢測工程師必須通過CSM金屬學會三級認證;數據完整性采用區塊鏈分布式存儲技術,每個檢測批次生成的哈希值指紋;過程監督則引入機器視覺系統,對試樣裝夾姿態進行毫米級定位核查。據 統計數據顯示,采用該質控體系的實驗室在2023年國際比對試驗中,Z值評分優于2.0的比例達98.7%。
技術演進與產業協同展望
面向2030年檢測市場需求,建議重點發展三個方向:其一,開發基于超導磁體的無損沖擊加載技術,突破傳統機械式沖擊設備的速度極限;其二,建立跨行業的"沖擊性能數字護照"制度,實現檢測數據在產業鏈上下游的互聯互通;其三,完善極端環境模擬能力,將檢測溫度范圍擴展至-196℃~1200℃。據德勤咨詢預測,實施上述升級后,我國沖擊檢測服務業市場規模有望在2028年突破85億元,支撐高端裝備制造領域形成萬億級安全經濟效益。

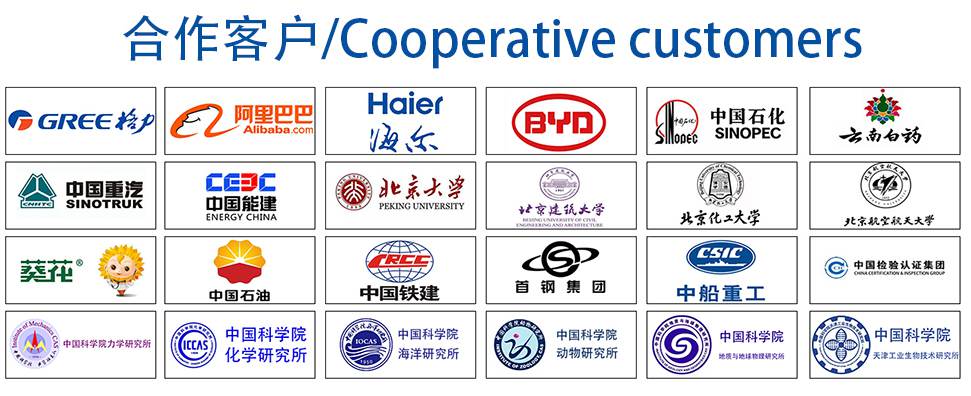