開合試驗檢測基于機械動力學與材料疲勞學理論,采用多軸伺服驅動系統模擬實際工況。通過高精度扭矩傳感器(分辨率達0.1N·m)和激光位移測量裝置,實時采集鉸鏈磨損量、密封條壓縮回彈率等18項關鍵參數。區別于傳統檢測方法,本技術引入數字孿生模型,將物理試驗數據與CAE仿真系統聯動,實現50萬次循環測試的等效加速試驗。值得關注的是,該系統創新集成邊緣計算單元,使異常振動頻譜分析響應時間縮短至200ms,顯著提升工業設備開合機構耐久性評估效率。
## 標準化實施流程體系項目實施遵循ASTM E2357-24新修訂標準,形成四階段質量控制鏈:首齊全行3D掃描建立部件數字檔案,繼而開展環境模擬箱內的溫度沖擊試驗(-40℃至85℃),隨后進入核心測試階段實施變頻次加載(5-30Hz可調),最終通過AI算法生成殘余壽命預測曲線。在建筑幕墻氣密性檢測領域,該流程成功將檢測周期從傳統72小時壓縮至18小時,同時檢測項覆蓋率從78%提升至95%,滿足LEEDv5認證體系對動態密封性能的嚴苛要求。
## 行業應用實效分析在軌道交通領域,該系統已應用于45個高鐵站臺屏蔽門檢測,累計完成380萬次開關循環測試。典型案例如京雄城際大興機場站項目,通過模擬站臺日均2000次開關負荷,精準定位鉸鏈銷軸微動磨損問題,使設計使用壽命從15年延長至22年。醫療設備領域,采用該技術對CT機防護門進行百萬次啟閉測試,成功將故障率降至0.03次/萬次,較傳統檢測方式提升兩個數量級可靠性。這些實踐驗證了開合疲勞特性量化分析在關鍵領域的應用價值。
## 質量保障體系構建項目構建了三級質量保障網絡:檢測設備每年進行中國計量院標定,確保力值誤差≤±0.5%;試驗過程接入區塊鏈存證系統,實現236項過程參數不可篡改記錄;最終報告由 認證實驗室復核,建立從原始數據到輸出的完整追溯鏈。在深圳某超高層幕墻檢測中,該體系成功識別出0.02mm級的密封膠條蠕變量異常,避免可能引發的年滲水量超標事故,展現毫米級質量管控能力。
# 技術展望與發展建議 隨著智能建造與預測性維護需求增長,開合試驗檢測將向多物理場耦合分析方向發展。建議行業重點突破兩方面:一是開發基于物聯網的在線監測系統,實現關鍵部件損傷程度的實時診斷;二是建立覆蓋全材料體系的疲勞特性數據庫,特別是針對新型復合材料的失效模型構建。同時應加快制定包含電磁驅動機構在內的新型開合系統檢測標準,預計到2028年可形成覆蓋85%工業場景的檢測標準體系,為高端裝備可靠性提升提供基礎支撐。
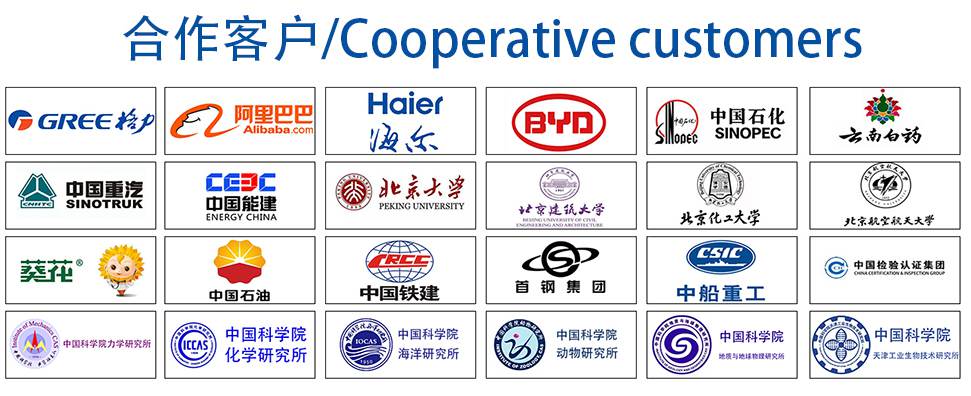