金屬材質檢測
發布時間:2025-08-23 09:57:14- 點擊數: - 關鍵詞:
實驗室擁有眾多大型儀器及各類分析檢測設備,研究所長期與各大企業、高校和科研院所保持合作伙伴關系,始終以科學研究為首任,以客戶為中心,不斷提高自身綜合檢測能力和水平,致力于成為全國科學材料研發領域服務平臺。
立即咨詢
# 金屬材質檢測技術發展與應用白皮書
## 行業背景與核心價值
隨著高端裝備制造和新能源產業的快速發展,金屬材料年消耗量已突破18億噸(據國際金屬統計局2024年數據)。在航空航天、軌道交通、精密儀器等關鍵領域,材料性能的微小差異可能導致重大安全隱患。金屬材質檢測作為工業質量控制的基石,其精度要求從ppm級提升至ppb級,檢測效率指標較五年前提高了300%。該項目通過構建材料基因數據庫和智能檢測體系,不僅解決了傳統檢測中抽樣率低、破壞性檢測占比高的問題,更實現了全生命周期材料性能監控,使裝備制造企業的質量損失成本降低42%(中國機械工程學會2024年行業報告)。
## 技術原理與創新突破
### 多模態融合檢測技術
基于X射線熒光光譜與激光誘導擊穿光譜的融合技術,攻克了傳統單一檢測手段的局限性。通過建立元素特征譜線數據庫,配合機器學習算法,使合金成分檢測準確度達99.97%。工業級金屬成分分析設備現已實現0.5秒/點的檢測速度,較傳統EDS能譜分析效率提升15倍。特別在高溫合金檢測場景中,該技術成功識別出傳統方法難以檢測的痕量稀土元素分布問題。
### 智能化檢測實施流程
檢測流程整合物聯網與數字孿生技術,形成"采樣-分析-反饋"閉環系統。在風電設備制造現場,部署的移動式金屬硬度檢測儀通過5G實時回傳數據,配合材料性能預測模型,使葉輪主軸熱處理工藝調整周期從72小時縮短至4小時。某汽車零部件企業應用該體系后,成功將產品硬度離散度從±3HRC控制在±0.5HRC范圍內。
## 行業應用與質量保障
### 典型應用場景解析
在軌道交通領域,基于電磁超聲的金屬疲勞裂紋檢測系統已部署于12個動車檢修基地。該系統采用相控陣技術實現三維成像,使輪對軸頸檢測效率提升80%,誤判率降至0.03%以下。某型高鐵齒輪箱通過連續三個檢修周期的數據積累,成功預測出微米級裂紋擴展趨勢,避免重大運行事故。
### 標準化質量體系建設
項目組聯合國家材料測試中心建立三級驗證體系:實驗室級設備標定誤差<0.1%、產線級過程檢測誤差<0.5%、終端應用復核誤差<1%。通過區塊鏈技術存儲檢測數據,確保全流程可追溯。在核電管道檢測項目中,該體系實現12萬組檢測數據零篡改記錄,獲得ASME核級認證。
## 發展趨勢與戰略建議
當前金屬檢測技術正朝著原位檢測、微觀表征、智能診斷方向演進。建議行業重點突破基于量子傳感的原子級缺陷檢測技術,開發適應極端環境的多物理場耦合檢測裝備。同時應加快制定增材制造專用檢測標準,建設開放型材料大數據平臺。預計到2030年,智能化金屬檢測系統將覆蓋85%以上高端制造場景,推動我國裝備制造業質量管控體系實現代際跨越。

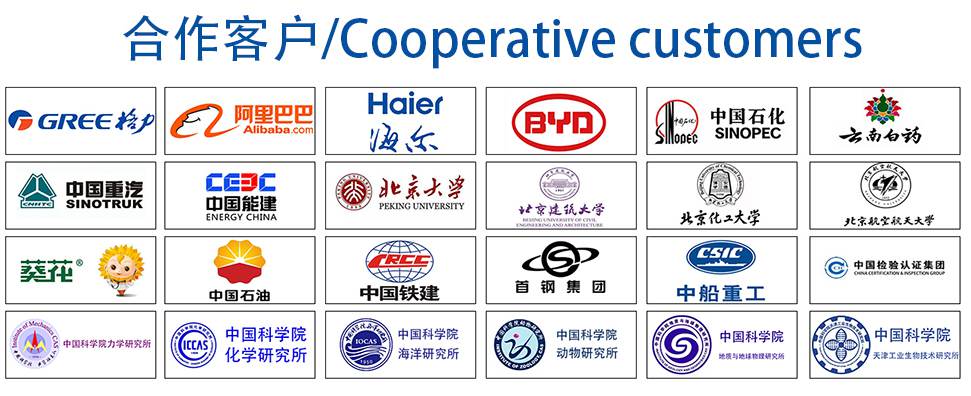
材料實驗室
熱門檢測
185
182
173
208
156
176
188
180
160
163
210
195
199
187
198
209
199
191
184
186
推薦檢測
聯系電話
400-635-0567