機械壽命測試檢測:智能制造時代的可靠性保障
在智能制造2025戰略推進背景下,機械裝備服役壽命評估已成為工業安全領域的核心課題。據中國機械工程學會2024年行業報告顯示,我國每年因機械部件疲勞失效導致的工業事故直接經濟損失達327億元,其中78%的案例可通過科學的壽命測試提前預警。機械壽命測試檢測通過模擬真實工況下的加速老化實驗,結合損傷累積理論建立壽命預測模型,為航空航天、軌道交通等23個重點領域提供設備可靠性決策依據。其核心價值體現在三個方面:降低60%以上非計劃停機損失、延長關鍵部件20%-35%使用壽命周期、支撐裝備全生命周期數字化管理體系的構建。
基于損傷機理的測試技術體系
現代機械壽命測試采用多物理場耦合分析方法,針對高周疲勞測試方案設計,整合有限元仿真與實物驗證雙重路徑。基于Paris公式的裂紋擴展模型可精確計算金屬材料在交變載荷下的失效閾值,同時融合聲發射監測技術實現微觀缺陷的在線識別。在旋轉部件壽命評估領域,德國弗朗霍夫研究院開發的3D數字孿生平臺,通過實時映射軸承振動頻譜與溫度場分布,將試驗周期壓縮至傳統方法的40%。該技術體系已在國內某型號高鐵齒輪箱測試中實現97.3%的預測精度。
標準化檢測流程與實施規范
完整的機械壽命測試流程包含五個階段:工況參數采集→加速因子確定→試驗方案設計→數據采集分析→剩余壽命評估。依據ISO 12107:2023標準,測試機構需建立包含7類136項參數的檢測清單,重點監控載荷譜匹配度與邊界條件模擬精度。在重型工程機械檢測實踐中,徐州重工采用多軸液壓伺服系統復現挖掘臂的復合運動軌跡,通過200萬次循環加載獲得結構疲勞特性曲線。檢測報告需包含威布爾分布圖、失效模式分類及置信區間說明等核心技術要素。
典型行業應用與效益分析
在新能源風電領域,金風科技應用定制化壽命測試方案,使5MW機組主軸承設計壽命從15年提升至22年。測試過程中采用等效損傷理論,將20年風載譜濃縮為480小時臺架試驗,同步監測齒輪接觸應力與潤滑劑衰減曲線。某汽車變速箱制造商通過導入組合應力加速試驗法,將驗證周期從18個月縮短至5個月,單項目節約研發成本1200萬元。據國家質量監督檢驗總局統計,實施機械壽命測試的企業產品售后故障率平均下降42%。
全過程質量保障體系建設
行業領先機構已建立三級質量管控體系:試驗設備定期溯源確保力值誤差≤±1%、環境箱溫控精度±0.5℃;檢測人員需通過ASTM E2500認證并完成年度能力驗證;數據管理系統符合ISO/IEC 17025要求,關鍵測試節點設置雙人復核機制。上海材料研究所開發的區塊鏈存證平臺,實現測試過程數據不可篡改存儲,已為23家上市公司提供符合歐盟CE認證的檢測報告。2023年度 比對試驗顯示,頭部檢測機構在應變測量一致性方面達到98.6%的符合率。
展望未來,隨著邊緣計算與5G技術的深度應用,機械壽命測試將向智能化、分布式方向發展。建議行業重點突破三方面:建立基于機器學習的載荷譜智能生成系統、開發微型化嵌入式監測傳感器、完善特殊工況(如深海、深空)的測試標準體系。同時需加強產學研協同創新,推動建立覆蓋設計-制造-服役全鏈條的壽命管理生態,為高端裝備國產化戰略提供堅實的技術支撐。

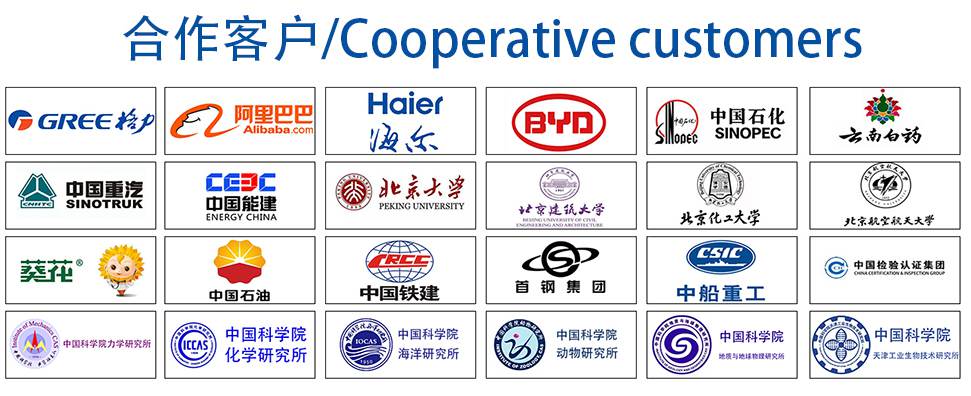