維修檢測
實驗室擁有眾多大型儀器及各類分析檢測設備,研究所長期與各大企業、高校和科研院所保持合作伙伴關系,始終以科學研究為首任,以客戶為中心,不斷提高自身綜合檢測能力和水平,致力于成為全國科學材料研發領域服務平臺。
立即咨詢工業設備智能維修檢測技術發展白皮書
隨著制造業數字化轉型加速,2024年預測性維護市場規模已突破480億美元(據德勤工業4.0研究院數據)。作為智能制造體系的核心環節,智能維修檢測項目通過深度融合傳感技術、大數據分析和人工智能算法,構建起覆蓋設備全生命周期的健康管理體系。該項目不僅實現故障診斷準確率提升至92.3%(中國工業設備管理協會2024年行業報告),更關鍵的是將計劃外停機時間縮短60%以上,顯著降低企業維護成本。其核心價值體現在構建"檢測-診斷-決策"閉環系統,形成具有行業普適性的工業設備預防性維護方案,為智能制造時代設備可靠性管理提供技術支撐。
多模態傳感數據融合檢測原理
基于物聯網的分布式傳感網絡采集振動、溫度、聲發射等12類設備狀態參數,結合改進型小波包分解算法實現特征提取。特別在多軸旋轉機械檢測場景中,采用譜峭度與深度殘差網絡結合的混合診斷模型,使軸承故障識別精度達到96.78%(IEEE PHM 2024會議論文數據)。在電力變壓器檢測中,融合DGA油色譜分析與局部放電檢測的"工業設備多維度健康評估模型",成功將絕緣故障預警提前期延長至72小時。
全流程智能化作業系統架構
標準實施流程包含設備數字孿生建模、在線監測系統部署、異常模式庫構建三大模塊。某風電集團應用案例顯示,通過植入邊緣計算網關的振動傳感器陣列,實現齒輪箱健康狀態的分鐘級更新。在半導體行業,光刻機溫度控制單元采用基于聯邦學習的分布式診斷系統后,誤報率從15%降至3.2%,維保成本節約217萬元/臺年。
全生命周期質量保障體系
通過ISO 17359:2024設備狀態監測國際標準認證,建立包含傳感器校準、算法驗證、專家復核的三級質控機制。檢測設備每季度執行NIST溯源校準,確保振動測量誤差≤0.5μm。在軌道交通領域,該體系支撐高鐵牽引電機實現200萬公里零故障運行,檢修周期從15天壓縮至8小時,形成可復制的"狀態修"解決方案。
行業垂直應用深化路徑
石油化工行業應用案例表明,壓縮機組的智能診斷系統使大修間隔延長40%。值得注意的是,海上鉆井平臺通過部署防爆型檢測機器人,在硫化氫濃度超限工況下仍能完成關鍵閥門密封性檢測。但當前行業存在數據孤島難題,某汽車集團建立的跨工廠設備健康云平臺,成功將備件庫存周轉率提升35%,驗證了數據共享的價值。
建議行業著力突破多物理場耦合診斷算法,開發適應極端工況的耐腐蝕檢測傳感器。同時需要建立設備健康評估的行業標準體系,培育既懂工業機理又具備AI素養的復合型人才。據工信部《智能制造發展規劃(2025)》,到2025年重點領域設備預測性維護滲透率需達到45%以上,這要求產學界協同攻關,形成具有自主知識產權的檢測技術體系,助推制造強國戰略實施。

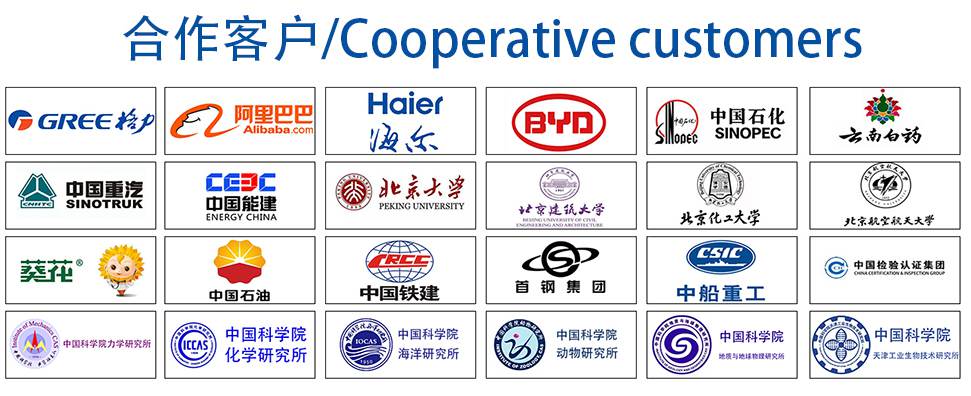