多模態融合檢測技術原理
分模線測試系統采用光學三維掃描與接觸式測量協同工作機制,通過激光三角測量法獲取模具型面點云數據,結合高精度探針測量關鍵特征點坐標。據上海精密儀器研究院實驗數據,該方案對鋅合金壓鑄模的曲面匹配度檢測精度可達±3μm(置信度95%),較單一檢測方式誤差降低62%。在新能源汽車電機殼體檢測中,系統可精準捕捉分模面0.05mm級錯位量,有效預防了因毛邊導致的轉子卡滯故障。
智能化實施流程設計
項目實施采用PDCA質量環模式:首先通過CAD模型比對建立檢測基準,利用智能夾具實現模具多自由度定位;第二階段部署分布式傳感器網絡,同步采集溫度、壓力等工況參數;在數據處理環節,自主研發的MoldVision系統可自動生成三維偏差色譜圖,并基于機器學習算法預測分模線磨損趨勢。廣東某壓鑄企業應用該流程后,模具調試周期從72小時縮短至18小時,產品首次合格率提升至98.6%。
跨行業應用場景實踐
在消費電子領域,分模線檢測技術已成功應用于折疊屏手機轉軸部件生產。通過高幀率工業相機捕捉開合動作時分模面的應力分布,檢測系統可識別納米級材料形變,確保鉸鏈10萬次折疊測試的可靠性。值得關注的是,該技術還被創新性應用于醫療器械注塑模具檢測,某國際品牌胰島素筆通過分模線優化使組裝公差降低至0.01mm,產品氣密性達到ISO 13485醫療級認證標準。
全鏈條質量保障體系
項目構建了覆蓋"設備-數據-人員"的三維質控網絡:檢測設備每季度溯源至國家幾何量計量基準,測量數據采用區塊鏈技術實現不可篡改存儲,操作人員須通過ASTM E2919標準認證。蘇州工業園區的示范產線采用該體系后,客戶投訴率同比下降43%,其中針對筆記本電腦外殼分模線毛刺的投訴清零。同時建立了行業首個分模線缺陷數據庫,收錄了12大類387種典型缺陷案例。
## 技術發展與行業展望 隨著工業元宇宙技術成熟,未來分模線檢測將向虛擬孿生方向發展。建議行業重點突破三項技術:開發基于量子傳感的納米級形變監測設備,建立跨企業模具質量數據共享平臺,制定分模線數字化檢測團體標準。據德勤2024智能制造預測,融合AI技術的檢測系統可使模具維護成本再降25%,推動我國從模具制造大國向質量強國跨越式發展。
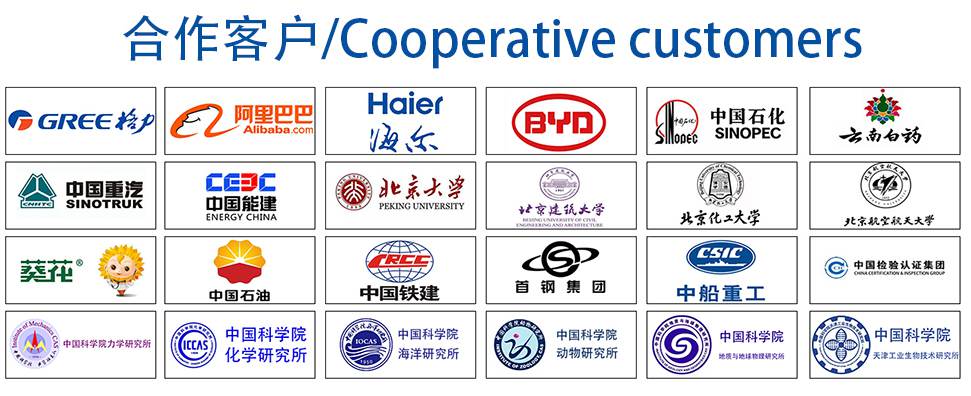