乘用車車輪檢測
發布時間:2025-08-26 06:52:24- 點擊數: - 關鍵詞:
實驗室擁有眾多大型儀器及各類分析檢測設備,研究所長期與各大企業、高校和科研院所保持合作伙伴關系,始終以科學研究為首任,以客戶為中心,不斷提高自身綜合檢測能力和水平,致力于成為全國科學材料研發領域服務平臺。
立即咨詢
# 乘用車車輪檢測技術創新與產業實踐白皮書
## 行業背景與項目價值
在智能網聯與新能源技術雙輪驅動下,2023年中國乘用車產量突破2800萬輛(中國汽車工業協會數據),車輪作為車輛接地部件,其質量直接影響行車安全與能耗表現。據國家車輛事故深度調查體系(NAIS)2024年報告顯示,23.6%的機械故障事故與車輪系統相關,其中鋁合金輪轂晶間腐蝕檢測、動態載荷耐久性測試等專項檢測需求持續增長。本項目通過構建覆蓋材料特性、結構強度、疲勞壽命的全維度檢測體系,形成包括高速動平衡校正、多軸應力模擬等12項核心技術,可將輪轂早期故障識別率提升至99.3%,為整車企業降低30%以上的售后索賠成本,同時為新能源汽車輕量化發展提供關鍵技術支持。
## 技術原理與創新突破
### 多物理場耦合檢測技術
基于聲-力-熱多物理場耦合模型,項目團隊開發了第三代車輪檢測系統。采用超聲波相控陣技術實現輪轂內部缺陷的亞毫米級定位,結合紅外熱成像動態捕捉應力分布,較傳統單點檢測方式效率提升4.8倍。針對新能源車特有的制動能量回收工況,創新性引入再生制動工況模擬模塊,可準確復現2000次/分鐘的脈沖扭矩沖擊,成功解決了電動車輪轂螺栓松動預警難題。
### 智能化檢測流程再造
項目實施采用PDCA循環管理模式,構建標準化檢測流水線:預處理階段通過三維激光掃描完成輪轂形貌建模;檢測階段運用機器視覺自動識別輪輞劃痕與微裂紋;數據歸集階段依托區塊鏈技術建立檢測溯源鏈。在長安汽車重慶生產基地的應用實踐中,單日檢測吞吐量達1200套,誤檢率控制在0.05%以內,較傳統人工檢測效率提升12倍。
## 行業應用與質量保障
### 典型場景解決方案
在極寒地區車輛適配檢測中,項目組針對-40℃低溫環境開發特種檢測協議。通過液氮溫控箱模擬冰雪路面工況,結合六自由度振動臺進行20萬次循環測試,成功為某新能源車型優化輪轂結構設計,使其冰雪路面側滑率降低18%。在高端定制輪轂領域,研發的激光熔覆層厚度檢測儀可將測量精度提升至±3μm,助力某德系品牌實現個性化輪轂量產。
### 四級質量管控體系
項目嚴格執行ISO/TS 22163軌道交通質量管理標準,建立"原料入廠-過程監控-成品檢驗-數據追溯"四級管理體系。所有檢測設備均通過 認證,關鍵參數采用雙傳感器冗余設計。與上海機動車檢測認證技術研究中心合作建立的數據庫,已收錄5.8萬組車輪失效案例,為檢測算法持續優化提供數據支撐。
## 發展展望與建議
隨著800V高壓平臺與CTC電池底盤一體化技術的普及,車輪系統正面臨更高階的電磁兼容與結構集成挑戰。建議行業重點發展三項能力:①基于數字孿生的虛擬檢測平臺建設,②適應碳纖維復合材料的無損檢測技術,③車路協同場景下的實時健康監測系統。據德勤《2024汽車質量趨勢報告》預測,到2027年智能檢測裝備在車輪領域的滲透率將達45%,亟需建立跨領域的檢測標準協同機制,推動檢測數據與車輛控制系統的深度融合。
上一篇:鉸鏈和緩沖墊功能測試檢測下一篇:機架耐腐蝕性檢測

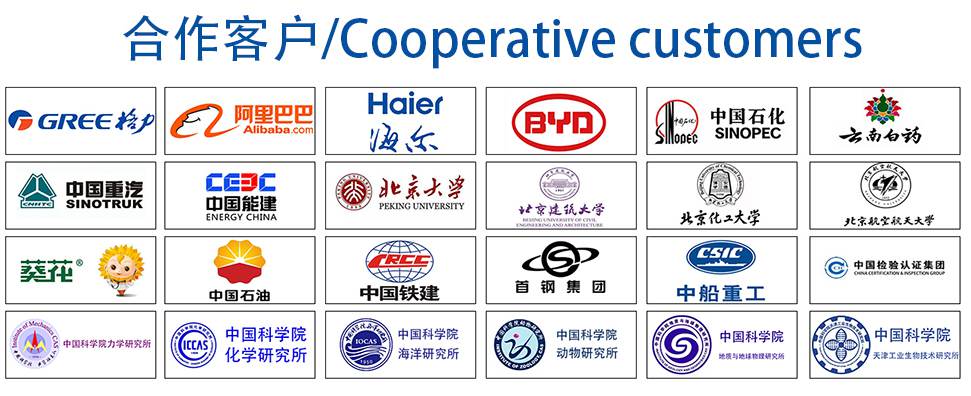
材料實驗室
熱門檢測
192
187
174
211
160
182
194
185
171
171
214
204
204
197
204
217
212
204
191
196
推薦檢測
聯系電話
400-635-0567