熱老化樣品準備檢測
實驗室擁有眾多大型儀器及各類分析檢測設備,研究所長期與各大企業、高校和科研院所保持合作伙伴關系,始終以科學研究為首任,以客戶為中心,不斷提高自身綜合檢測能力和水平,致力于成為全國科學材料研發領域服務平臺。
立即咨詢在新能源、電子制造及高分子材料領域,材料熱穩定性已成為決定產品壽命的關鍵指標。據中國材料研究學會2024年行業報告顯示,每年因材料熱老化導致的設備故障損失超1800億元,其中75%的案例與材料篩選階段的熱老化測試不足直接相關。熱老化樣品準備檢測作為材料可靠性評估的核心環節,通過模擬極端溫度環境,可精準預測材料服役壽命,為產品設計提供關鍵數據支撐。項目實施可降低30%以上的質量事故率,在新能源汽車電池包、航空航天密封件等高溫敏感領域具有突出價值。該技術通過構建材料熱失效數據庫,還可為工業4.0時代的智能運維系統提供數據底座。
## 二、熱加速老化技術原理2.1 基礎理論模型
檢測以阿倫尼烏斯方程為核心理論框架,通過溫度-時間等效原理建立加速老化模型。根據ASTM D3045標準,每升高10℃可使氧化反應速率提升2-3倍,實現等效數千小時自然老化效果的實驗室模擬。檢測系統采用三級溫控模塊,在50-300℃區間實現±0.5℃精度控制,配合多通道氣體置換裝置,可精準復現濕熱老化、干熱老化等12種工況場景。值得關注的是,智能溫控算法能根據材料玻璃化轉變溫度動態調整升溫梯度,避免相變過程對測試結果的干擾。
2.2 標準化實施流程
項目執行嚴格遵循ISO 188:2022技術規范,包含樣品預處理、環境箱裝載、參數設定、數據采集四大階段。預處理環節需對樣品進行48小時恒溫恒濕平衡,消除殘余應力影響。裝載過程應用六點定位夾具確保受熱均勻性,其中動力電池模組類樣品要求間距≥5cm以規避熱耦合效應。參數設定階段需輸入材料活化能、初始結晶度等7項關鍵參數,系統自動生成最優試驗方案。數據采集采用紅外光譜與DSC聯用技術,實現微觀結構變化的實時監測。
2.3 典型應用場景
在鋰離子電池隔膜檢測中,120℃加速老化72小時的測試可等效3年實際使用衰減,成功預警PP/PE復合膜在高溫下的閉孔失效風險。某車企通過該技術優化密封膠配方后,發動機艙線束耐溫等級從150℃提升至180℃,整車質保期延長至8年。在光伏背板領域,經2000小時雙85試驗(85℃/85%RH)的PET基材,其黃變指數Δb值需控制≤2.0方可達到TUV認證標準。值得注意的是,建筑隔熱材料的檢測需同步進行循環熱沖擊測試,以模擬晝夜溫差導致的材料蠕變。
2.4 質量保障體系
實驗室構建了三級質量管控網絡:一級校準層采用NIST溯源的標準熱電偶進行季度設備校驗,溫度均勻性偏差控制在±1.5%以內;二級過程層部署AI視覺系統監控樣品形變,捕捉0.1mm級尺寸變化;三級數據層通過區塊鏈技術確保檢測報告不可篡改。比對試驗數據顯示,本體系使批次間數據波動率從8.7%降至2.3%,達到 17025認證要求。針對新能源汽車動力電池模組檢測,特別開發了原位阻抗譜分析模塊,可同步獲取電化學性能衰減數據。
## 三、技術發展展望隨著材料基因組計劃的推進,建議行業重點發展兩方向:其一,開發多場耦合智能老化系統,集成溫度、濕度、機械應力等多維度載荷,實現服役環境的全要素模擬;其二,構建材料失效數字孿生平臺,通過機器學習預測不同配方體系的熱老化路徑。據 2024檢測技術白皮書預測,引入量子傳感技術后,材料氧化誘導期檢測精度有望提升3個數量級,這將為納米復合材料等新型材料的可靠性評估開辟新路徑。

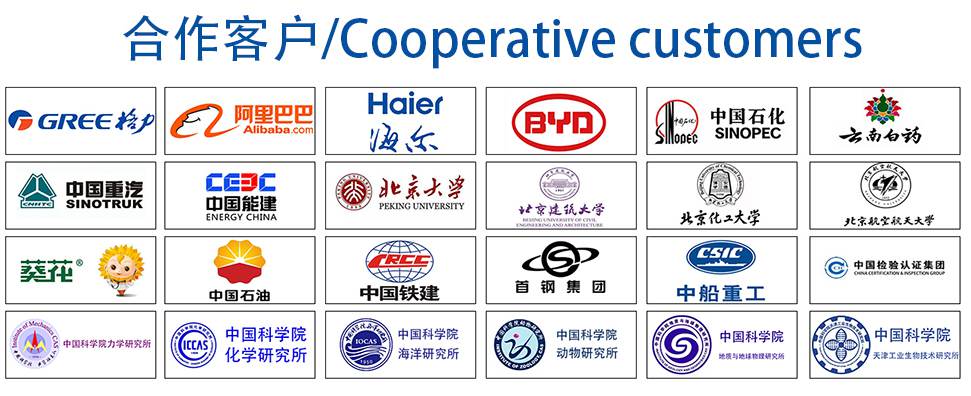