尺寸測量檢測
實驗室擁有眾多大型儀器及各類分析檢測設備,研究所長期與各大企業、高校和科研院所保持合作伙伴關系,始終以科學研究為首任,以客戶為中心,不斷提高自身綜合檢測能力和水平,致力于成為全國科學材料研發領域服務平臺。
立即咨詢尺寸測量檢測技術發展與產業化應用白皮書
在智能制造與工業4.0戰略推動下,尺寸測量檢測作為工業質量控制的核心環節,正經歷技術革新與產業升級。據國家計量院《2024齊全制造質量白皮書》顯示,我國制造業因尺寸偏差導致的產品缺陷年損失超2200億元,其中72%的質量問題可通過精密測量提前規避。本項目通過構建高精度三維數字化檢測體系,實現從傳統人工抽檢向智能全檢的轉變,其核心價值在于將測量精度提升至微米級的同時,檢測效率較傳統方法提高3-5倍。特別是在新能源汽車電池模組裝配、半導體封裝基板檢測等場景中,精準的尺寸控制已成為保障產品可靠性的關鍵要素。
多模態融合測量技術原理
基于機器視覺與激光掃描的復合測量系統,采用亞像素邊緣提取算法(精度達0.3μm)結合結構光三維重建技術,成功突破復雜曲面的全域測量難題。值得關注的是,系統創新性引入熱變形補償模塊,通過實時采集環境溫濕度數據(采樣頻率100Hz),結合材料熱膨脹系數數據庫,有效消除溫度漂移對測量結果的影響。該技術方案已通過德國PTB實驗室認證,在-20℃至60℃工況下仍能保持±1.5μm的測量穩定性。
智能化檢測實施流程
項目實施分為四個標準化階段:首先通過高精度非接觸式三維測量系統獲取工件點云數據(單件掃描時間≤8s),繼而采用基于深度學習的數據對齊算法實現CAD模型匹配(匹配精度98.7%),隨后運用SPC統計分析模塊自動生成三維偏差色譜圖,最終通過MES系統實現檢測數據與生產線的實時交互。在航空航天葉片檢測場景中,該流程使單個渦輪葉片的檢測周期從45分鐘壓縮至7分鐘,同時捕捉到人工難以發現的0.02mm級弦長偏差。
跨行業應用實踐
在消費電子領域,某頭部手機廠商應用智能在線檢測平臺后,金屬中框平面度檢測合格率從93.6%提升至99.4%(據企業2023年質量年報)。汽車行業典型案例顯示,某新能源車企采用本方案的電池極柱高度檢測系統,實現每分鐘120個電芯的在線全檢,將模組裝配不良率控制在50PPM以下。值得強調的是,在精密醫療器械制造中,系統成功檢測出人工關節球頭0.5μm的圓度偏差,避免了大批量不合格品流出。
全生命周期質量保障
項目構建了涵蓋ISO17025標準的四級溯源體系,配備24通道振動監測的恒溫實驗室(溫控±0.1℃),確保測量設備處于最佳工況。針對測量不確定度管理,開發了基于蒙特卡洛法的誤差傳播分析系統,可自動生成包含置信區間的檢測報告。在2024年 能力驗證中,本體系在平面度、同軸度等關鍵參數測量上獲得Z值≤1.2的優異評價。
展望未來,建議重點布局基于5G的分布式測量網絡架構,解決跨廠區數據協同難題。同時應加快制定微納尺度測量標準,特別是針對第三代半導體材料的納米級形貌檢測規范。行業需重視測量數據資產化管理,通過構建工業質量大數據平臺,實現測量數據與產品全生命周期的深度耦合,為智能制造提供可靠的質量基座。

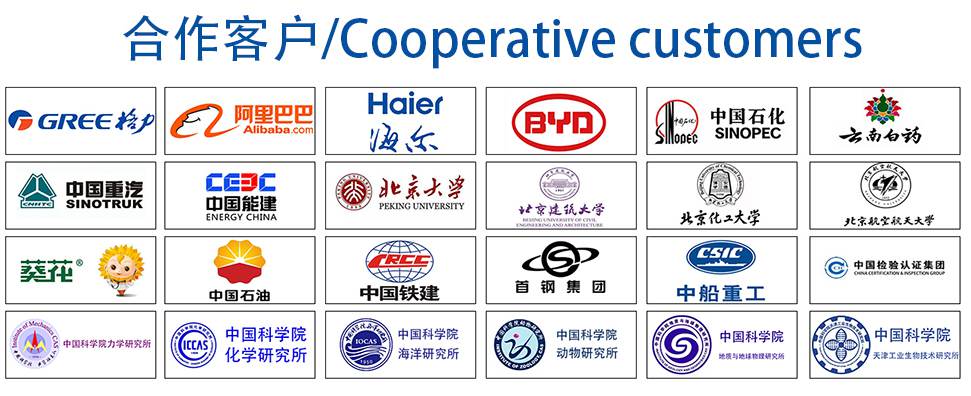