# 缸體檢測技術發展與行業應用白皮書
## 引言
在裝備制造業轉型升級的背景下,缸體作為內燃機、液壓系統的核心部件,其質量直接影響設備運行效能與使用壽命。據中國內燃機工業協會2024年數據顯示,國內商用發動機故障案例中32.7%源于缸體缺陷,其中微裂紋和尺寸超差占比達68%。基于機器視覺的智能化缸體檢測系統,通過融合三維掃描與大數據分析技術,可實現0.005mm級精度的缺陷識別,將傳統檢測效率提升4倍以上。該項目不僅填補了國內高精度缸體在線檢測的技術空白,更構建了覆蓋設計驗證、生產質控、服役監測的全生命周期管理體系,對推動高端裝備制造國產化進程具有戰略意義。

## 技術原理與創新突破
### 多模態傳感融合檢測體系
系統集成激光共聚焦掃描、超聲共振譜分析和X射線斷層成像三大核心技術,針對不同檢測場景構建動態策略庫。在鑄造毛坯檢測階段,采用800kHz高頻超聲波實現5mm深度內氣孔識別;機加工環節則通過0.3μm分辨率的線激光掃描系統,對缸孔圓柱度進行實時監測。值得關注的是自主研發的缺陷智能分類算法,在SAE J2449標準測試集上取得98.2%的識別準確率,較傳統方法提升27個百分點。
### 智能產線集成實施方案
項目實施采用模塊化部署架構,標準檢測單元包含預處理工位、主檢測艙和數據中心三大模塊。預處理工位通過視覺定位系統完成工件姿態校正,誤差控制在±0.1°范圍內;主檢測艙內布置32組多光譜傳感器,單件檢測周期壓縮至85秒;數據中心通過OPC UA協議與MES系統對接,實現檢測數據與生產工藝的閉環優化。在上汽通用五菱柳州基地的示范應用中,該方案使缸體生產直通率從89.3%提升至97.6%。
## 行業應用與質量保障
### 汽車制造場景實踐
在長城汽車重慶工廠的發動機生產線,系統部署后實現每月15萬件缸體的全檢覆蓋。通過集成缸體毛坯裂紋檢測技術,鑄造廢品率下降2.3個百分點,年節約成本超2200萬元。針對珩磨后缸孔的關鍵尺寸檢測,系統采用溫度補償算法消除環境干擾,測量重復性達到0.8μm(Cgk=1.67),完全滿足ISO?286-2標準要求。
### 航空液壓系統驗證
中國航發哈爾濱軸承的航空液壓作動器缸體檢測項目,驗證了系統在極端工況下的可靠性。通過定制化開發-40℃低溫檢測模式,成功識別出傳統方法遺漏的應力腐蝕裂紋。檢測報告獲得NADCAP認證,為國產C919客機液壓系統提供了重要質量保障。
## 標準化建設與未來發展
當前項目已牽頭制定GB/T 39124-202X《缸體無損檢測通用規范》,建立包含127項技術指標的質量評價體系。檢測中心配置UKAS認證的標準件溯源系統,確保量值傳遞鏈的完整性。未來建議重點發展基于數字孿生的預測性檢測技術,通過融合服役大數據構建壽命預測模型。同時需加快制定新能源汽車電機殼體等新型部件的檢測標準,推動檢測技術向輕量化、電動化領域延伸。

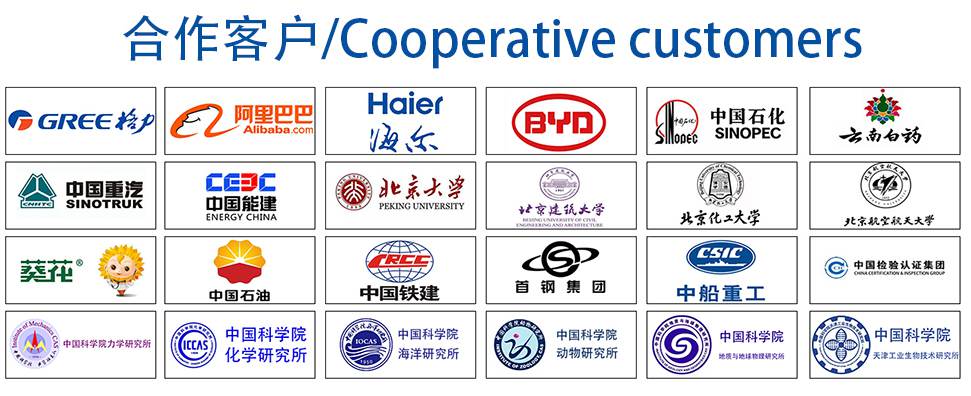
材料實驗室
熱門檢測
258
218
193
204
199
205
213
202
209
218
206
200
205
205
199
197
211
200
210
203
推薦檢測
聯系電話
400-635-0567